WATERBOUWKUNDE STELT BEKISTINGSFIRMA’S VOOR SPECIFIEKE UITDAGINGEN
Innovatie vormt oplossing voor uitdagingen waterbouwkundige werken
Bekistingen zijn er in alle maten en gewichten. De techniek heeft intussen haar deugdelijkheid al meer dan bewezen, maar toch gaan ingenieurs allerhande steevast op zoek naar nieuwe technieken en toepassingen. De waterbouwkunde vormt daarbij specifieke uitdagingen, waardoor sommige gangbare oplossingen niet altijd even toepasbaar zijn.
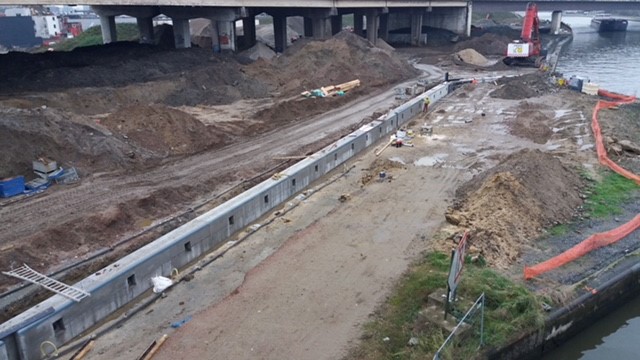
BEKISTINGEN ALGEMEEN
Het principe van bekisting uitleggen hoeft al lang niet meer. Algemeen gesteld, wordt de bekistingswereld onderverdeeld in drie types: traditionele bekisting, systeembekistingen en speciale bekistingen. Een traditionele (hout)bekisting wordt gekenmerkt door een lage materiaalkost, een beperkte repetitie, is zeer arbeidsintensief en wordt gebruikt voor kleinere belastingen.
Systeembekistingen maken dan weer gebruik van een stalen of aluminium frame, kennen een grotere repetitie, worden ingezet voor hogere belastingen en vormen in feite een compleet systeem. En dan zijn er nog de speciale bekistingen die meestal uit maatwerk uit staal of EPS bestaan. Die worden niet zelden voor kolommen gebruikt.
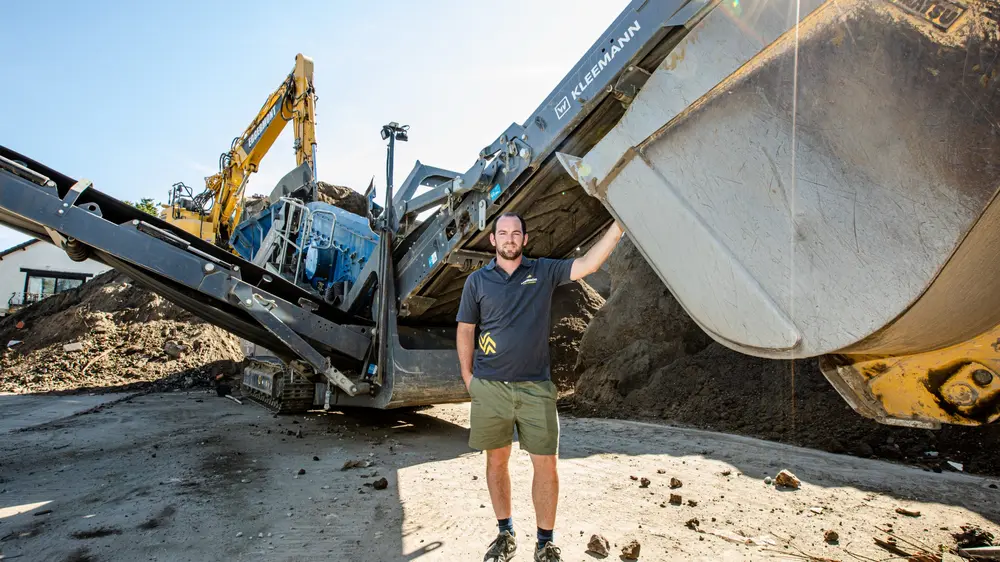
Het uitgangspunt bij tal van werken is veelal de modulaire systeembekisting. Afwijkingen daarvan worden vooral ingegeven door eisen voor het betonoppervlak, de beschikbaarheid van bouwkranen, technische eisen, repetitie, flexibiliteit en zelfs de ervaring van de werfleider.
ALTIJD EN OVERAL
Bekistingen zijn noodzakelijk in alle types van bouwwerken. Wandbekisting, vloerbekisting, klimbekisting, noem maar op. Zo ging de realisatie van de 12 kilometer lange A11, een recente snelweg tussen de N31 in Brugge en de N49 in Westkapelle, gepaard met de bouw van maar liefst 70 nieuwe kunstwerken, waaronder enkele heel speciale. Zo werden de brugdekken van pijler tot pijler gestort met behulp van een stalen vakwerkconstructie en geïntegreerde bekisting, een realisatie van Doka. De bekisting kon verschoven worden op de draagstructuur. Het was de eerste keer dat deze innovatieve, verplaatsbare bekistingstechniek in België werd toegepast.
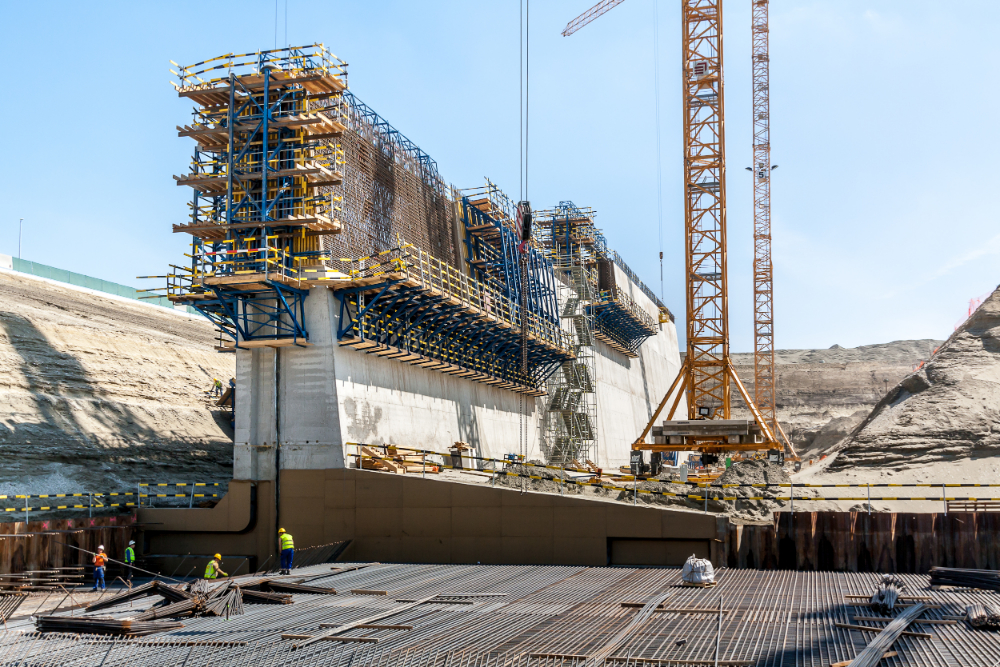
DEURGANCKDOKSLUIS
Waterbouwkundige werken stellen de bekistingsfirma’s niet zelden voor bijkomende uitdagingen. Constructies van havens, bassins, scheepshellingen, kades, sluizen, duikers, steigers, golfbrekers, oeververdedigingen enzovoort hebben elk hun specificiteiten.
Een van de grootste nationale projecten die de voorbije decennia werden uitgevoerd met betrekking tot bekisting bij waterbouwkundige projecten, was de realisatie van de Deurganckdoksluis in de Antwerpse haven. De Deurganckdoksluis is de grootste sluis ter wereld met een lengte van 500 meter, een breedte van 68 meter en een diepte van 28 meter. Voor de THV Waaslandsluis was het dan ook cruciaal om de bekistingspartner zorgvuldig uit te kiezen. Om het project tot een goed einde te kunnen brengen, moest er immers dagelijks zo’n 3.000 meter beton kunnen worden gestort, dankzij performante betrouwbare bekistingsoplossingen. De opdracht werd uiteindelijk toebedeeld aan Doka, dat instond voor de L-vormige sluiskolkmuren en voor de overige onderdelen, waaronder massieve deurkamers, brugkelders, leidingen- en kabelkokers. In totaal werd er voor de hele sluis zo’n 740.000 kubieke meter beton gestort.
L-vormige sluiskolkmuren
De 28 meter hoge sluiskolkmuren dienden te worden gebetonneerd in vijf fasen, waaronder in het bijzonder drie opeenvolgende klimfasen van elk 8 meter hoog. Als algemeen criterium voor de dikke massieve muren (van 5,50 m aan de basis tot 2,50 m aan de top) werd een zelfdragend systeem ontworpen zonder doorgaande trekkers, dit in tegenstelling tot het algemeen gangbare bekistingsontwerp, waarbij de drukken uitgeoefend op de bekisting doorgaans opgevangen worden door doorgaande trekkers die de beide zijden van de bekisting samenhouden. Door het vermijden van doorgaande trekkers vermindert ook het risico op ‘lekken’ in de dokwand. Het zorgde ook voor een snellere uitvoering, omdat er bv. geen steigers moesten blijven staan voor de afwerking.
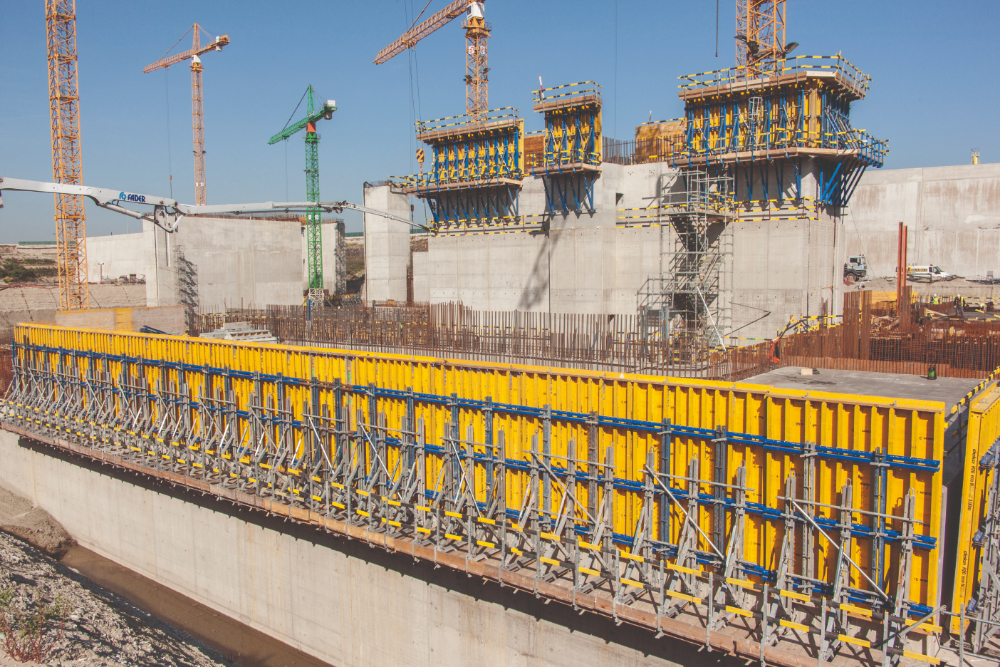
Om dit te kunnen realiseren, werden speciale zelfdragende stalen spanten ontworpen en gefabriceerd, in combinatie met zelfdragende consoles, die naast de ondersteuning van de bekisting en stalen spanten, tevens fungeerden als veilig werkplatform, mede ter bevestiging van de onderste ankerpunten in het al gestorte en verharde beton van de voorgaande fase. Naast de opname van de betondrukken en het gewicht van de bekisting zelf werden deze verankeringspunten ook gedimensioneerd om hoge windkrachten te kunnen opnemen. Bovenaan werd de bekisting samengehouden door een stalen loopbrug, die ook de trekkrachten tot boven het te realiseren betonniveau opnam en overdroeg. Vanaf deze loopbrug kon het betonneren en trillen (verdichten) van het vers gestorte beton in alle veiligheid verlopen.
De massieve deurkamers, brugkelders, leidingen- en kabelkokers
Voor de overige onderdelen werd het bekistingssysteem ontworpen als enkelzijdige wandbekisting, waarbij gebruik werd gemaakt van haar standaard tot 8 meter hoge zelfdragende bokken voor de eerste betonneringsfase aan de basis. De daaropvolgende fases werden telkens over een hoogte van 4 meter gerealiseerd door gebruik te maken van dambekistingsconsoles, die de betondrukken overdroegen naar de ankerpunten onderaan in het al bij de voorgaande fase gestorte en verharde beton. De combinatie van het gebruik van de 8 meter hoge bokken aan de basis, gevolgd door de opeenvolgende klimfases per 4 meter door middel van de dambekistingsconsoles, resulteerde ook hier in het vermijden van doorgaande courante bekistingstrekkers, die in wanden van deze dikte met hoge wapeningsconcentraties zeer arbeidsintensief en moeilijk te realiseren zijn.
De grootste uitdaging bij deze diverse onderdelen, waren – naast de engineering – de grote hoeveelheden aan bokken en dambekistingsconsoles die tegelijkertijd dienden te worden ingezet op het project. Deze hoeveelheden bedragen meer dan een veelvoud van wat binnen de Belgische markt gangbaar is. Het project was dus niet alleen een technisch buitenbeentje, maar het was zeker ook een logistiek-organisatorisch hoogstandje om alle bekistingsonderdelen op dit ene project te mobiliseren en na de goede afloop ervan opnieuw te dispatchen.
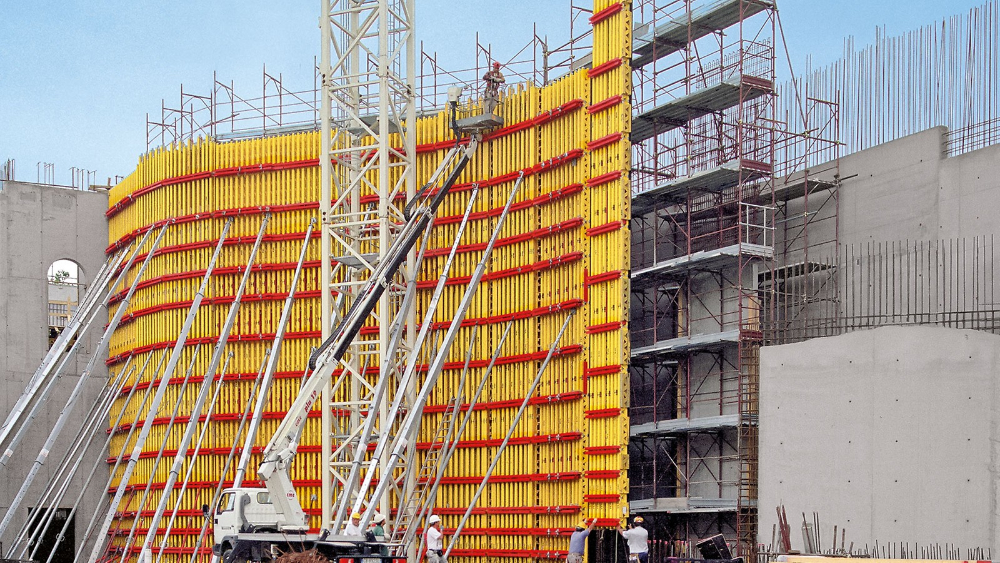
KANAALBRUG OVER DE ELBE
Een ander indrukwekkend project inzake bekistingssystemen is de realisatie van een kanaalbrug over de rivier Elbe in het Duitse Maagdenburg. Een en ander werd uitgevoerd door Peri. Het gaat om de langste kanaalbrug in Europa die de verbinding vormt tussen het kanaal Elbe-Havel en het Mittellandkanaal. De brug, inclusief voorland, is in totaal 690 meter lang en 34 meter breed. Voor de realisatie moesten er zeventien pijlers in de vorm van scheepsboegen geproduceerd worden. Daarvoor werd onder andere de flexibele dragerwandbekisting gebruikt, net als 14 meter hoge elementen in een polygonaal arrangement. Grote FinPly Maxi panelen zorgden voor kwalitatieve betonnen oppervlakken. De bekisting werd speciaal ontworpen om te voldoen aan de projecteisen, wat resulteerde in mooi architectonisch beton.