AUTOMATISERING HAALDE
PRODUCTIELIJN TERUG NAAR BELGIE
RF-TECHNOLOGIES LEVERDE GECOMBINEERDE INSPANNINGEN
Je kan als bedrijf op meerdere manieren concurrentie uit lagelonenlanden counteren: je kan inspelen op de betere kwaliteit van je producten, je kan automatiseren om meer productie-output te realiseren met dezelfde middelen, of je kan kortere levertermijnen proberen door te voeren. Bij Rf-Technologies combineerden ze deze drie pijlers, maar ze verloren daarbij het welbevinden van de werknemers niet uit het oog. De gecombineerde inspanningen leverden het bedrijf onlangs een Factory of the Future Award op.
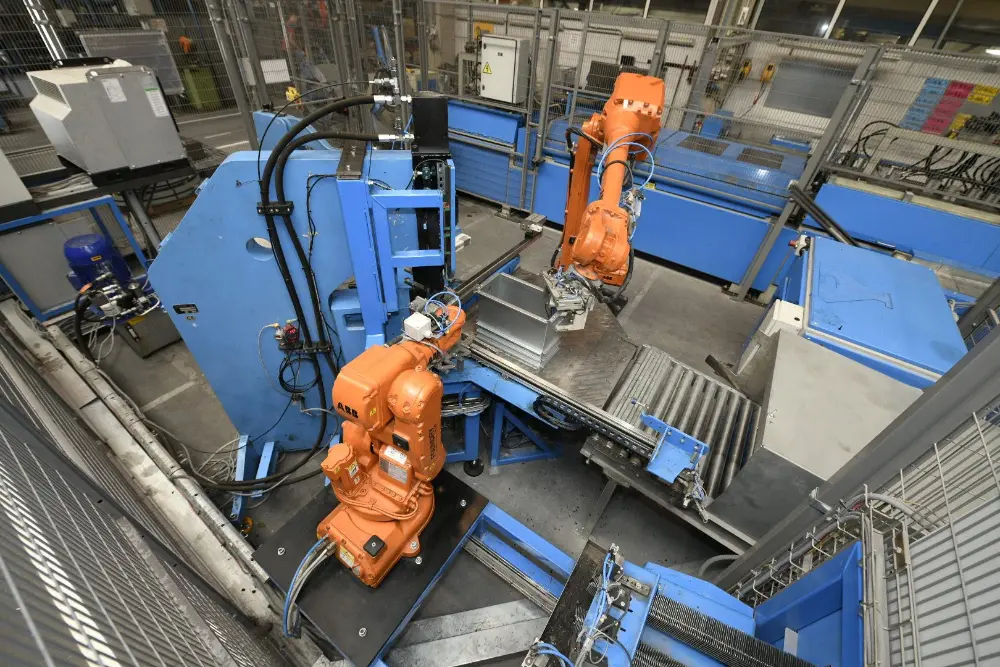
FOCUS OP DRIE TRANSFORMATIES
Het Factory of the Future-programma van Agoria is gestoeld op in totaal zeven transformaties. Om een Factory of the Future te worden, kan elk bedrijf deze transformaties overlopen om te achterhalen waar zij op kunnen werken. Bij Rf-Technologies - producent van oplossingen voor passieve brandveiligheid (zie kaderstuk) - waren dat vooral 'world class manufacturing', 'digital factory' en 'smart production systems', met daarnaast ook een belangrijke rol voor 'networked factory' en 'human centered production'. Jürgen Van De Velde, operations manager van het bedrijf, gidst ons door de verschillende projecten.
WORLD CLASS MANUFACTURING
“We maakten een technologische roadmap op, dat is een document dat dient als verdere basis voor onze technologische ontwikkeling," steekt Van De Velde van wal. “De informatie verzamelen we dankzij ons netwerk: tijdens bedrijfsbezoeken, op beurzen, in magazines, op netwerkbijeenkomsten, tijdens opleidingen, noem maar op. Vier keer per jaar overlopen de operationele verantwoordelijken en de IT-dienst dit document, waarbij we bekijken wat er interessant kan zijn voor ons, hoe lang de terugverdientijd is en wat de gevolgen zijn op korte en lange termijn. Op basis daarvan beslissen we dan jaarlijks welke zaken we willen en kunnen realiseren."
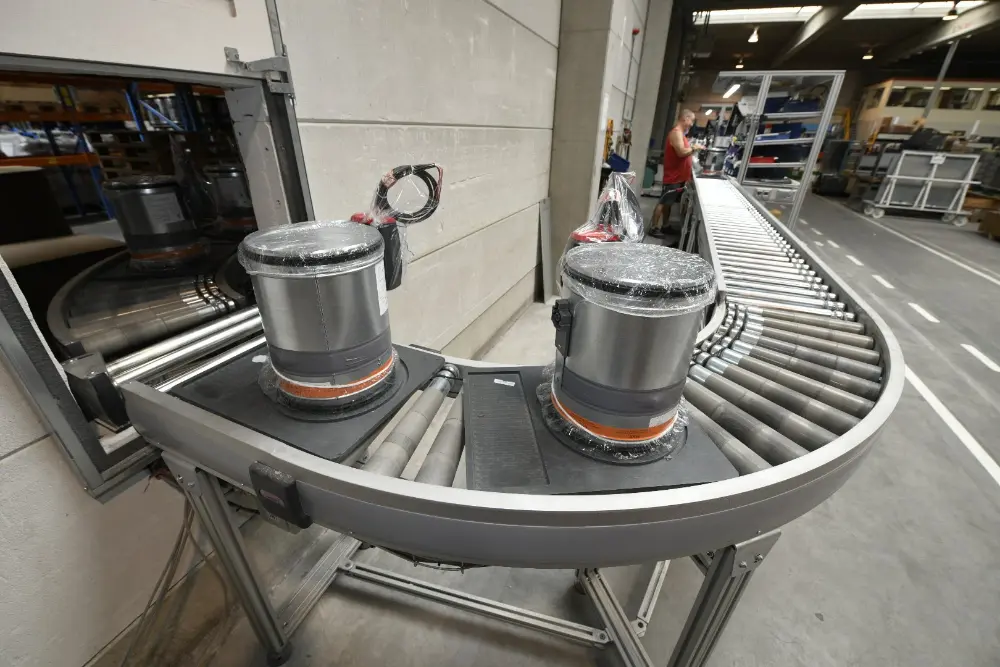
Automatisering
“Een van de opvallendste realisaties is automatisering. Een eerste voorbeeld hiervan is een machine die werkt op basis van een visiesysteem. De camera detecteert welk stuk er ligt, die informatie wordt vervolgens gecommuniceerd naar de volgende twee units. Die stemmen daar hun acties op af, zoals bv. welke strook er moet worden aangebracht. De output van die machine is ongeveer 130 stuks per dag. Vroeger gebeurde dat manueel met zes personen, vandaag nog met vier. Ook in onze metaalafdeling werd een belangrijke automatisering doorgevoerd, hier met twee robots. Vroeger konden met vier personen per ploeg max. 110 stuks gemaakt worden, vandaag kan één persoon maar liefst 300 stuks produceren. Deze investering is zeer belangrijk geweest, want deze zorgde ervoor dat we kunnen voldoen aan de stijgende vraag." “Vroeger bereidden we dit product voor in onze vestiging in Slowakije, maar net dankzij deze automatisering konden we die lijn terughalen naar ons land. Er loopt momenteel ook een thesis bij ons rond de opportuniteiten voor cobots in onze setting. Ik ben vooral benieuwd of een traditionele robot het pleit zal winnen in de applicaties waarvan wij verwachten dat een cobot beter zal zijn. Afwachten maar wat het resultaat zal zijn."
Cr60 lijn
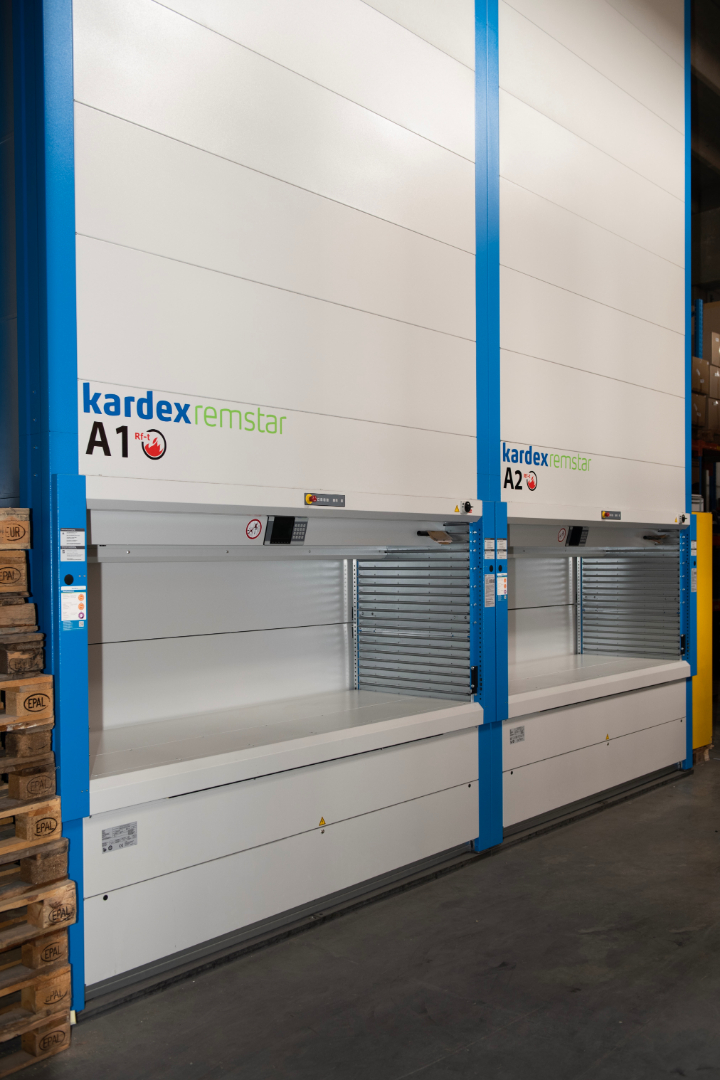
Een ander mooi voorbeeld is de installatie van de CR60-lijn. Hier vertelt productieleider Nico Meuleneire ons over het project: “Die lijn werkt volledig paperless. Eerst wordt via RFID uitgelezen om welke brandklep het exact gaat, vervolgens krijgt de operator op een scherm automatisch de instructies voor het specifieke stuk. Die kunnen divers zijn: een etiket kleven, een mechanisme bevestigen of een strip aanbrengen. Er is ook de mogelijkheid om foto's of instructievideo's weer te geven om het de operator nog makkelijker te maken. Het aantal varianten dat we met één lijn kunnen maken, is in principe oneindig mits aanpassing in ons SCADA-systeem. De bedoeling is dat we dit systeem verder implementeren in andere assemblagelijnen."
Picking in magazijn
Een vlotte productie staat of valt met een goede aanvoer van goederen. Een SWOT-analyse bracht interessante informatie aan het licht. Jürgen Van De Velde licht toe: “Die analyse werd gedaan omdat we kampten met ruimtegebrek. Daarom werd geïnvesteerd in twee Kardex-toestellen met een automatisch pointersysteem voor het picken van de onderdelen. Die investering wordt binnenkort uitgebreid met nog eens 6 toestellen. Uit dezelfde analyse bleek ook dat er te veel loopafstanden van magazijniers nodig waren. Dankzij het gebruik van een AGV is dat nu verholpen."
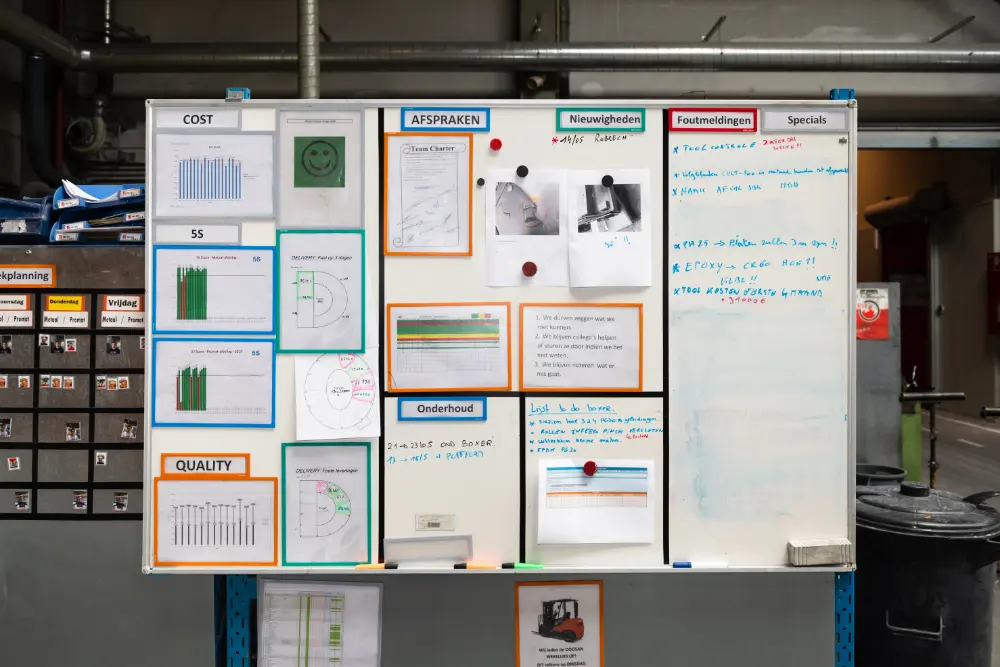
HUMAN CENTERED PRODUCTION
Nico Meuleneire vertelt ons meer over deze pijler: “Een tweetal jaar terug ging een teamleider een nieuwe uitdaging aan. Dat was voor ons de aanleiding om te bekijken hoe we ons menselijk kapitaal beter konden inzetten. We wilden een efficiëntere inzetbaarheid, meer autonomie en meer tevredenheid. Die inzetbaarheid was een absolute voorwaarde om richting kortere levertermijnen te gaan. Bij verlof van een werknemer, moet iemand anders zijn taak kunnen overnemen. Een eerste stap was het oplijsten van elke taak - zeer specifiek - die moet worden uitgevoerd op elke machine. Eens deze zogeheten Fleximatrix af was, konden alle operatoren zelf hun eigen score op elke taak aanvullen. Dat geeft een prima leidraad om de kennis van je mensen in kaart te brengen. Het is ook een zeer goed element in de opleiding van nieuwe werknemers. Maar soms hebben kleine ingrepen even goed een grote impact op de werking. Zo werkt een van onze afdelingen in een tweeploegenstelsel. Vroeger verliep de overgang tussen de ploegen quasi direct, er was bijna geen overlap. Sinds kort hebben we wekelijks een overlapmoment van een half uur ingepland.
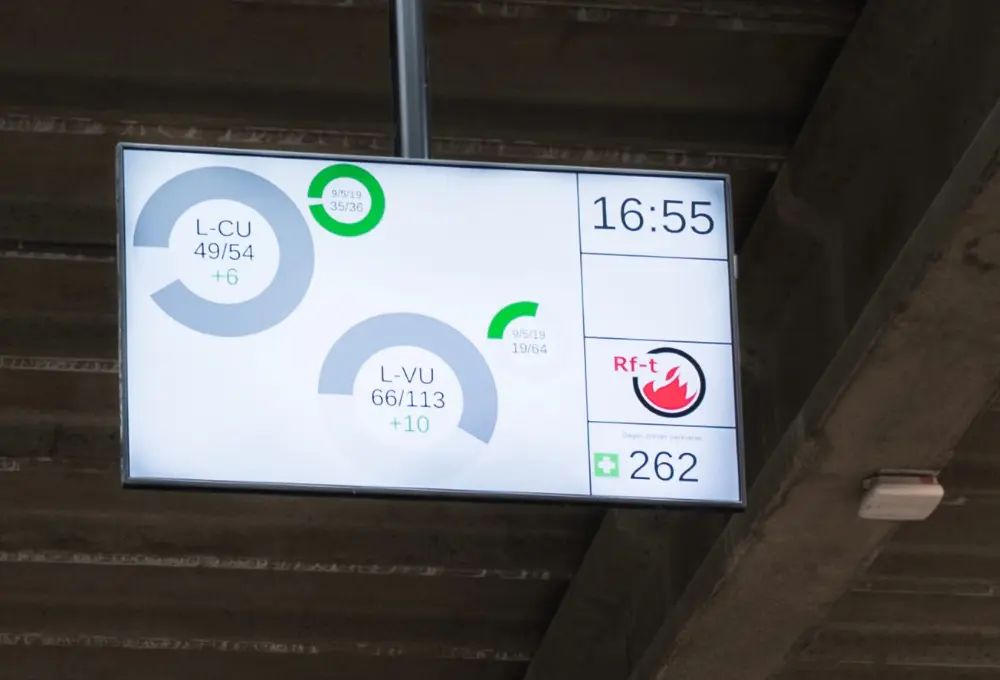
Op strategische plaatsen kwamen er ook infoschermen. Daarop onder meer productiedoelen voor die dag. Zulke info helpt de betrokkenheid van de werknemers te stimuleren. De communicatie verloopt zo veel beter. Ook het teambord is herwerkt, de werknemers mochten zelf de indeling daarvan vastleggen. Klachten van klanten krijgen er een plaats op, de werknemers die in verlof zijn die dag, mankementen aan de machines, planningen … Een derde kleine ingreep zijn de grote schermen die overal in het bedrijf op strategische plaatsen worden opgehangen. Daar staan eenvoudige zaken op: de productiedoelen voor die dag bijvoorbeeld en het huidige cijfer. Zulke info helpt de betrokkenheid van de werknemers te stimuleren. Er is ook een teamcharter opgesteld waarin een aantal commitments worden meegegeven.Wat ik ook nog wil aanstippen, zijn de inspanningen die we hebben gedaan om onze werknemers en onszelf te 'leren communiceren'. Dat lijkt makkelijk en evident, maar is het allerminst. Correct aanbrengen aan je collega's dat ze iets verkeerd doen, dat is niet iedereen gegeven. We hebben samen met Agoria meerdere sessies doorlopen om dat aan te leren. We kunnen stellen dat deze maatregelen een zeer positieve invloed hebben. De communicatiedoorstroom is nu veel beter. Er is een tussenlaag minder, want er is geen teamleider meer. We ondervinden ook dat het team zeer goed samenhangt. Missie geslaagd dus."
SMART PRODUCTION SYSTEMS
Jürgen Van De Velde: “Hier gaat het voornamelijk om efficiëntie. In 2014 hebben we gedurende 8 maanden een aantal zaken opgemeten, soms letterlijk met de chronometer in de hand. Die nulmeting hebben we uitgedrukt in efficiëntiepunten, met 100 als startwaarde. Vervolgens zijn we beginnen kijken naar het laaghangend fruit, de 'non value added time' zoveel mogelijk gereduceerd. Dat resulteert 4 jaar later in een efficiëntiescore van 120, dus 20% beter. Het uiteindelijke doel blijft om ons te wapenen tegen concurrentie. Betrouwbaarheid is zeer belangrijk in onze sector. Als we een levertermijn beloven aan een klant, moeten we die ook waarmaken. Dat is vooral van belang omdat er sinds 2012 een geharmoniseerde CE-normering werd opgesteld. Op zich is dat niet verkeerd, maar het werd zo wel makkelijker voor andere spelers om ook op onze markt te gaan verkopen. Wij hebben daarop gereageerd door in te spelen op kortere levertermijnen. Op dat moment zaten we op 10 dagen. Met kleine stapjes hebben we daar telkens wat tijd afgehaald. In 2015 haalden we 5 dagen. Vandaag kunnen we bepaalde basisproducten op 48 uur leveren. Zo kunnen we bijvoorbeeld in Nederland sneller leveren dan Duitse bedrijven."
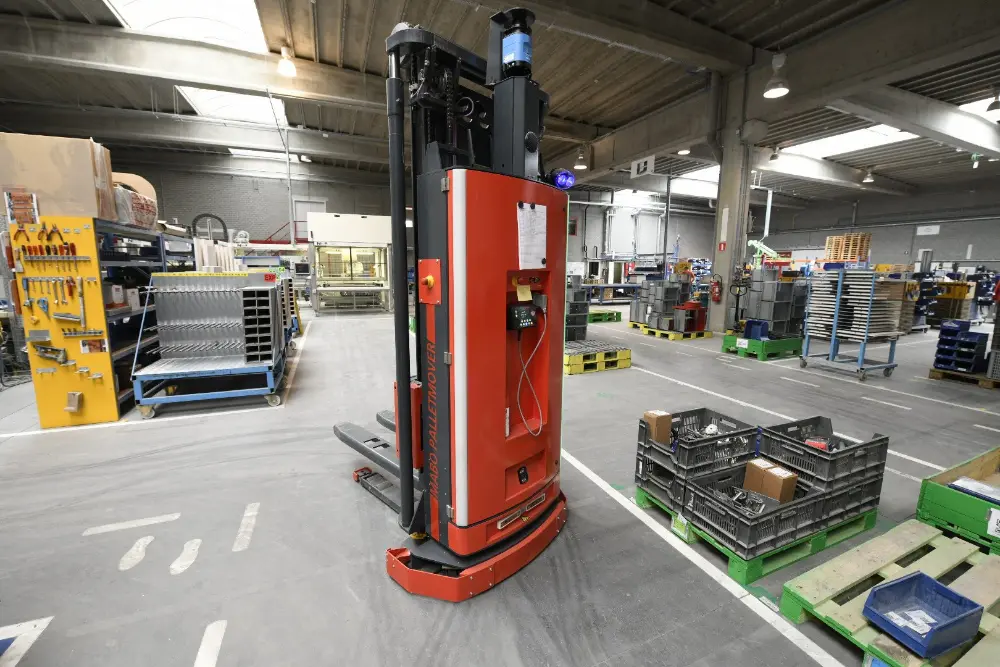
DIGITAL FACTORY
Bart Vergote (IT-manager) vertelt ons meer over de softwaretechnische achtergrond: “We mogen niet vergeten dat de opgesomde innovaties worden aangestuurd door software: het scannen, de visualisatie van de schermen, de Kardextoestellen, de AGV's …
Zo is de scanapplicatie volledig door onszelf ontwikkeld. Vroeger verliepen veel acties rechtstreeks, waarbij werknemers manueel zaken inbrachten en opzochten in het ERP-systeem. We wensten dat te vermijden: we wilden dat de acties gebundeld en asynchroon naar het ERP-systeem gestuurd werden. Zo vermijden we de verliestijd ten gevolge van het wachten op het systeem. Dat vergde wel wat inspanningen, zo moesten we bijvoorbeeld alle flows in kaart brengen. Die applicatie staat zo goed als los van het ERP-systeem. Het communiceert er mee, maar is er niet afhankelijk van. Als we later willen veranderen van software, kan dat makkelijker. Ondertussen zijn ook onder andere de Kardex, het laadsysteem voor de vrachtwagens en de AGV eraan gelinkt. In principe proberen we altijd de software van de fabrikant te behouden, we gaan enkel aanpassingen uitvoeren indien nodig voor onze applicatie. Zo is de Power Pick-software voor de Kardex prima, enkel voor de aanvoer van de data vanuit het ERP-systeem hebben we een kleine applicatie gemaakt om de werking te laten aansluiten op onze werkwijze. Hetzelfde geldt voor de AGV. De software van de fabrikant is prima, maar we wilden deze wat verder toespitsen op onze eigen situatie. Zo willen we dat onze operatoren bepaalde prioriteiten kunnen instellen en zelf palletgroottes kunnen ingeven. Ook hier hebben we onze scansoftware uitgebreid, in dit geval hebben we dat opgelost door het gebruik van QR-codes die alle nodige informatie bevatten." Vergote illustreert dit met een klein voorbeeld: “Als er ergens 15 palletten moesten worden opgehaald, waren er 30 scanacties nodig: 15 keer inscannen om de opdracht te geven, en 15 keer scannen om de opdracht af te melden. Door een QR-code aan te maken met '15 palletten ophalen' als opdracht, beperk je dat tot 2 scanacties. Met een gigantische tijdswinst tot gevolg."
NETWORKED FACTORY
De vijfde transformatie wordt terug toegelicht door Jürgen Van De Velde: "De inbreng van ons netwerk wil ik ook graag even aanstippen. Zo hebben we een vruchtbare samenwerking met Trianval, een maatwerkbedrijf uit Wetteren. Zij kunnen op een zeer flexibele manier werknemers ter beschikking stellen. Dagelijks zijn hier minstens 5 werknemers van hen aan de slag, maar in piekperiodes loopt dat op tot 15. Daarnaast werken we ook nauw samen met de plaatselijke technische school voor stages en eindwerken. We zijn eveneens actief in meerdere normcommissies. Via Agoria staan we ook in contact met alle belanghebbenden rond brandveiligheid, onder andere ook de FOD Binnenlandse Zaken. We zijn vaak ook de afgevaardigde namens België in die normcommissies. Daar bewaken we de normering samen met onze concurrenten, laboratoria en andere entiteiten. Maar ook in plaatselijke organisaties in onder meer Frankrijk en Nederland zijn we actief in forums rond brandveiligheid."
RF-TECHNOLOGIES: PASSIEVE BRANDBEVEILIGING SINDS 1985
Familiebedrijf Rf-Technologies produceert vanuit twee afdelingen - eentje in Oosterzele, eentje in Slovakije - passieve brandbeveiligingsproducten zoals brandwerende kleppen, vlinderkleppen, ontrokingskleppen, controllers, brandwerende ventilatieroosters, brandwerende manchetten, afdichtingsmateriaal en brandwerende platen. In totaal zijn 200 personen dagelijks in de weer om deze onderdelen te produceren conform de internationale normen. Het bedrijf beschikt over eigen testfaciliteiten met twee testovens, waar de producten onderworpen kunnen worden aan dezelfde tests die nodig zijn om de certificering te verkrijgen. Jaarlijks worden ongeveer 100 van die tests uitgevoerd. In februari 2012 werd het bedrijf de eerste leverancier met een volledig gamma van brandkleppen met CE-markering. De producten van Rf-Technologies vinden we ondertussen over de hele wereld terug, onder meer in bekende bouwwerken als het Nato-gebouw in Brussel, La Maison du Radio in Parijs en de Odeon-toren in Monaco. Het bedrijf exporteert naar 25 landen en behoort Europees tot de top drie in deze sector. Bedrijfsleider Bernard Santens - u kent de ondernemersfamilie misschien van het gelijknamige badstoffenbedrijf - is terecht trots op de verwezenlijkingen van zijn team: “Onze bedrijfsslogan is 'Open to innovation, closed to fire'. Dit dekt hier goed de lading, want we mogen toch wel zeggen dat innovatie de rode draad is doorheen het bedrijf, met de Factory of the Future Award als ultieme bekroning."