SYSTEME DE DISTRIBUTION ELECTRIQUE POUR L'ASSEMBLAGE D'AVIONS
Airbus optimise la disponibilite de ses systemes electriques a basse tension avec Eaton
Afin de garantir un assemblage irréprochable en termes de fiabilité du réseau électrique, Airbus a mis en place des mesures de reconditionnement poussées pour le système d'alimentation basse tension de ses modèles à succès A320. Sur la base de la technologie d'Eaton, le système électrique a été rapidement mis à jour pour se conformer efficacement aux dernières normes en matière de contrôle, de sécurité et de protection du personnel.
VINGT AIRBUS PAR MOIS
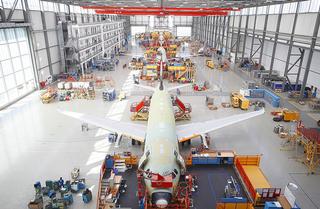
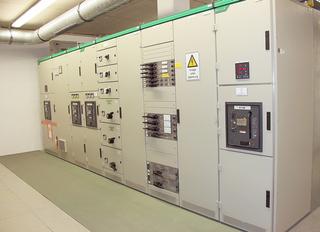
Les trois lignes d'assemblage à Hambourg tournent de jour comme de nuit afin de satisfaire la demande élevée de ces modèles à succès.
Chaque mois, plus de vingt avions sont assemblés. La ligne d'assemblage comprend quatre stations de travail, où l'avion est construit en quelques jours, comme sur une bande transporteuse. Ces stations assemblent, par exemple, les sections du fuselage et montent les ailes, le stabilisateur vertical, le gouvernail de profondeur, les moteurs, le train d'atterrissage et les sièges. Dans le hall 9, qui abrite la ligne d'assemblage finale, des stations individuelles peuvent être relevées ou rabaissées pour que l'avion soit libéré et déplacé entre les stations.
MAXIMALISER LA DISPONIBILITE DU SYSTEME ET LA SECURITE DU PERSONNEL
L'unité d'alimentation basse tension pour le hall 9 utilise depuis des années le système de qualité Modan d'Eaton. Dans le cadre du reconditionnement, Airbus a décidé de mettre à jour son installation existante afin d'optimiser la disponibilité de l'alimentation électrique. Pour l'équipe de maintenance et responsable de l'énergie d'Airbus, cela implique une plus grande fiabilité technique du système et la possibilité d'effectuer un contrôle poussé du système et des composantes, avec un lien vers le système de gestion de la construction, en plus d'une sécurité renforcée pour le personnel. Il n'était pas possible de remplacer toute l'installation, car cela aurait pris des heures et la production aurait dû être arrêtée. Le système existant devait donc être remodelé.
REMANIEMENT DU SYSTEME
Dans le cadre de ce projet, le constructeur a choisi de consulter Eaton afin de développer une solution complète, avec contrôle du système de commutation et de la température aux points critiques, en passant par un système de protection d'arc. Les automates IZM d'Eaton de la série Moeller constituent la pierre angulaire de cette solution et permettent une puissance de sortie de 630 à 4.000 A avec unité d'activation électronique et fonction de mesure intégrée. Ces interrupteurs d'alimentation électrique permettent d'envoyer des données vers un système de logging et de visualisation BreakerVisu, par exemple dans le cas d'une tension trop élevée, trop basse ou d'une surtension. Tous les interrupteurs existants NZM sont repris dans le système de contrôle. Ce procédé était le plus simple grâce à la connexion intelligente SmartWire-DT et au système de communication.
OUTIL DE CONSULTATION

La nouvelle solution d'Eaton repose sur un appareil de contrôle (contrôleur diagnostic) à sondes de température autonomes destinées à contrôler tous les systèmes de rails et les branchements, et à surveiller tous les autres points de mesure. Les valeurs de température sont régulièrement envoyées par connexion sans fil au contrôleur (toutes les dix minutes environ). Cette connexion sans fil simplifie l'installation et permet de libérer des guides la zone autour du système de rail. Dans le cadre de ce projet, près de 80 sondes de température ont été installées dans le système de commutation pour le hall 9. Eaton a enregistré les valeurs thermiques seuils pour le système de commutation Modan directement dans le contrôleur. Le comportement thermique du système a été analysé au travers de plusieurs tests et les réactions mathématiques relatives ont été intégrées. En cas de variations, le système émet un avertissement par rapport à l'erreur et active une alarme en cas de dépassement d'un seuil prédéfini. Ces notifications sont envoyées via BreakerVisu vers le système de contrôle d'Airbus, pour permettre de corriger l'erreur avant d'être confronté à une vraie situation critique. Afin d'améliorer l'unité de distribution électrique en termes de sécurité pour le personnel et parce que Airbus a déjà eu de bonnes expériences avec le système de protection d'arc Arcon d'Eaton ailleurs le système a également été équipé d'un système de protection d'arc. Grâce aux nouvelles sondes à pointe, l'installation a été modifiée en quelques heures à peine.
FIABILITE MAXIMALE ET UNE INSTALLATION QUASI NEUVE
Au terme de cette installation réussie, Airbus s'est dit très satisfait du résultat. Le concept développé conjointement avec Eaton s'est avéré très efficace et permet à l'équipe de maintenance et de gestion de l'énergie de disposer d'un aperçu complet et détaillé du système. Le système de distribution basse tension du hall 9 est complètement remis à jour et intègre la technologie la plus récente. L'implémentation n'a duré qu'un week-end grâce à une préparation efficace et à une collaboration étroite entre les équipes de production. Le système de commutation a été éteint de 22h00 un vendredi d'octobre 2015 pour être relancé le dimanche à 18h00, pour que la production puisse reprendre dès le lundi matin. Au terme du remaniement, le système a été entièrement inspecté et certifié pour une garantie de 36 mois, comme si elle était neuve. Sur la base de cette expérience fructueuse, Airbus envisage d'appliquer le même concept à d'autres halls sur le site de Finkenwerder.