NOUVELLE GENERATION DE MACHINES D'EMBALLAGE FAÇON INDUSTRY 4.0
Scaldopack a conçu des machines de plus de quarante servo-entrainements
La firme Scaldopack à Marke a présenté avec l'OCTO-1 une nouvelle génération de machines pour la production d'emballages droits et flexibles. Plus de quarante servo-entraînements à la technologie avancée garantissent des performances élevées et une grande fiabilité. La numérisation continue traduit bien les possibilités pratiques de l'Industry 4.0.
EMBALLAGES POUCHES
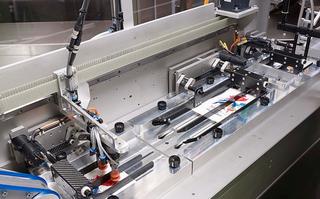
La production de ce type d'emballage est toutefoisun peu plus complexe. Lorsque Harald Saelens, chef de l'entreprise Scaldopack, a décidé il y a quelques années de trouver un constructeur de machines pour la fabrication de ce type d'emballage, il a vite été confronté aux limites des entraînements mécaniques et pneumatiques utilisés dans le secteur.
“Dans le secteur alimentaire, les erreurs de production ont eu de plus en plus d'impact ces dernières années", explique Harald Saelens. “Les rappels impliquent non seulement des frais importants, mais peuvent également porter un coup dur à l'image de marque.
Le but est donc de développer une machine la plus précise et fiable possible mais ce ne semblait pas réalisable avec les entraînements classiques."
Scaldopack a fini par trouver chez Beckhoff Automation un partenaire qui a accepté de s'engager à développer conjointement une nouvelle génération de machines pour la fabrication de pouches. Trois ans plus tard, la première machine est presque prête à être livrée au client. Scaldopack a laissé les emballages de côté et est à présent une entreprisese focalisant sur la construction de machines spécialisées. Spécialisation: la numérisation façon Industry 4.0.
PARTENARIAT AVEC LES CLIENTS
Pour expliquer le concept de numérisation: il faut savoir que pour chaque emballage produit par la machine, pas moins de 4.000 données de mesure sont enregistrées dans une base de données. Les réglages de la machine sont aussi stockés dans une base de données consultée avant le lancement de chaque cycle de production. La machine est donc presque capable d'un réglage automatique.
Comme il cadre parfaitement avec l'Industry 4.0, le concept va encore plus loin, puisque la numérisation permet un nouveau modèle de collaboration entre le constructeur de machines et ses clients.
“Nous pouvons analyser les données de nos clients et proposer des optimisations sur la base de ces analyses", explique Harald Saelens. “Les nouveaux paramètres sont entrés dans la base de données et sont automatiquement repris par la machine sans que le client n'intervienne ou ne doive interrompre sa production. Même pour des nouveaux produits, nous pouvons préparer les procédés chez nous et les tester, de sorte que la machine puisse directement être fonctionnelle avec les nouveaux réglages optimisés chez le client. Nous ne voulons pas livrer une machine, mais être un véritable partenaire quiva aider nos clients à produire des produits de qualité."
Beckhoff a joué un rôle essentiel pour rendre ce projet possible", déclare Wouter Malfait, responsable commercial chez Scaldopack. “Ils ont fourni les composants, mais nous ont aussi aidés à mettre nos idées en pratique."
Scaldopack voulait spécifiquement des performances définies en grande partie par la programmation de la machine. Kimjan Logie, responsable de la programmation, avait déjà travaillé avec des appareils Beckhoff et est en bons termes avec l'équipe de suivi du fournisseur.
“En Belgique, 6 des 18 travailleurs de Beckhoff sont dans l'équipe de suivi. Nous sommes ouverts aux questions des clients et nous faisons tout pour les impliquer dans la réalisation de leurs projets. La programmation de cette machine a été en partie spécialement développée pour eux par nos soins", explique Ronny Noynaert, ingénieur commercial chez Beckhoff.
“C'est ce type de collaboration que nous voulons pouvoir offrir à nos clients", ajoute Wouter Malfait.
CONTROLE DE CHAQUE ETAPE DE LA PRODUCTION
La nouvelle machine OCTO doit son nom à sa forme. Les huit côtés se chargent chacun d'une étape de la production des pouches. La machine est modulable pour permettre plus tard d'adapter certaines étapes de façon rapide et efficace en fon
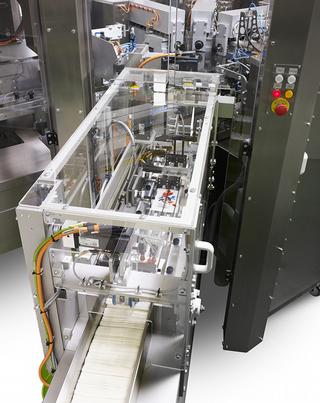
Le point de départ de la production des pouches,ce sont des sacs en plastique scellés sur trois côtés par le fournisseur. L'OCTO-1 doit saisir ce sac, l'ouvrir et le sceller sur un bec verseur. Pour y arriver avec précision, la machine utilise pas moins de 43 servo-entraînements. C'est pour cette technologie d'entraînement que Scaldopack a fait appel à Beckhoff Automation.
Harald Saelens: “Les entraînement nous permettent de contrôler chaque mouvement avec une grande précision, mais surtout: ils nous communiquent un feed-back sur ce qui se passe dans la machine. Chaque étape est donc contrôlée et commandée avec énormément de précision. Lors de l'ouverture d'un sac,la position exacte est mesurée par des cellules photosensibles. Lorsque le bec est en place et scellé, la position est adaptée à la position du sac pour la garantie d'une soudure parfaite. Ainsi à chaque étape, une série de paramètres sont mesurés pour toujours contrôler la qualité, ou lancer les étapes suivantes."
Le système de soudage est l'application la plus avancée de ce principe. Les entraînements qui commandent les procédés sont équipés d'encodeurs externes extrêmement précis d'une résolution jusqu'à quelques dizaines de micromètres.
“Grâce à cette précision, le moindre décalage dans la production est détecté", continue Harald Saelens. “Si le film est doublé, ou s'il manque de la matière,la machine le remarque directement et le produit est écarté."
OPTIMISER LES PROCEDES POUR PLUS DE VITESSE ET DE QUALITE
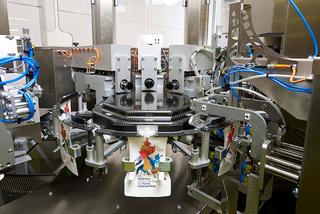
Harald Saelens: “La plupart des données viennentdu scellage. Toutes les positions sont mesurées toutes les deux millisecondes pour que le profil complet du procédé de soudage soit parfaitement visible. Ces informations sont déterminantes pour l'optimisation du soudage.
Du scellage dépendent la vitesse de la machine et évidemment la qualité de l'emballage. Pour cette raison, nous voulons pouvoir contrôler et suivre l'ensemble de ce procédé."
Le cœur de la machine, c'est le PC industriel C6925 de Beckhoff Automation. La partie en temps réel du contrôleur génère le cycle de deux millisecondes utilisé notamment pour l'enregistrement des données. Le réseau EtherCAT qui permet la communication entre les différents composants gère également le contrôle des mouvements. Un cycle de 250 microsecondes pour la synchronisation de certains axes y est généré.
GARANTIE DE QUALITE
Le PC industriel de cette application tourne sous Windows 7 avec la plate-forme TwinCAT2.L'environnement PC du C6925 regroupe les immenses quantités de données que la machine génère en fichiers CVS. Elles sont ensuite transmisesà un second PC qui fait office de serveur données. C'est également dans ce serveur que la machine peut retrouver les paramètres pour des réglages spécifiques.
A terme, l'objectif est de passer sous TwinCAT3, pour pouvoir utiliser les PC multicore de la gamme de Beckhoff. Le serveur de données séparé n'aura alors plus de raison d'être, puisque les données des produits pourront éventuellement être sauvegardées sur le cloud pour être analysées.
Pour ce faire, il faut pouvoir utiliser les outils IoT de l'environnement TwinCAT3. Il comprend les outils IoT Communication et IoT Analytics. Grâce à cette méthode de travail, on peut sensiblement réduire le coût et les pertes de production, et optimiser la qualité.Ce concept 'smart machine' consiste à soutenir l'optimisation des cycles de production et celle de la consommation d'énergie.
Les paramètres de la machine doivent être conservés localement, pour que sa disponibilité ne dépende pas de la connexion à Internet. Ces paramètres peuvent être sauvegardés dans le contrôleur, surtout dans un environnement multicore qui permet d'équiper le PC de nombreuses fonctionnalités sans impacter la partie en temps réel du contrôleur. Cette fonction couvre aussi le serveur Web qui permet d'accéder à la base de données de la machine.
La conception totale d'OCTO-1 est orientée performance, fiabilité et service. Grâce à la numérisation, Scaldopack peut garantir une réaction très rapide aux demandes spécifiques de ses clients. Il aura fallu un an pour l'engineering et la construction de la première machine, mais le concept va permettre de mettre au point très rapidement chaque nouvelle machine. L'entraînement électrique garantit par ailleurs une performance très élevée.
“L'output de notre machine est nettement supérieur à celui d'une machine pneumatique", explique Harald Saelens. “Nous produisons 120 sachets par minute alors qu'une solution classique en sortirait seulement 40 à 60. L'investissement dans ces entraînements avancés est donc rapidement amorti. De plus, la machine demande beaucoup moins d'entretien, ce qui réduit encore le coût d'exploitation. Le plus gros avantage, c'est la fiabilité qui permet à nos clients, fournisseurs pour l'industrie alimentaire, d'être certains de la qualité de leurs produits."