EFFICIENTIE KOELWATERPOMPEN AANZIENLIJK VERBETERD
Dramix vervangt inductiemotoren door synchrone reluctantiemotoren
Dramix, onderdeel van staalfabrikant Bekaert, fabriceert staalvezels voor versterkt beton. Bij dit productieproces is de koeling van de draadtrekmachines een heel belangrijke factor. Via een gesloten circuit wordt er warm water naar een koeltoren afgevoerd, waar het met koelventilatoren tot koud water wordt afgekoeld en via drie koelwaterpompen terug naar de productieafdeling gaat. De asynchrone motoren die deze pompen aandrijven, werden onlangs door KSB vervangen door synchrone reluctantiemotoren. Goed voor een besparing van zo'n 40.000 euro op de jaarlijkse energiefactuur of een terugverdientijd van minder dan een jaar.
BEDRIJFSVOORSTELLING
NV Bekaert Dramix Moen startte in 1979 met de productie van haar Dramix® staalvezels, die als een flexibeler alternatief voor de klassieke staalnetten worden gebruikt in gewapend beton. Nu, bijna veertig jaar later, worden de gebogen vezels in verschillende varianten wereldwijd geëxporteerd.
Productieproces
Bij de productie van deze staalvezels wordt vertrokken van een 5,5 mm dikke walsdraad, gewikkeld op een coil. Die passeert een opeenvolging van trekstenen met een alsmaar kleinere diameter (20% reductie per pas), waardoor de draad steeds fijner en langer wordt. Op het einde van de treklijn is hij nog minder dan een millimeter dik en wordt hij op een rol gewikkeld. In een volgend stadium worden de draden weer afgerold en in een breedte van 36 stuks naast elkaar verlijmd. Vervolgens worden ze op maat geknipt en op verschillende punten gebogen tot de eindproducten, die dan in papieren zakken of in bulkzakken verpakt worden.
Automatisatie
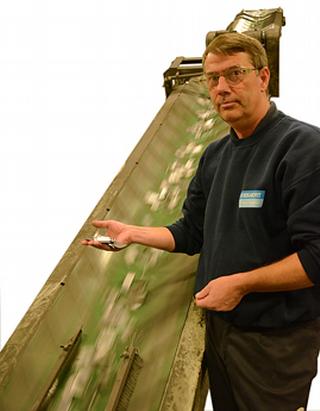
zijn de vitale organen van ons productieproces”
(Philip Vercaemst, onderhouds- en milieuverantwoordelijke bij Dramix)
Energiebesparende maatregelen
“In 2015 zijn we met Bekaert toegetreden tot het EBO, waarmee we ons bij het Vlaams Gewest engageren om onze verplichtingen in het kader van de energiebeleidsovereenkomst na te komen", zegt Philip Vercaemst, onderhouds- en milieuverantwoordelijke bij Dramix.“Concreet betekent dit dat we als bedrijf moeten aantonen dat we energiebewust te werk gaan en dat we willen onderzoeken welke energiebesparende maatregelen we kunnen treffen. Wanneer de investeringen daarvoor binnen de vijf jaar terugbetaald zijn, dan ben je verplicht om ze effectief uit te voeren."In de productieafdeling zelf bleken er geen energetische verbeterstappen te realiseren. In de burelen is er sindsdien wel ledverlichting geplaatst, en de warmte die vrijkomt bij de persluchtcompressoren wordt gerecupereerd om de burelen en kleedruimtes te verwarmen.“Daarnaast waren er ook twee energiebesparende maatregelen mogelijk in ons pomphuis, zoals bleek uit een studie van Laborelec. Zij stelden namelijk vast dat er daar een aantal grootverbruikers zaten", vervolgt Vercaemst.
PROJECT ENERGIE-EFFICIENTIE
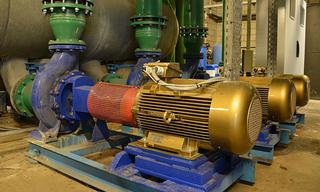
“Vroeger stonden daar drie asynchrone inductiemotoren met een vermogen van elk 37 kW. Die zijn op advies van KSB Service Belgium vervangen door hun nieuwe synchrone reluctantiemotoren, met een vermogen van slechts 22 kW. Die vallen binnen klasse IE4 in plaats van IE2 en zijn dus sowieso efficiënter", weet Vercaemst.“Dat er destijds drie pompen geplaatst zijn en dat we dit zo houden, is louter om betrouwbaarheidsredenen. Mocht er één uitvallen, hebben we nog altijd de andere twee en kunnen we toch blijven produceren", legt hij uit. “De capaciteit is in ieder geval dus een stuk hoger dan de vraag. Vroeger losten we dit op door de afvoer te snoeren met vlinderkleppen, terwijl de motoren wel volcontinu bleven draaien. In energetisch opzicht was dat allerminst een goede werkwijze", beseft de onderhouds- en milieuverantwoordelijke.
Frequentieregelaars
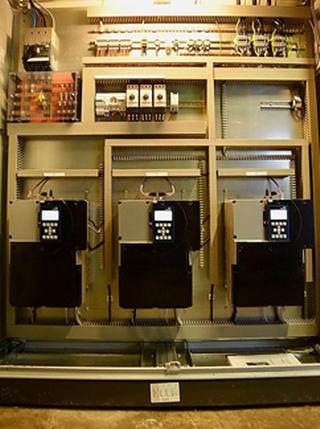
Pompen
“De pompen zelf waren niet aan vervanging toe. Wel kregen ze een totale revisie, wat we altijd overlaten aan KSB Service. Dit onderhoud plannen we elk jaar in, precies omdat die pompen zo belangrijk zijn voor ons. We willen geen onvoorziene storingen", klinkt het.
BEREKENING
Een korte rekensom leert ons dat de jaarlijkse energiebesparing bijna 40.000 euro bedraagt, uitgaande van een kostprijs van 0,054 euro/kWh. Vroeger betaalde men immers 52.507 euro per jaar (3 x 37 kW x 8.760 h x 0,054 euro), nu is dat teruggebracht tot 13.056 euro (3 x 9,2 kW x 8.760 h x 0,054 euro). De kostprijs van het project ligt lager dan die 40.000 euro, waardoor we dus uitkomen op een ROI van minder dan een jaar.
REALISATIE
Dit project werd volledig autonoom gerealiseerd door KSB Service Belgium NV, dat hierbij optrad als hoofdaannemer. Alleen de elektriciteitswerken, de bouw van de elektrische kast met de frequentieregelaars en de civiele werken werden onder hun supervisie uitgevoerd door lokale ondernemingen.“De grootste uitdaging hierbij was het timeframe. De hele klus moest geklaard zijn in onze zomerstop, die welgeteld twee weken duurt. De timing is perfect gerespecteerd; de oplevering en de indienstneming vonden plaats op het afgesproken tijdstip", vertelt Vercaemst.
EVALUATIE
“We hadden al een jarenlange samenwerking met KSB voor de jaarlijkse revisie van onze pompen. Het lag dus voor de hand dat we voor dit project bij hen aanklopten, ook al omdat zij zelf pompen fabriceren. Gezien het respecteren van de timing, het verhogen van de levensduur en betrouwbaarheid van de installatie, en natuurlijk de grote energiewinst, kunnen we zeker spreken van een succesproject. Het enige jammere is dat we deze upgrade niet eerder hebben laten uitvoeren, want dan hadden we al eerder van de winst kunnen profiteren", besluit hij.
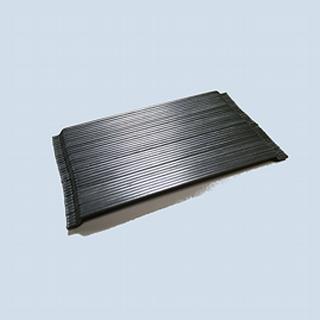