MECHANISCHE OVERBRENGINGEN VERVANGEN DOOR SERVOSTURING
JBT herontwerpt afvulmachine met hulp van Siemens
De voedingsverwerkende industrie staat onder druk van de retail. Producenten moeten kwaliteitsvolle en voedselveilige producten afleveren tegen een zo laag mogelijke kost. Als fabrikant van vul-, sluit- en sterilisatiemachines probeert JBT (John Bean Technologies) hen zo goed mogelijk bij te staan bij deze uitdagingen. Samen met Siemens werkte het bedrijf aan een redesign van zijn Unifiller, die dient voor het afvullen en sluiten van 'liquid foods' in zowel blikken als glazen bokalen. De mechaniek werd daarbij vervangen door een digitale servosturing. Resultaat: een machine met gesynchroniseerde assen die tot wel 1.200 verpakkingen per minuut aankan.
MACHINEBOUWER VOOR DE VOEDINGSINDUSTRIE
JBT (John Bean Technologies) werd medio jaren 1800 al opgericht door de Amerikaanse ingenieur die het bedrijf zijn naam verleende. Door de overname van de bedrijfstakken AeroTech en FoodTech van de industriële groep FMC, zo'n honderd jaar later, groeide de onderneming uit tot de wereldspeler die ze vandaag is. JBT vestigde zich net na WOII in Sint-Niklaas en bouwt tegenwoordig allerlei afvul-, sluit- en sterilisatiemachines voor de voedingsindustrie.
Troeven
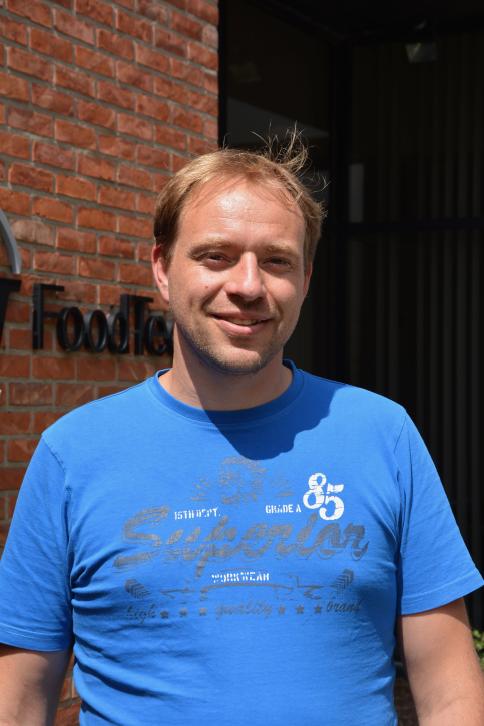
“Zowel de engineering als de eigenlijke productie van de machines doen wij 'tailormade', en dus vrijwel altijd volgens de specifieke wensen van de klant. Dat is meteen de belangrijkste troef van ons bedrijf, maar het maakt ook dat we geen afgebakend productportfolio hebben; laat staan dat wij machines 'off the shelf' kunnen aanbieden", zegt lead controls engineer Bart Aluwe.
“Daarnaast kiest men ook dikwijls voor ons om de sterke support die wij aanbieden na de verkoop. Wij hebben immers over de hele wereld lokale sales- en servicemedewerkers op onze payroll staan die de klanten snel kunnen bijstaan, en dat bovendien dikwijls in hun eigen taal", stelt hij.
“In de voedingsindustrie streeft men naar een hoge kwaliteit en voedselveiligheid tegen een lage kost per unit"
UNIFILLER
Door deze globale aanpak kent het bedrijf ook de diverse nichemarkten waarin hun klanten actief zijn, en welke specifieke aandachtspunten daarbij dan van belang zijn. Als machinebouwer willen ze aan die verscheidene behoeften tegemoetkomen.
High capacity & high quality
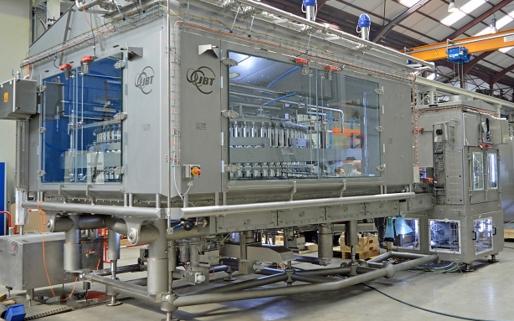
“De nieuwe Unifiller is een prima voorbeeld. We werden de jongste jaren gecontacteerd door diverse grote spelers in de zuivelindustrie, die gekenmerkt wordt door heel prijsgevoelige producten. Om nog geld te kunnen verdienen, hebben zij nood aan 'high capacity', zonder dat de 'high quality' daarbij in het gedrang mag komen. Zij waren dus op zoek naar een snelle afvul- en sluitmachine met een hoge flexibiliteit voor eventuele productwissels, die bovendien heel nauwkeurig doseert om op die manier ook productverliezen zo veel mogelijk in te perken. Veel van deze bedrijven exporteren namelijk geen zuivere melk, maar bijvoorbeeld melk die geëvaporeerd is of een 'added value' meekreeg, zoals extra proteïnen of vitaminen. Gecondenseerde melk kreeg al meerdere thermische behandelingen voor het afvullen, dus dat is geen goedkoop goedje dat je langs de machine wil zien lopen", weet Aluwe.
Hygiënisch ontwerp
“Bovendien is ook een hygiënisch ontwerp hier van groot belang. We hebben van bij de ontwerpfase gestreefd naar een makkelijk te reinigen machine met een volledig geautomatiseerde CIP-reiniging, zonder dat je de machine daarvoor helemaal moet ontmantelen. Deze eisen gaan echter steeds verder."
REDESIGN
Om aan al deze vragen te beantwoorden, drong een 'redesign' van de bestaande Unifiller zich op. De mechanische overbrengingen voor de koppeling tussen de in de hoogte verstelbare, roterende vul- en sluitstations en de vaste, maar eveneens roterende invoerster, werden daarbij vervangen door een digitale servosturing. Dat resulteert in verschillende voordelen.
Hoge flexibiliteit en nauwkeurigheid

“Dat de vul- en sluitstations in de hoogte regelbaar moeten zijn, is om vlot te kunnen wisselen tussen verschillende verpakkingen. De vrije 'headspace' boven aan de blikken of bokalen is dan weer een erg belangrijke factor bij het afvullen zelf. Met name tijdens de sterilisatie heeft dit immers een grote invloed op de uiteindelijke kwaliteit en voedselveiligheid van de producten. Ook de lijnsnelheid wordt bepaald door de verpakkingen en de af te vullen producten, waarbij we ook rekening moeten houden met de middelpuntvliedende kracht. Die lijnsnelheid kunnen we dus niet tot in het oneindige opkrikken, maar we zijn er nu wel in geslaagd om maar liefst 81 vulstations in één machine in te bouwen. Hierdoor kunnen nu tot 1.200 blikken per minuut gevuld en gesloten worden, en dat met een nauwkeurigheid op de synchronisatie van de servomotoren van 0,2 mm op de buitendiameter van 3,5 m. Dit is dus een proces dat heel synchroon moet lopen en waarvoor een grote rekenkracht vereist is", legt Aluwe uit.
Servosturing
“Vroeger gebruikten we heel specifieke, dure gearboxes voor de link tussen deze verschillende componenten, die bovendien veel plaats innamen. Zo was er ook een gearbox voor de mechanische bijstelling van de kettingen tussen de vullers en de sluiters, die onderhevig waren aan rek. Om dit perfect af te stellen, moest dit gebeuren, terwijl de machine in werking was, wat absoluut geen evidente klus was. Door van één algemene aandrijving over te schakelen op drie compact ingebouwde, gesynchroniseerde motoren - voor de invoerster, de vulkuip en de sluiter - die elk apart worden aangedreven, vallen alle nadelen van deze gearboxes weg. Dankzij de servosturing kunnen we de eventuele bijstellingen nu softwarematig uitvoeren, wat veel eenvoudiger verloopt. Voor een perfect procesverloop wordt alles nu ook elektronisch gecontroleerd en opgevolgd, waardoor de eindklant minder operatoren hoeft in te zetten", klinkt het.
Co-engineering en support

“We hadden al een jarenlange, goeie samenwerking met Siemens op PLC-gebied. In nauw overleg met hen vonden we de juiste combinatie voor de complete aandrijftrein, waarbij zij mee nadachten over de mapping tussen het mechanische en het elektronische gedeelte. We kunnen daarbij zeker spreken van een 'co-engineering', veeleer dan louter een productlevering. Zij kwamen hier namelijk enkele keren ter plaatse, ook om ons de nodige support te verlenen. Het gekozen Simotion platform is immers een high-endmotionplatform dat specifiek bedoeld is voor dynamische omgevingen die een hoge rekencapaciteit vereisen. Daar is enige kennis voor nodig, die verder reikt dan het klassieke PLC-niveau", aldus nog de lead controls engineer.
EVALUATIE
“We kozen voor Siemens vanwege onze positieve ervaring uit het verleden en door het feit dat zij net als ons wereldwijd actief zijn in de voedingsindustrie, wat voor ons heel belangrijk is naar service en support toe. Door hun nauwgezette begeleiding bleek dit zeker een juiste partnerkeuze", evalueert Aluwe.
“Ook wat de aangeleverde oplossing zelf betreft, zijn we heel tevreden. Die stelde ons immers in staat om op drie verschillende vlakken kostenbesparingen te realiseren voor de eindklanten. Vooreerst zijn de servomotoren een energiezuiniger alternatief door het wegvallen van de mechanische verliezen. Daarnaast moeten er door de elektronica minder operatoren worden ingezet en moet men daar ook niet naar op zoek. En tot slot zijn aanpassingen nu veel makkelijker door te voeren, door gewoon een paar lijnen te herschrijven in de code", besluit hij.