AGV-technologie: What’s in a name?
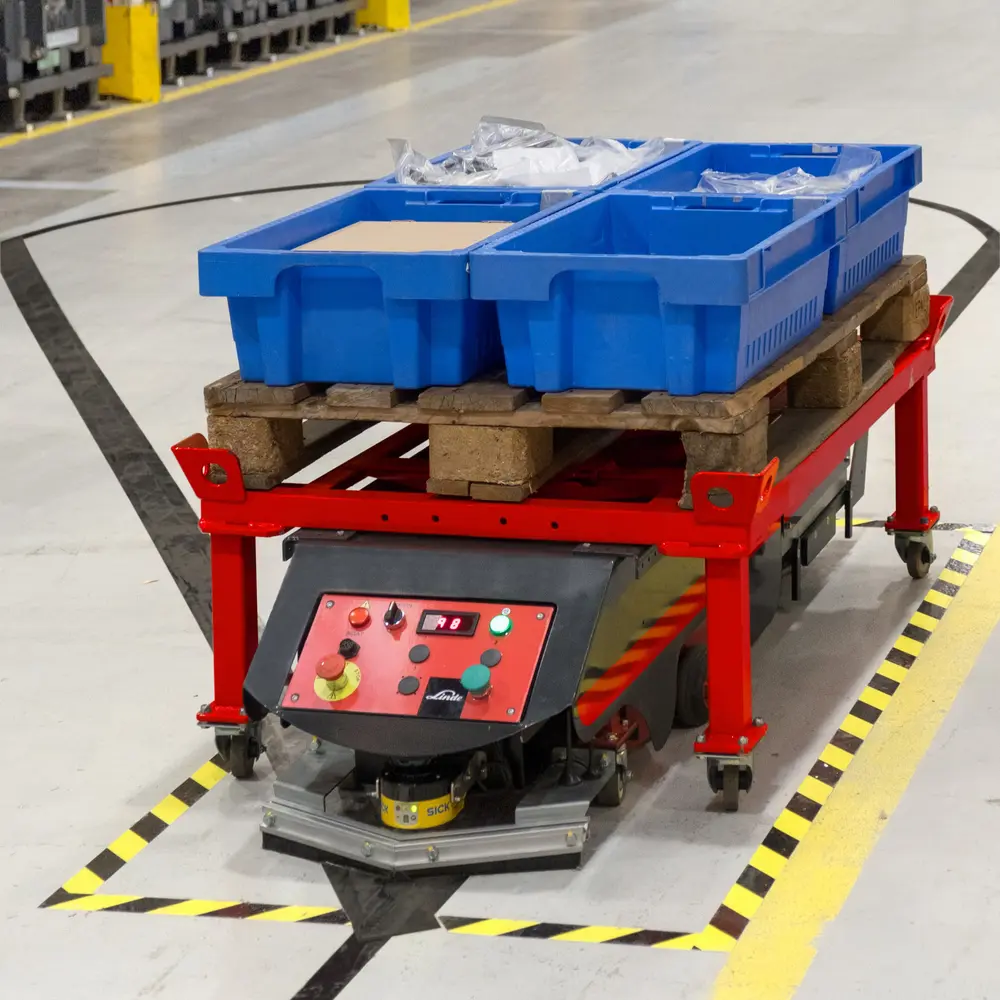
De AGV-technologie is ondertussen een vertrouwde technologie geworden die we steeds vaker zien opduiken in bedrijven. In recente jaren zagen we tegelijkertijd heel wat blitse, soms producentspecifieke afkortingen voorbijkomen, wat het voor gebruikers niet altijd even duidelijk maakt over welke technologie we nu exact spreken: AGV, AMR, SDV, IDV, DTS … We hadden een gesprek met Filiep Vincent van Sirris om klaarheid te scheppen in deze materie.
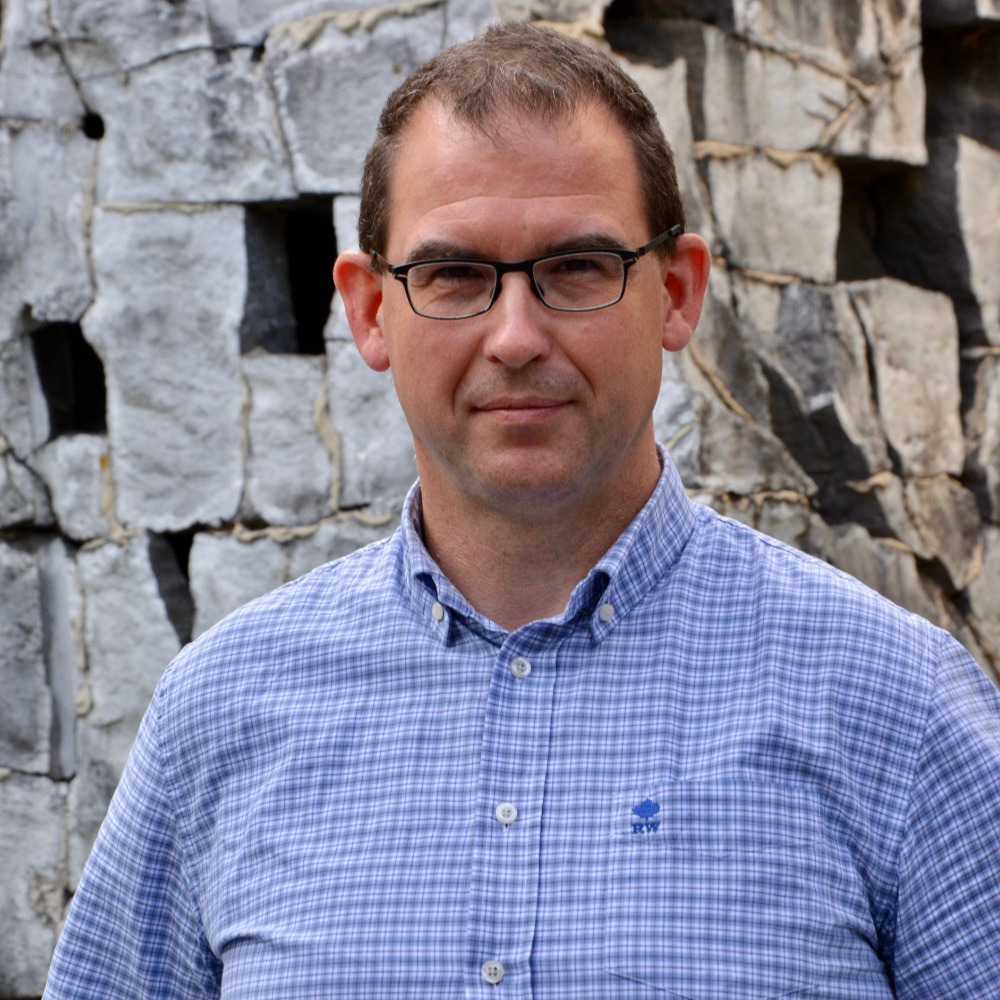
Onderscheid tussen AGV en AMR
“Voor velen is een geautomatiseerde heftruck die palletten vervoert een AGV,” steekt Vincent van wal. “Dit terwijl de karakteristieke kleinere toestellen als AMR’s aangeduid worden. Dat onderscheid is evenwel niet altijd even duidelijk te maken. Wij vinden dat de manier waarop genavigeerd wordt een veel duidelijker onderscheidende factor is. Daar bestaan een aantal werkwijzes in die elk hun merites hebben. Een van de eerste methodes voor AGV’s - al sinds de jaren ‘60 - is via een sleuf in de grond met een koperen kabel, waarbij via het opgewekte magnetische veld het toestel voortbeweegt. Deze methode zien we stilaan verdwijnen. Een andere werkwijze is via (magnetische) tape of tags op de grond of via een kettingbaan in de grond. Vooral de werkwijze met magnetische tape zien we nog wel eens in bedrijven. Deze drie werkwijzes hebben één iets gemeenschappelijk: de geleiding gebeurt op een vast, vooraf uitgestippeld traject. Dat is wat wij als AGV zouden aanduiden.”
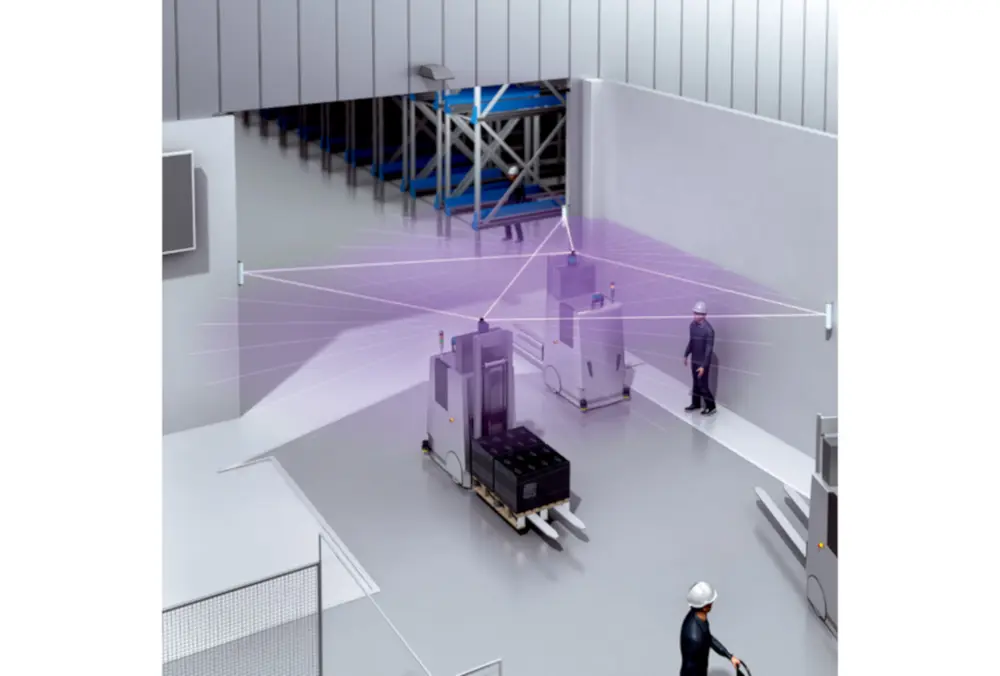
“Bij AMR’s is de wijze van navigatie anders, hier bewegen de toestellen zich op basis van een interne kaart maar ook hier zijn diverse manieren om dit te bereiken."
"AMR's bewegen zich op basis van een interne kaart"
"Een eerste is op basis van vaste referentiepunten: op vaste entiteiten zoals muren, poutrellen of starre rekken in het bedrijf zijn reflectoren aangebracht. Op de AMR staat een LIDAR die voortdurend de omgeving scant om de reflectoren terug te vinden. Als er drie gedetecteerd worden, weet het toestel exact waar het zich bevindt op de kaart die ingelezen werd. Dit is vandaag een zeer populaire toepassing."
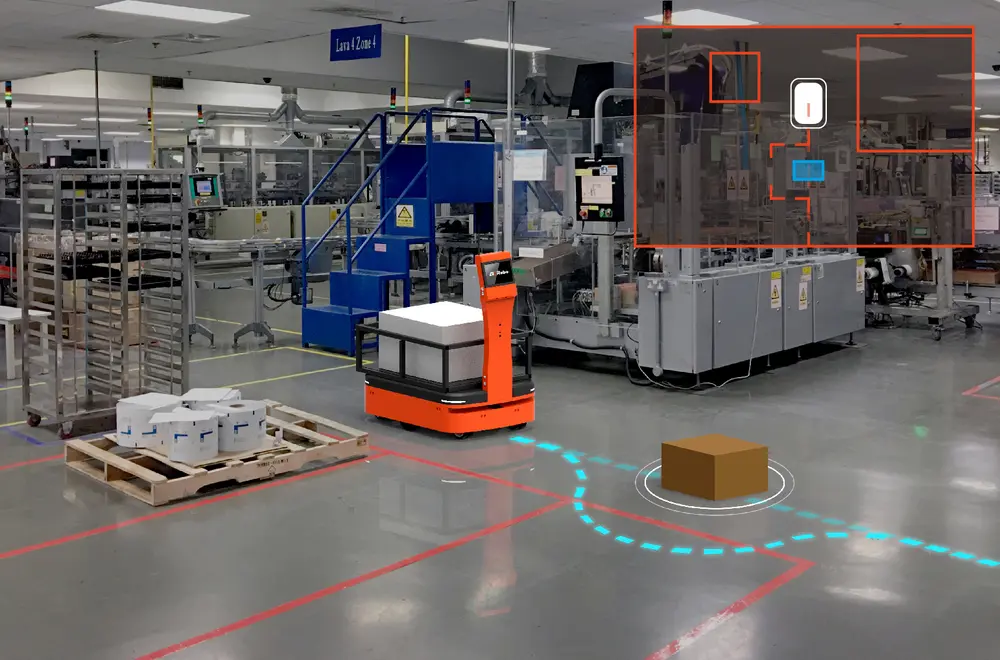
"Een tweede werkwijze - die vandaag aan populariteit wint - is werken met natuurlijke referentiepunten in plaats van reflectoren. Hier wordt gebruikgemaakt van laserscanners die op ongeveer 20 cm hoog geplaatst worden en voortdurend de omgeving aftasten via laser. Door de informatie van de terugkaatsing kan de AMR weten wat er op zijn weg staat. Ook hier is evenwel nog een eerste inlezing nodig, waarbij de AMR aangeleerd wordt wat de grote structuren - muren, rekken, machines … - zijn in zijn actiegebied. Op die manier kan hij zich voortbewegen in deze omgeving, maar kan hij ook plotse obstakels detecteren die niet tot de vaste structuren behoren."
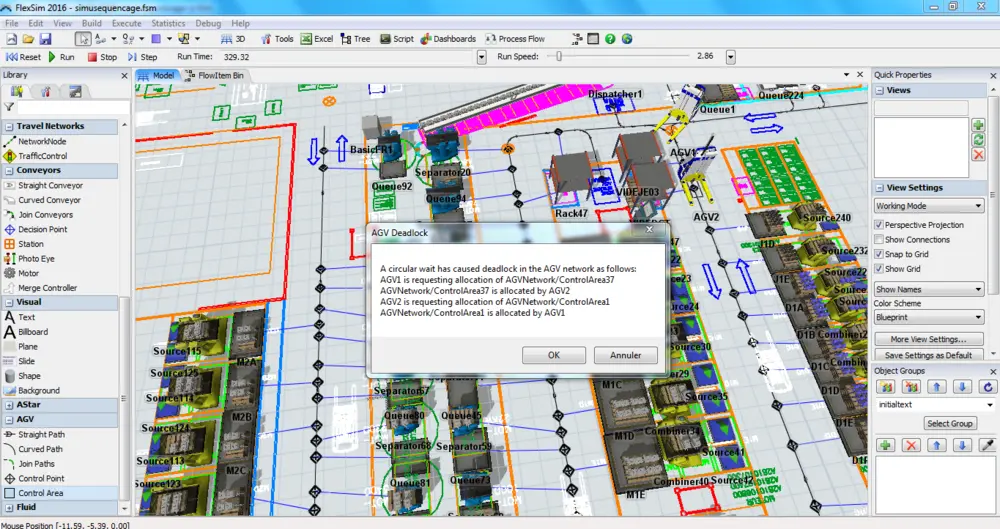
waarbij 2 voertuigen elkaar omwille van de veiligheid tot stilstand brengen
"Vanaf dit punt zijn er terug 2 werkwijzes mogelijk: ofwel wordt gewerkt met veiligheidszones, waarbij de detectie van een object eerst resulteert in een vertraging en indien nodig in het tot stilstand brengen van de AMR. Dat is uiteraard prima om bewegende personen te vermijden, maar als een werknemer een palet op het traject zet, zal de AMR uiteraard compleet stilvallen. Daarnaast is er ook het risico op een zogenaamde deadlock. Stel dat 2 AMR’s met veiligheidscanners elkaar kruisen, dan zullen ze elkaars aanwezigheid detecteren en vertragen tot ze helemaal stilvallen. Dat kan vermeden worden door hun trajecten uit elkaar te houden. Bij AMR’s van eenzelfde merk kan de fleetmanager - zie verder - hier wel rekening mee houden, maar dat is niet altijd het geval bij toestellen van verschillende producenten. In de tweede optie berekent de AMR zelfstandig een andere route om een obstakel te vermijden. Dat vereist uiteraard een zekere rekenkracht.”
Aandrijving en communicatie
“Over de aandrijftechniek kunnen we kort zijn, want die is relatief eenvoudig. Meestal wordt gewerkt met 2 aangedreven wielen en 4 zwenk- of blokwielen (op de hoeken) voor de stabiliteit. Sommige toestellen kunnen een bocht maken, maar niet zijdelings rijden terwijl andere toestellen dat wel kunnen. In sommige gevallen kan dat een voordeel zijn, bijvoorbeeld als de manoeuvreerruimte beperkt is. Een groter aandachtspunt vormt de communicatie. Daar wordt meestal wifi voor ingezet, maar dat is niet altijd even stabiel in een industriële omgeving. Bovendien moet de dekking echt overal 100% zijn, op elke hoogte en in elke hoek van het actiegebied. Zodra de verbinding even wegvalt, valt de AGV onherroepelijk stil en dat zorgt voor verlies aan efficiëntie in de productie.“
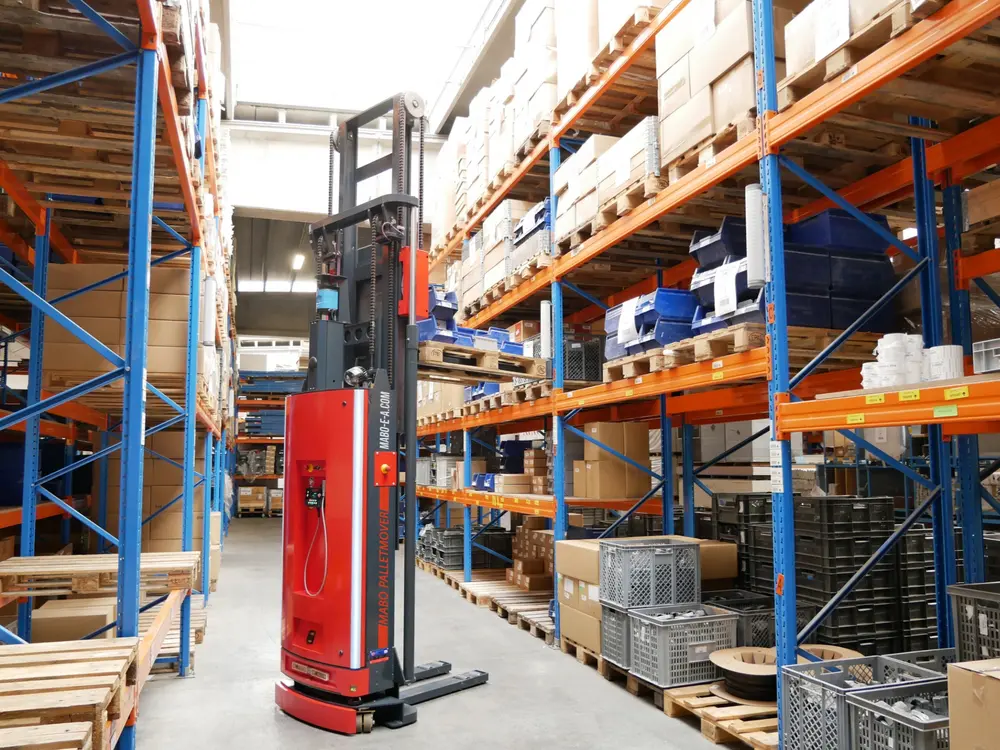
Uitdagingen
“Als uitdaging zou ik de veiligheid - zie kaderstuk verderop - en de integratie van AMR’s in de productieketting noemen. Wij hebben bij Sirris net een interessant proefproject afgewerkt bij het bedrijf Altachem, waarbij AMR’s ingezet werden om onnodige verplaatsingen van operatoren te vermijden. Daarbij werd de combinatie gemaakt met de Karakuri-kaizen systemen. Daaruit kwam een oplossing naar voor met 2 types AMR’s. De eerste verplaatst via een zelf op maat gemaakte pipe-and-jointconstructie met bak componenten in bulk. De AGV kan makkelijk de bak transporteren en via zwaartekracht het product lossen zonder manipulatie van de operator. De andere AMR is bovenaan voorzien van een aangedreven rollenbaan conveyor met daarop een verpakking met product, die zo makkelijk in een ander deel van het proces kunnen ingevoerd worden.”
“Daarnaast stip ik zeker ook de aansturing aan van diverse merken AMR, want zij beschikken over eigen software en userinterfaces om hun map en routes te creëren. Beiden maakten in dit geval gebruik van het SLAM (Simultaneous Localisation And Mapping) principe, waarbij de toestellen zelf hun kaart creëren door rond te rijden in hun nieuwe omgeving. Maar dan blijft de issue om hun onderlinge communicatie af te stemmen. Meestal wordt gebruikgemaakt van een fleetmanager om meerdere toestellen aan te sturen, maar die zijn veelal beperkt tot één fabrikant. Maar wat als u toestellen van meerdere producenten moet aansturen? Wij hebben dat opgelost met software van Flagstone, die met alle systemen kan spreken via Rest-API’s. Dat is een publiek document dat de producent ter beschikking stelt, op basis daarvan kan de software de nodige informatie krijgen over de sturing van de AMR. In die optiek is ook het VDA 5050 initiatief het vermelden waard, want dat beoogt de verdere standaardisering van de communicatie.”
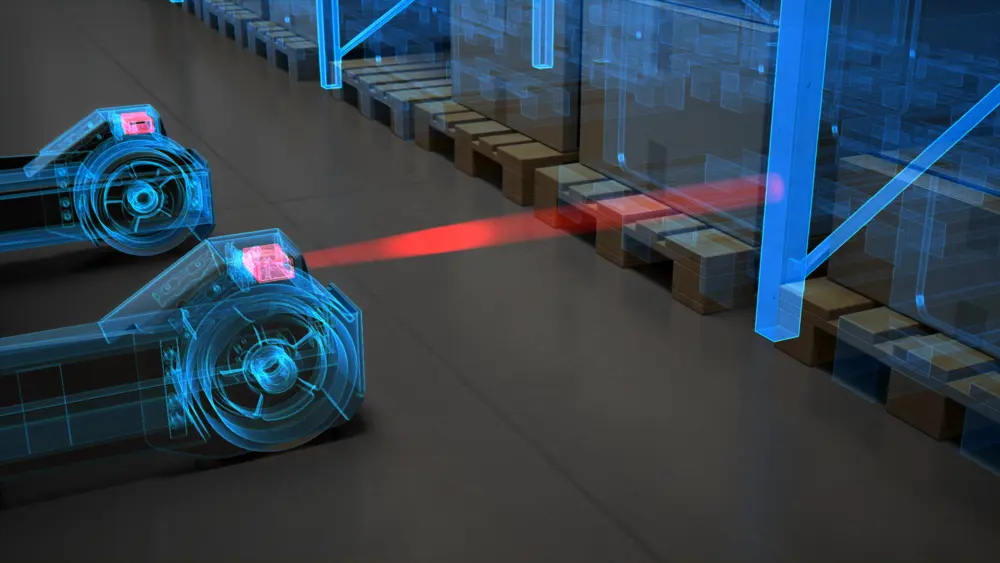
Omgevingscondities vormen risico
“Naast deze uitdagingen stip ik ook nog de specifieke hinderpalen aan in sectoren als de voeding. Het transporteren van goederen uit een diepvrieszone richting een normale omgevingstemperatuur zorgt bijvoorbeeld voor risico op condensvorming, wat niet bevorderlijk is voor de componenten. Ook de aanwezigheid van vocht is niet optimaal, zowel voor de interne componenten als voor het risico op doorslippen. Stoffige omgevingen vormen eveneens een stevige uitdaging, bijvoorbeeld voor de efficiëntie van de laserscanner. Zowel condens en stof kunnen ervoor zorgen dat de scanner verkeerdelijk denkt een obstakel te zien en daarom in stop gaat terwijl het eigenlijk enkel stof of condensdruppel is. Ook de vlakheid van de vloer is heel belangrijk. Bedrijfsvloeren zijn niet altijd even egaal of vertonen oneffenheden, dat is niet bevorderlijk voor de efficiënte werking.”
"Zowel condens als stof kunnen ervoor zorgen dat
de scanner verkeerdelijk denkt een obstakel te zien"
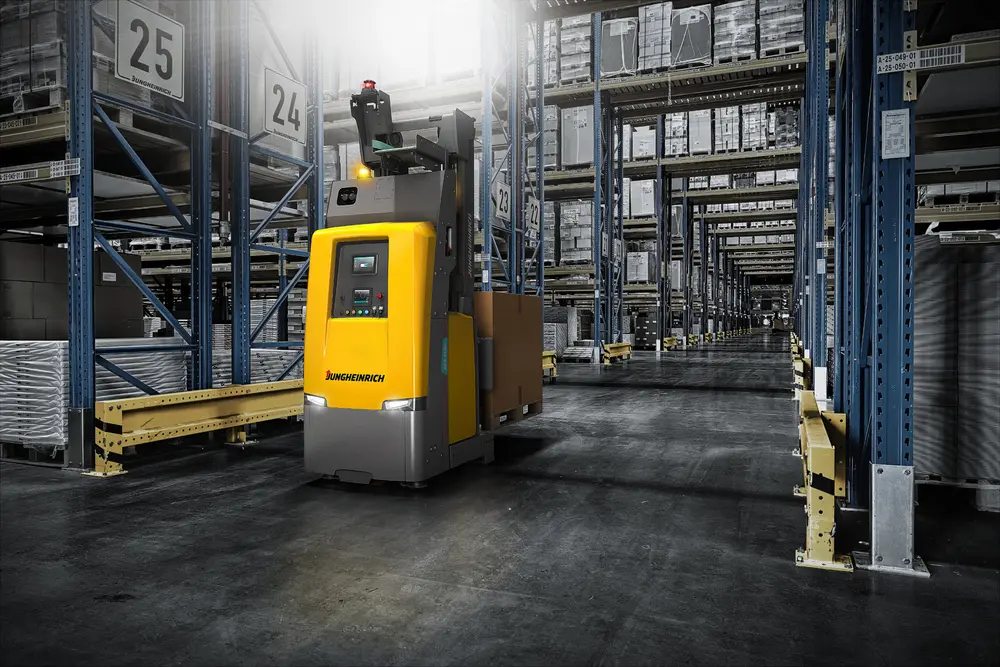
Nauwkeurigheid
AMR’s die naar machines rijden, daar automatisch hun product op de band zetten en hun weg moeten vervolgen richting de nieuwe opdracht. In hoeverre kunnen zij dat vandaag nauwkeurig uitvoeren?
Vincent: “Daar zijn met de huidige technologie nog hulpmiddelen voor nodig. Het hangt wat af van de applicatie, maar soms is een V-marker voldoende. Die helpt de AMR om zich exact te positioneren. Ook de rest van de installatie kan helpen om de nauwkeurigheid te verhogen. Zo kan een robot die de AGV moet ontladen/beladen voorzien worden van een camerasysteem met referentiemarkers. Daarmee vang je de onnauwkeurigheid op van de positionering van de AGV, al verbetert de positie van de AGV op zich niet.
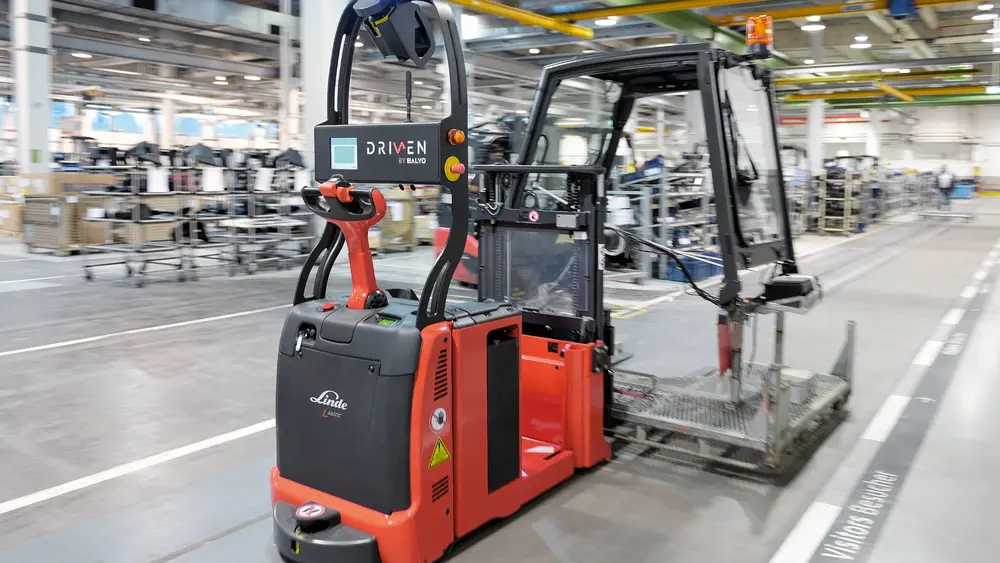
Voorbereiding cruciaal
“We kunnen ook een aantal zaken meegeven waar bedrijven tegenaan lopen. Kijk eerst of de flow van het product wel goed zit, dat is de basis. Een chaotische opbouw automatiseren is meestal nutteloos en lost problemen niet op. Dus starten doe je best met het verminderen van bewegingen, het beperken van transportafstanden en het logisch maken van de productieflow. Vervolgens moet je je de vraag stellen of een AGV wel de beste oplossing is, want soms kan een eenvoudige rollenbaan even goed werken aan een veel goedkopere prijs. Als u voor een AGV opteert, blijven er nog de operationele zaken over. Er zit bijvoorbeeld heel veel verschil in bedienings- en programmeergemak tussen de producenten. Als u voor elk klein akkefietje beroep moet doen op de leverancier omdat u zelf de nodige technische kennis intern niet in huis hebt, zal de prijs sterk oplopen. Verder moet ook de rijweg goed in kaart gebracht worden, denk bijvoorbeeld aan het inschatten van de benodigde ruimte om een bocht te nemen, of het correct instellen van referenties.”
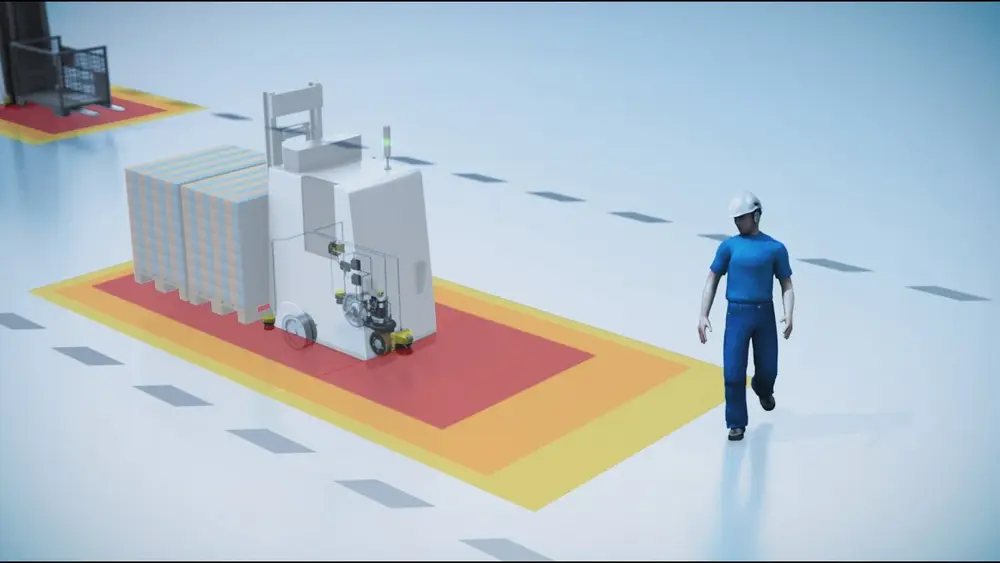
en de validatie van de geautomatiseerde functies van de voertuigen
NIEUWE VEILIGHEIDSNORMEN
De toenemende populariteit van AGV’s is ook de normerende instanties niet ontgaan en dat is een positieve evolutie. Tot voor kort werden AGV’s vooral als een aparte entiteit gezien, maar er zijn wel wat situaties te bedenken waarin dit eigenlijk niet langer houdbaar is. Denk aan een AGV die niet alleen de grondstof of halffabrikaat aanbrengt, maar dit ook op de machine plaatst: dan wordt de AGV in feite een tijdelijk deel van de machine met een bijhorende invloed op de mogelijke risico’s. Omdat de oude norm al dateert uit 1997 (de EN 1525:1997) was het hoog tijd voor een update die de zowel bestuurderloze transportvoertuigen (AGV), autonome mobiele robots (AMR) en bemande transportwerktuigen voor geautomatiseerde functies als onderwerp heeft. Die komt er nu in de vorm van de ISO 3691-4:2020 die kan beschouwd worden als de primaire internationale AGV-norm. De AGV-norm wordt in Europa verder uitgebreid door de invoering van EN 1175: 2020, die betrekking heeft op bepaalde elektrische aspecten en geautomatiseerde functies van AGV en bemande transportwerktuigen. Beide normen wachten wel nog op harmonisatie in overeenstemming met de betreffende Europese richtlijnen.
Concreet bevat de nieuwe norm ISO 3691-4:2020 een uitbreiding van de eisen voor de veiligheidsfuncties voor AGV's en de validatie van de geautomatiseerde functies van de voertuigen. De norm neemt de ontwerpmethodiek van EN ISO 13849 over en schrijft het vereiste Performance Level voor de verschillende voertuigbewakingsfuncties, bedrijfsmodi en de rembesturing voor. Belangrijk is dat de norm niet alleen geldt voor de AGV-fabrikant, maar ook eisen bevat voor de AGV-exploitant. Het hoofddoel is de noodzaak van een goede zone-indeling van de AGV in zijn uiteindelijke installatieomgeving. De zone-indeling moet in overeenstemming zijn met het restrisico van de toepassing.
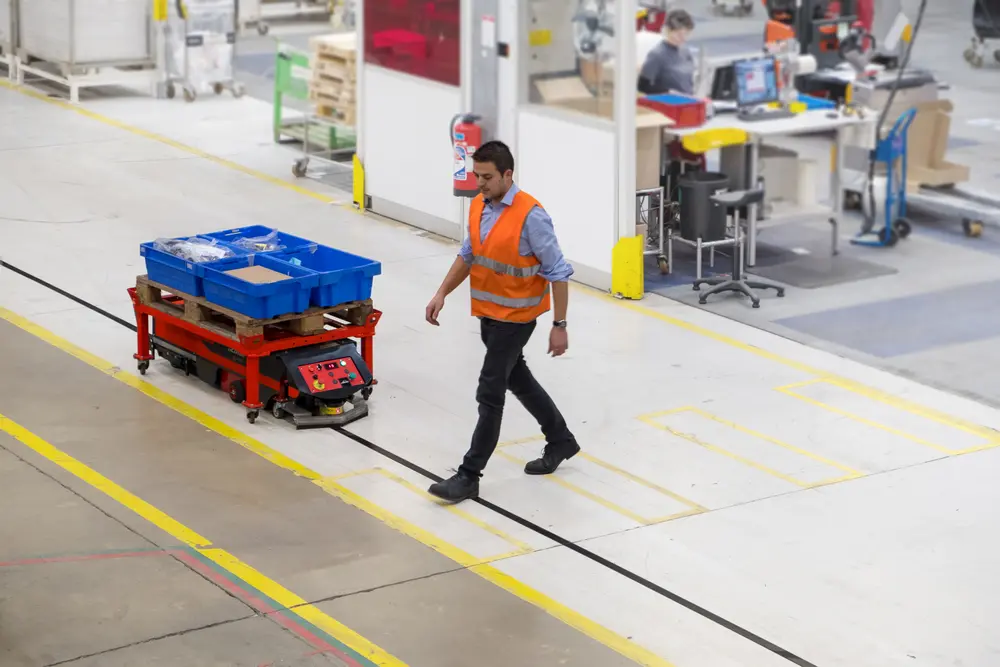