DRUKSENSOREN ONDER DE LOEP
De juiste druk om schadevrij te kunnen verpompen
Drukmetingen maken al tientallen jaren deel uit van productieprocessen. Ook pomptechnologie kan niet om deze grootheid heen. Wie niet aan de juiste druk werkt, loopt het risico zijn pomp te beschadigen of niet voldoende werking te garanderen. Hoe de drukmetingen precies een invulling krijgen, kan op verschillende manieren gebeuren. Dit artikel schetst de voordelen en beperkingen van de voornaamste technologische opties en kadert ze binnen het grotere geheel van Industrie 4.0.
DRUK
Alvorens een overzicht te geven van de verschillende technologieën die ter beschikking staan, is het goed om eerst scherp te hebben wat druk precies inhoudt (zie ook kaderstuk 'soorten druk'). Belangrijk om weten is dat druk steeds ten opzichte van een referentie wordt afgemeten. Positieve en negatieve druk (bovendruk en onderdruk) geven het drukverschil weer ten opzichte van de atmosferische druk (1.013 mbar).
Dat houdt in dat meetapparaten die een dergelijk drukverschil in kaart willen brengen, moeten beschikken over een referentieaansluiting die open is ten opzichte van de atmosfeer. Absolute druk, daarentegen, gebruikt de nuldruk (0 mbar) als referentie. Dat vraagt om hermetisch afgesloten meetinstrumenten. Ten slotte doet men in de industrie aan verschildrukmeting, ook wel differentieelmeting genoemd. Dit geeft het verschil weer tussen twee drukmetingen. Een bepaalde aanwezige druk, de procesdruk, doet dan dienst als referentiepunt.
SOORTEN DRUK
Druk is de grootheid die de kracht meet die wordt uitgedrukt op een oppervlakte-eenheid. Die kan op meerdere manieren uitgedrukt worden: in pascal (PA), newton (N), bar, psi (in Amerika) of in kg/cm³ in (Azië). Druk wordt steeds gemeten ten opzichte van een referentie. Afhankelijk daarvan krijgt die een andere formulering.
- Absolute druk:
een vacuüm is een ruimte zonder materie en daardoor zonder druk. Absolute druk wordt gemeten vanaf 0 bar en is het drukverschil met het absolute vacuüm. De drukmeting gebeurt onder ideale omstandigheden en dus onder vacuümcondities, zodat de referentiedruk gelijk is aan 0; - Atmosferische druk:
Dit is de druk die buiten heerst. De gemiddelde atmosferische druk bedraagt 1.013 mbar. Deze druk is echter niet constant en zal afhangen van enerzijds de weersomstandigheden en anderzijds de hoogte; - Overdruk:
Hieronder verstaat men de relatieve druk die wordt gemeten ten opzichte van de atmosferische druk. Dit is de meest voorkomende meting; - Onderdruk:
Er is sprake van onderdruk als de druk lager ligt dan de atmosferische druk. Dat wordt ook wel negatieve druk genoemd.
DRUKSENSOREN
Het gros van de druksensoren werkt op dezelfde wijze. Ze meten het doorbuigen van een membraan, veroorzaakt door de druk die hierop wordt uitgeoefend. De grootte van de doorbuiging wordt vervolgens omgezet in een elektronisch signaal dat dus de druk weergeeft. Het onderscheid schuilt voornamelijk in de keuze van het membraanmateriaal en in de manier waarop het doorbuigen wordt gemeten. Daaruit volgt een onderscheid in resistieve, capacitieve en piëzo-elektrische drukmeting, elk met hun eigen voor- en nadelen, en binnen een specifiek drukbereik. Het is de toepassing die dicteert welke meettechniek en bijgevolg welke druksensor aan de orde is. Daarnaast heeft de gebruiker keuze in de meetcellen die het hart van de druksensor uitmaken.
MEETCELLEN
Metalen
Metalen meetcellen beschikken over een Hastelloy membraan. Dit drukmembraan wordt via een oliekanaal verbonden met de meetcel. Metalen meetcellen staan te boek als zeer compact en robuust, schok- en trillingsbestendig, en zeer goed bestand tegen piek- en barstdruk. Met hun meetbereik van -1 tot 25 bar en een temperatuurbereik van -12 °C tot 140 °C blinken ze uit in goed thermoshockgedrag. Toepassingen situeren zich in de levensmiddelenindustrie, in corrosieve chemische producten en bitumenopslag.
Dunne film
Deze maakt eveneens gebruik van een stalen membraan waarop een metalen dunne film rust met een Wheatstone brug. Dunnefilmmeetcellen hebben een meetbereik van 25 tot 1.000 bar en een temperatuurbereik van -40 °C tot 105 °C. Ze kunnen erg compact gebouwd worden en realiseren een hoge nauwkeurigheid. Toepassingen situeren zich in de hydraulische techniek en pneumatica, motortestbanken en gascompressoren. Ten opzichte van metalen meetcellen scoren ze vooral beter in precisie. Dat hebben ze vooral te danken aan hun bestendigheid tegen trillingen en andere negatieve invloeden die een correcte meting in de weg kunnen staan.
Keramisch
Hier is de structuur van de rekstrookjes geprint op keramisch materiaal en daarna in een oven gebakken. Het keramische element is bijzonder slijtvast, wat leidt tot een hoge levensduur. Processen waarin agressieve vloeistoffen voorkomen lenen zich dan ook uitstekend als speelterrein voor deze meetcellen. Het meetbereik ligt ong. tussen 0 en 100 bar. Door hun robuustere karakter boeten ze wel wat in aan nauwkeurigheid ten opzichte van dunnefilmmeetcellen.
“Druksensoren meten het doorbuigen van een membraan, veroorzaakt door de druk die hierop wordt uitgeoefend. De grootte van de doorbuiging wordt vervolgens omgezet in een elektronisch signaal dat de druk weergeeft“
WERKINGSPRINCIPES
Resistief
De kern van een resistieve druksensor bestaat uit een behuizing met daarop een membraan van weerstanden. Dit zijn ofwel rekstrookjes, ofwel piëzo-resistieve weerstanden op een siliciumchip. Een rekstrookje is een folie of een film met daarop een elektrische geleider. Wanneer daar een kracht op wordt uitgeoefend, dan wordt de geleider langer en tegelijkertijd ook smaller. Dat geeft als resultaat dat de elektrische weerstand groter wordt. Omgekeerd wordt de weerstand kleiner naarmate de geleider wordt samengedrukt. Door de druk buigt het membraan van de druksensor door en worden de rekstrookjes met daarop de elektrische geleiders uitgerekt of samengedrukt. Hierdoor neemt de elektrische weerstand van de rekstrookjes toe of af, afhankelijk van de grootte van de doorbuiging.
Om de verandering van elektrische weerstand eenvoudig om te zetten in een elektrisch signaal, zijn de elektrische geleiders aangebracht in de vorm van een Wheatstone brug. Met dit principe kan een elektrische weerstandsverandering eenvoudig en nauwkeurig gemeten worden.
“Bij resistieve druksensoren zijn de elektrische geleiders aangebracht in de vorm van een Wheatstone brug, om zo de verandering van elektrische weerstand eenvoudig om te zetten in een elektrisch signaal“
Keramisch-resistief
Bij deze toepassing wordt de vervorming van een keramische meetcel omgezet in een kleinere of een grotere weerstand. Voor toepassingen waarbij bijvoorbeeld piëzoresistieve metingen geen soelaas bieden, kan een keramisch-resistieve drukmeting de oplossing zijn. Ze zijn immers uitstekend bestand tegen corrosie en slijtage.
Keramisch-capacitief
Dit zijn dan weer droge meetcellen die bestaan uit een keramisch membraan, een glasnaad en een keramische plaat. Onder invloed van de druk verandert de afstand tussen de keramische platen. Dat zorgt voor een capaciteitsverhoging die recht evenredig is met de druk. Keramisch-capacitieve meetcellen hebben een drukbereik van -1 tot 72 bar en een temperatuurbereik van -40 tot 150 °C. Ze onderscheiden zich door hun hoge slijtagebestendigheid. Toepassingen situeren zich in de farmaceutische en de papierindustrie en in de afvalwaterbehandelingssector.
Piëzo-elektrische drukmeting
Het werkingsprincipe van piëzo-elektrische drukmeting is gebaseerd op het piëzo-elektrische effect. Dit maakt gebruik van een kristal. Wordt dit kristal blootgesteld aan druk- of trekkracht, dan produceert het een elektrische spanning. De hoeveelheid spanning is evenredig aan de grootte van de kracht. De polariteit van de spanning is dan weer afhankelijk van de richting van de kracht. Dit effect is hoofdzakelijk geschikt voor het meten van dynamische druk. Want hoewel de elektrische isolatieweerstand vrij groot is, lekt de spanning uiteindelijk naar 0.
De snelheid waarmee ze lekt, is afhankelijk van de elektrische isolatieweerstand. Dit betekent dat wanneer er geen verandering in druk is, de uitgangswaarde van de sensor niet accuraat is. Dat maakt hem minder geschikt voor statische drukmetingen. Een piëzo-elektrische druksensor heeft als unieke eigenschap dat hij zeer nauwkeurig kleine drukfluctuaties bij een hoge statische druk kan meten. Dit type krijgt dan ook voornamelijk toepassing bij snelle drukveranderingen.
DRUKSENSOR, -TRANSMITTER OF -SCHAKELAAR
Druksensor
De druksensor is slechts een onderdeel van de drukmeter. Drukmeting start met een drukopnemer, die de procesdruk overzet op de druksensor. Het gegenereerde elektronische signaal komt via een outputmodule ter beschikking van de gebruiker. De druksensor wordt dan geïntegreerd in een transmitter of een schakelaar (transducer). Er bestaan ook samengestelde versies, die beide functionaliteiten combineren.
Druktransmitter
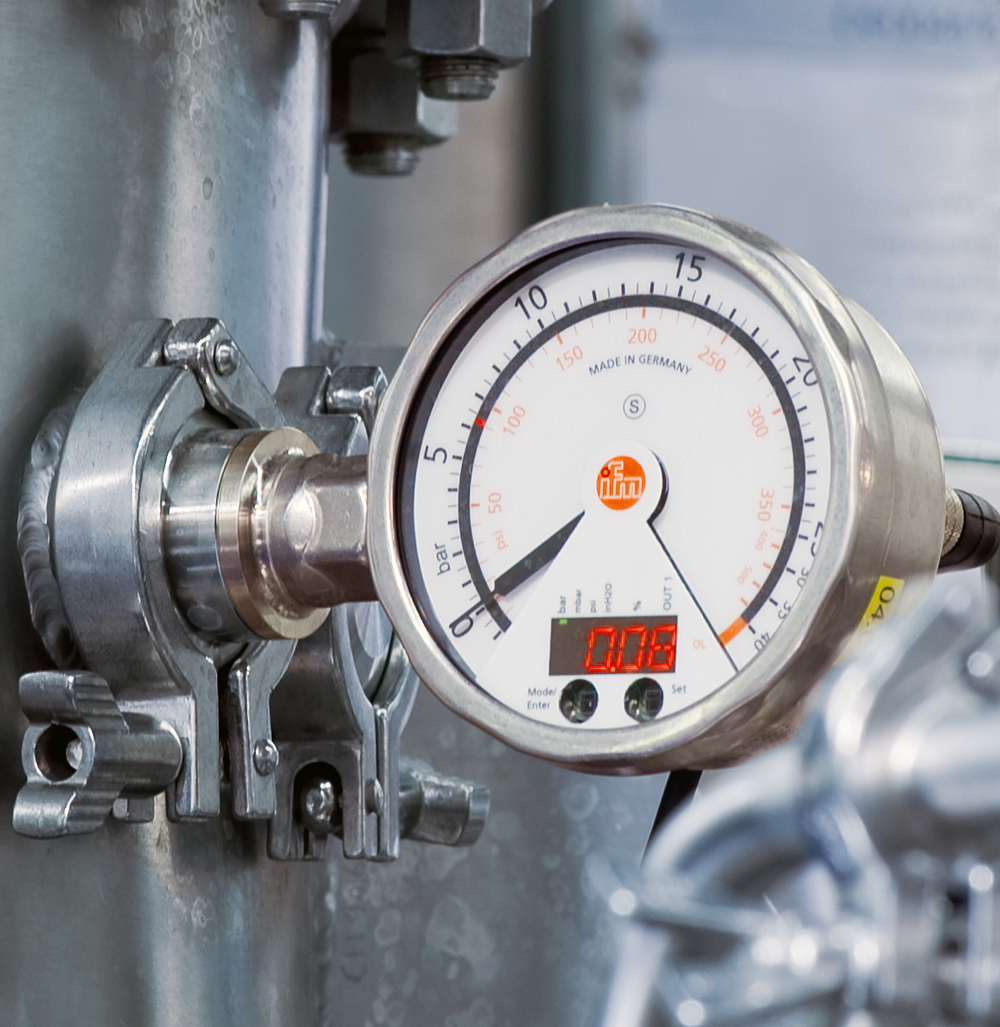
Een druktransmitter wordt gebruikt wanneer de meetomstandigheden van die aard zijn dat ze een negatieve invloed kunnen hebben op de meting, bijvoorbeeld door extreme temperaturen, aanwezige chemicaliën of hygiënische redenen.
Ook media die een deklaag vormen of heel viskeus zijn, kunnen moeilijkheden geven. Dan is er nood aan een druksensor die onder geen beding in contact komt met het procesmedium.
Een transmitter bestaat uit een kamer, gevuld met een geleidbare vloeistof, aan één kant gesloten door een druksensor en aan de andere kant afgesloten van het proces door middel van een membraan. Onder druk buigt het membraan, zodat de kracht wordt overgebracht van de vloeistof naar de druksensor. Dat garandeert een betrouwbare meting.
Drukschakelaar
Een drukschakelaar gaat dan weer een stap verder dan het pure meten en monitoren van druk, zoals een druksensor dat doet. Wanneer een vooraf ingestelde waarde bereikt wordt, zal een drukschakelaar geactiveerd of gedeactiveerd worden. Als de druk te hoog wordt, schakelt de drukschakelaar (dat kan een relais of een transistoruitgang zijn) bijvoorbeeld een ventiel in, waardoor de druk weer afneemt. Drukschakelaars maken veelal gebruik van een 1 … 10 V-sturing: hoe groter de meetwaarde, hoe groter de stuurspanning.
DRUKSENSOREN EN INDUSTRIE 4.0
Sensoren liggen aan de basis van Industrie 4.0. Zij moeten immers de broodnodige data genereren om de productieprocessen te optimaliseren. Deze ontwikkeling heeft ook haar impact gehad op sensoren zelf. Zo zorgden technologische evoluties ervoor dat ze compacter gebouwd kunnen worden. Daarnaast is er de sprong van analoge sensoren naar digitale sensoren, wat de betrouwbaarheid van het signaal ten goede kwam en de nood aan kalibratie verminderde. Maar om echt Industrie 4.0 te zijn, moeten ze ook de verzamelde gegevens tot in de cloud kunnen communiceren. Enkel een display waarop de waarden afgelezen kunnen worden, volstaat dus niet meer. De laatste jaren zien we daarom de trend naar de integratie met IO‑link. Dit maakt het mogelijk om nauwkeurige informatie te verzenden over drukwaarden of installatiecondities uit te lezen.
Deze communicatie loopt overigens langs twee kanten, waardoor de sensoren automatisch kunnen worden geparametreerd of via zelfdiagnose aangeven wanneer ze niet meer naar behoren functioneren en aan vervanging toe zijn. De meeste sensoren in het veld zijn hier nog niet mee uitgerust, maar voor nieuwe aankopen is het vandaag wel de standaard aan het worden.