EFFICACITE AMELIOREE DES POMPES DE CIRCULATION D'EAU DE REFROIDISSEMENT
Dramix remplace les moteurs a induction par des moteurs a reluctance synchrone
Dramix, qui fait partie de Bekaert, fabrique des fibres d'acier pour béton renforcé. Dans ce processus, le refroidissement des machines de tréfilage est très important. Via un circuit fermé, l'eau chaude est évacuée vers une tour de refroidissement qui la refroidit en eau froide par des ventilateurs, puis retourne vers le département de production via trois pompes de circulation d'eau de refroidissement. KSB a récemment remplacé les moteurs asynchrones de ces pompes par des moteurs à réluctance synchrone. Une économie d'énergie annuelle de quelque 40.000 euros ou un temps de récupération de moins d'un an.
PRESENTATION DE L'ENTREPRISE
La SA Bekaert Dramix Moen a débuté en 1979 par la production de ses fibres d'acier Dramix®, utilisées comme alternative plus flexible aux réseaux d'acier classiques dans le béton armé. Maintenant, près de quarante ans plus tard, les fibres courbées sont exportées dans plusieurs variantes dans le monde.
Processus de production
Lors de la production de ces fibres d'acier, on part d'un fil laminé de 5,5 mm d'épaisseur, bobiné sur un coil. Celui-ci passe une succession de barres d'étirage d'un diamètre sans cesse plus petit (20% de réduction par passe), ce qui affine et allonge constamment le fil. Au bout de la ligne d'étirage, son épaisseur est inférieure à un millimètre et il est bobiné sur un rouleau. Dans un stade suivant, les fils sont déroulés et encollés côte à côte dans une largeur de 36 pièces. Ensuite, ils sont cisaillés sur mesure et cintrés sur différents points en produits finis, qui sont emballés dans des sacs en papier ou dans des sacs en vrac.
Automatisation
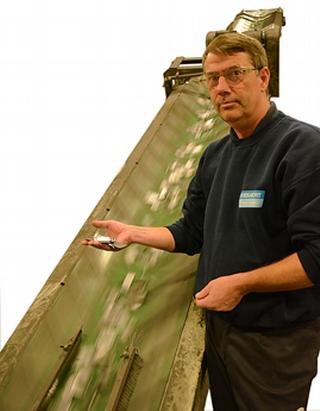
de notre processus de production"
(Philip Vercaemst, responsable maintenance et environnement Dramix)
A l'exception des arrêts de maintenance, les machines tournent ici 24h/24 et 7/7. Le processus est largement automatisé. Le travail manuel intervient à peine.RefroidirOutre cette automatisation, le refroidissement des barres d'étirage et treuils est primordial. Ceci se fait par l'aspersion constante d'eau de refroidissement, venant de la tour de refroidissement juste à côté du département de production. De plus, on insère des grains de savon dans les chambres des différentes passes, pour minimiser la résistance et donc le dégagement de chaleur dans l'étirage. Si ceci ne se produisait pas, cela conduirait à une usure plus rapide des noyaux des barres et les spécifications des produits finis sortiraient des limites de tolérance imposées.
Economie d'énergie
“En 2015, nous avons rejoint avec Bekaert l'EBO, par lequel nous nous engageons auprès de la Région flamande à respecter nos obligations dans le cadre du contrat de politique énergétique", déclare Philip Vercaemst, responsable maintenance et environnement chez Dramix.“Concrètement, ceci signifie que notre entreprise doit montrer qu'elle agit dans le respect de l'énergie et veut étudier les mesures d'économie d'énergie possibles. Lorsque les investissements à ce propos sont récupérés dans les cinq ans, vous êtes contraint de les exécuter effectivement."Dans le département de production, aucune étape d'amélioration n'est apparue réalisable. Depuis, on a bel et bien placé un éclairage LED dans les bureaux et la chaleur libérée près des compresseurs à air comprimé est récupérée pour chauffer les bureaux et les vestiaires. “Par ailleurs, deux mesures à économie d'énergie étaient possibles dans notre corps de pompe, comme l'a révélé une étude de Laborelec. En effet, ils ont constaté qu'il y avait là de grands consommateurs", poursuit Vercaemst.
PROJET D'EFFICACITE ENERGETIQUE
Moteurs
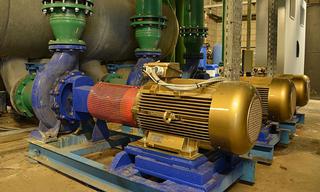
Régulateurs de fréquence
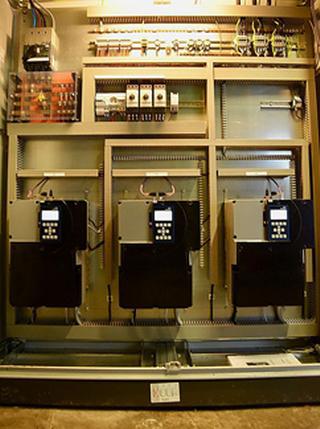
Pompes
“Les pompes ne devaient pas être remplacées. Elles ont été révisées, ce que nous confions à KSB Service. Nous planifions cet entretien chaque année, parce que les pompes sont si importantes pour nous. Nous ne voulons pas de perturbations imprévues", dit-on.
CALCUL
Une courte addition nous apprend que l'économie d'énergie annuelle s'élève à près de 40.000 euros, en partant d'un coût de 0,054 euro/kWh. Avant, on payait, en effet, 52.507 euros par an (3 x 37 kW x 8.760 h x 0,054 euro), maintenant, ceci est ramené à 13.056 euros (3 x 9,2 kW x 8.760 h x 0,054 euro). Le coût du projet est inférieur à ces 40.000 euros, ce qui nous amène à un ROI de moins d'un an.
REALISATION
Ce projet a été réalisé entièrement autonome par KSB Service Belgium SA, comme entrepreneur principal. Seuls les travaux d'électricité, la construction de l'armoire électrique avec les régulateurs de fréquence et les travaux civils ont été exécutés sous leur supervision par des entreprises locales.“Le défi majeur est le timing. Tout le travail devait être achevé dans notre arrêt estival, qui dure deux semaines au total. Le timing a été parfaitement respecté; la réception et la mise en service se sont déroulées au moment convenu", raconte Vercaemst.
EVALUATION
“Nous avions déjà une longue collaboration avec KSB pour la révision annuelle de nos pompes. Par conséquent, il était évident de les approcher pour ce projet, aussi parce qu'ils fabriquent des pompes. Etant donné le respect du timing, l'augmentation de la durée de vie et la fiabilité de l'installation, et naturellement, le grand gain énergétique, nous pouvons certainement parler d'un projet réussi. Il est seulement dommage que nous n'ayons pas procédé à cette modernisation plus tôt, car nous aurions pu profiter plus tôt du bénéfice", conclut-il.
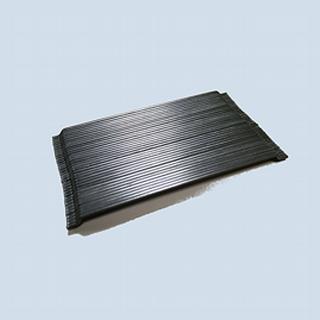