MODERNISERING DEPALLETISEEREENHEID IN VERPAKKINGSLIJN
Decentrale sturingen: lage installatiekosten, gemakkelijk in onderhoud
Unilin is een belangrijke producent van vloer- en wandelementen en platen voor de meubelindustrie en doe-het-zelfzaken. De Unilin Group investeert constant in productie. Er zijn de grote investeringen, zoals de bouw van een volautomatisch magazijn en van nieuwe productielijnen, maar even belangrijk zijn de permanente upgrades van productie- en verpakkingslijnen, die de productiviteit en dus ook de competitiviteit helpen verhogen.
VERPAKKINGSLIJN GEMELAMINEERDE PLATEN
Een mooi voorbeeld van zo'n upgrade is de ombouw van een depalletiseerunit aan de start van de verpakkingslijn in de productievestiging in Wielsbeke. Daar worden naast gemelamineerde platen ook de gekende Quick-Step vloerelementen geproduceerd. De kerndoelen daarvan: flexibele omschakeling, kortere stilstanden bij panne en hogere uptime. Door het toepassen van een decentraal aandrijfconcept werd het aantal wisselstukken sterk gelimiteerd. Ook werd door de eenvoud in bekabeling de ombouw sneller en goedkoper. En last but not least: wanneer er zich pannes voordoen, dan gebeuren vervangingen plug-and-play.
Flexibilisering van depalletiseermachine
Decoratieve panelen, melamine op dragerplaat, worden vooral in de keuken- en de meubelindustrie toegepast. Omdat klantenservice hoog in het vaandel staat, worden klanten beleverd volgens hun voorkeur. Het gaat dan ook om relatief kleine bestellingen met platen van verschillende afmetingen en diktes. Ook de verpakking is klantgebonden en verschilt per bestelling. Voor de ene klant moet elke plaat een krimpfoliejasje krijgen. Anderen willen de platen per twee, per vijf enzovoort in krimpfolie verpakt zien. Soms moeten er per krimpfoliepak kartonnen beschermhoeken worden geplaatst. Op het einde van de verpakkingslijn moet de ganse bestelling gepalletiseerd en gestrapt worden voor transport.
Werking van de palletonstapelaar
Aan het begin van de verpakkingslijn staat de palletontstapelaar. Met een XY-manipulator worden platen per stuk van de stapel genomen en herstapeld tot het nodige aantal platen dat samen in de krimpfoliemachine moet. De plaat wordt opgenomen via een hefplateau met zuignappen. Om er zeker van te zijn dat er telkens maar één plaat wordt overgezet, wordt de opgenomen plaat horizontaal juist over een schraper bewogen. Mocht er een tweede plaat aan de eerste kleven, dan stoot deze tegende afschraper en valt die terug op de palletstapel. De meegenomen plaat wordt afgelegd op een stangenrooster op hoogte. Als meerdere platen per stapel door de krimpfoliemachine moeten, dan zakt het stangenrooster één plaatdikte en wordt er een tweede plaat opgenomen en op de eerste gelegd. Deze handeling wordt herhaald tot de stapel het aantal platen telt dat samen moet worden verpakt in krimpfolie. Zodra de stapel volledig is, wordt via een Y-beweging van het rooster de stapel neergelegd op een rollenbaan, waarbij de stangen tussen de rollen gepositioneerd zijn. De stapel wordt via de rollenbaan aangeleverd aan de krimpfoliemachine. Het rooster kan terug naar boven, en de volgende stapel kan worden aangemaakt.
Kortere insteltijden door automatische bewegingen
Vermits de verpakkingslijn een breed platengamma met verschillende diktes en groottes moet verwerken, is er per invoerpallet instelwerk: afschuiver op de juiste hoogte instellen, hoogte-instellingen van de bewegingen van de plaatopnemer en van hetaflegrooster volgens de plaatdikte. In het verleden verliep dat manueel. Het ging inde meeste gevallen om een nokkensysteem waarvan de instelhoek met een draaiwieltje nauwkeurig werd gepositioneerd. De XY-bewegingen verliepen met stangenmechanismen, aangestuurd met stappenmotoren. In het kader van een permanente upgrading van de productielijnen wilde Unilin van deze ontstapelaar elke 'variabele' automatiseren, zodat vanuit de bovenliggende PLC de machine automatisch ingesteld kan worden aan de plaat, wat zowel plaatdikte als -grootte betreft. Het idee was dus om elke 'beweging' te automatiseren middels aangestuurde motoren, via encoders, eindeloopschakelaars enzovoort. In deze ontstapelaar gaat het om negen verschillende 'automatische positie'-punten.
Decentrale aandrijving via intelligente modules
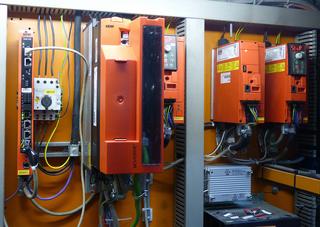
De ontwerpers bij Unilin bereidden zich dan ook voor op het plaatsen van bijkomende elektrische kasten en de aanleg van een complexe bedrading. En ook softwarematig zou het een klus zijn om de motoraansturingen correct te laten verlopen. Omdat al eerder revampings met SEW werden uitgevoerd, werd ook hun idee gevraagd over dit automatiseringsproject. Peter Corrijn, accountmanager bij SEW Eurodrives, kwam echter met een nieuw concept op de proppen, dat de ombouw een stuk zou vereenvoudigen. Hij stelde een systeem voor met één centrale controller, negen DRC's en vanaf de controller één voedings-/netwerkkabel die van motor tot motor wordt doorgelust. DRC's zijn synchroonmotorreductoren met een ingebouwde encoder. Ze omvatten een motor van de IE4-energieklasse (energiezuinige permanentmagneetmotor) en de noodzakelijke aandrijfelektronica in één behuizing. In dezelfde behuizing zitten een aantal I/O's en optioneel een remmotor. Bijkomend voordeel is dat elke DRC standaard een geïntegreerde STO-veiligheidsfunctie (Safe Torque Off) heeft, wat voor onderhoudsinterventies toelaat de elektronica onder spanning te houden en enkel het vermogen uit te schakelen. Dat is belangrijk, want ervaringen uit het verleden leren dat er na het stroomloos zetten van een installatie door een noodstop dikwijls pannes in de elektronica optreden. De DRC-synchroonmotoren kunnen modulair worden aangebouwd op de verschillende SEW-types rechte, vlakke en kegelwielreductiekasten (families R, F en K). Zo kon men zowel de opsteekmotorreductoren voor de manipulator als de riem- en de kettingoverbrengingen voor de plaatpositionering realiseren. Door het brede snelheidsregelbereik (1 op 2.000) kon men zelfs de gehele ontstapelaar uitrusten met één DRC-type, de 0,55 kW (2,6 Nm nominaal koppel). Dat is nuttig voor wat wisselstukken betreft. Enkel voor de XYZ-manipulator (om de zware platen te heffen) werd de 1,5 kW (7,2 Nm nominaal koppel) genomen. In deze module werd eveneens een elektrische remmotor voorzien, nodig voor diens heffuncties.
Geïntegreerde oplossing met DRC's maakt ombouw efficiënter
In een 'normale' installatie had men de motoren in de installatie (elk met vermogensbekabeling) moeten verbinden met een drive in de centrale elektrische kast. In zo'n geval moet men de remmotoren, ook met hun bekabeling en de verschillende absoluutencoders, bekabelen naar de I/O's van de kast, en heeft men dus een ruimere kast nodig. Bij de installatie op basis van DRC's heeft men daarentegen een geïntegreerde oplossing met weinig bekabeling.In de centrale kast was er slechts één SEW-controller voor de instelling en werking van de machine. Die controller krijgt vanuit de machine-PLC de plaatmaten en de stapelgrootte per krimpfoliestapel doorgestuurd. Die is uitgerust met twee S-busmasters. De S-bus zit mee in de kabel met de vermogenskabels, en deze kabel wordt van DRC naar DRC doorgelust. Elke DRC heeft daartoe twee identieke connectoren (één IN en één UIT). Tussen de DRC's komt hetzelfde type kabel met aan elk uiteinde dezelfde connector. Elke kabel bevat dus de energiekabel voor 400 V en een S-bussignaalkabel. Zich vergissen in het aansluiten van de DRC's is niet mogelijk. Elke S-bus kan acht deelnemers aansturen. De eerste S-bus stuurt in dit retrofitproject de behouden machinebewegingen aan. Het gaat om een servodrive (een SEW Movidrive MDX) van de platenaanvoer (een translatiewagen met vacuümzuigers) en ook de drie bestaande rollenbaanmotorreductoren (Movitrans MC07B frequentiesturingen) voor de aanvoer- en afvoerstapels. De tweede S-bus stuurt de nieuwe DRC's aan die instaan voor de automatisering van de machine-instellingen per plaattype. De DRC's zijn de decentrale positioneersturingen voor de diverse positioneerbewegingen (hefraam, verlegrooster, uitrichten, hoogte-instelling). Naast de aandrijving kan de elektronica van de DRC ook de lokale I/O's verwerken, met een I/O-kaartje goed voor vier digitale ingangen en twee vrij te programmeren in- of uitgangen. Dit kaartje is niet gekoppeld per connector, maar inductief aan de interne elektronica. Het probleem van vervuiling van connectoren of vuilpenetratie doorheen de IP65-behuizing stelt zich dus niet. Met deze I/O's werden de eindeloop- en referentieschakelaars aangesloten. Ook van daaruitis dus geen bekabeling meer nodig naar de centrale elektrische kast.
Industry 4.0, economischer in opbouw en gebruik
De DRC is een component binnen het MOVI-GEAR mechatronische SEW-aandrijfsysteem dat volledig past in de Industry 4.0-gedachte: decentralisatie ter vereenvoudiging en plug-and-play bij onderhoud. Het voordeel is zeker de eenvoud in bekabelen (enorm belangrijk omdat het gaat om de ombouw van een bestaande machine). Daarnaast heeft het een makkelijkere softwareopbouw. Er is een gebruiksvriendelijke wizard. Er dient enkel een opstart te gebeuren vanuit de SEW-controller (de DRC-motoren hoeven niet apart te worden opgestart). Bijgevolg dient er bij de uitwisseling van een DRC-stuurkop geen opstart te worden gedaan.
Lagere onderhoudskosten, hogere uptime
Als men de aankoop beschouwt, lijkt het of de DRC-componenten duurder zijn dan de motoren en drives afzonderlijk. Bekijkt men echter de veel lagere bekabelingskosten en het uitsluiten van bekabelingsfouten, dan was dit systeem minder duur dan het 'oude' alternatief. Er hoefde geen elektrische kast te worden toegevoegd en door het 'plug-and-play'-principe werd de doorlooptijd van het project gevoelig ingekort. De snelle motorwissel, de kortere depannagetijden en de snellere opstart na onderhoud leidden tot een lagere onderhoudskost, een hogere uptime en een betere competitiviteit op termijn.