LA COMBINAISON DE LA REDUCTION DU BRUIT ET DE LA DURABILITE EST LE PLUS GRAND DEFI AU REVETEMENT 'PORO-ELASTIOQUE' ULTRA SILENCIEUX
PROJET PILOTE CRR AVEC REVETEMENT 'PORO-ELASTIQUE' ULTRA SILENCIEUX
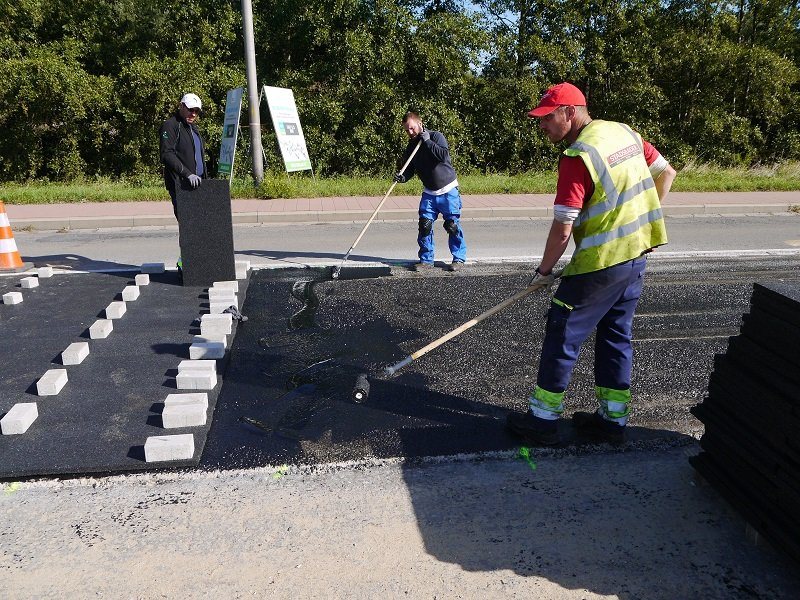
Quiconque habite près d'une route fréquentée le concédera sans aucun doute: le trafic engendre du bruit, beaucoup de bruit. La pratique nous apprend que le bruit d'un moteur automobile à partir de 30 à 40 km/h est négligeable par rapport au bruit de l'interaction des pneus et du revêtement, aussi appelé bruit de roulement. C'est là qu'une grande réduction de bruit peut être réalisée. Le Centre de Recherches Routières (CRR) étudie la possibilité d'utiliser des matériaux poro-élastiques en guise de revêtement. Récemment a été présentée à Gand une zone d'essai avec ce type de revêtement innovant.
SOLUTIONS EXISTANTES INSUFFISANTES?
Ces dernières décennies, des innovations sont apparues dans les revêtements réducteurs de bruit:
- SMA (stone mastic asphalt) avec petit agrégat (par exemple max. 7 mm);
- EBD (enrobé bitumineux drainant) double couche;
- revêtements d'asphalte minces insonorisants.
Les revêtements silencieux procurent la plus grande réduction sonore au début de leur durée de vie. Pour l'EBD, il s'agit par exemple d'environ 3 dB(A). L'EBD double couche, considéré aujourd'hui comme le revêtement le plus silencieux au monde utilisable avec efficacité, atteint une réduction du bruit de 5 à 7 dB(A). Notez que l'EBD n'est plus utilisé en Belgique en raison de facteurs tels que l'entretien hivernal. Aux Pays-Bas, l'EBD est utilisé, comme revêtement standard sur le réseau autoroutier.
REVETEMENT PORO-ELASTIQUE
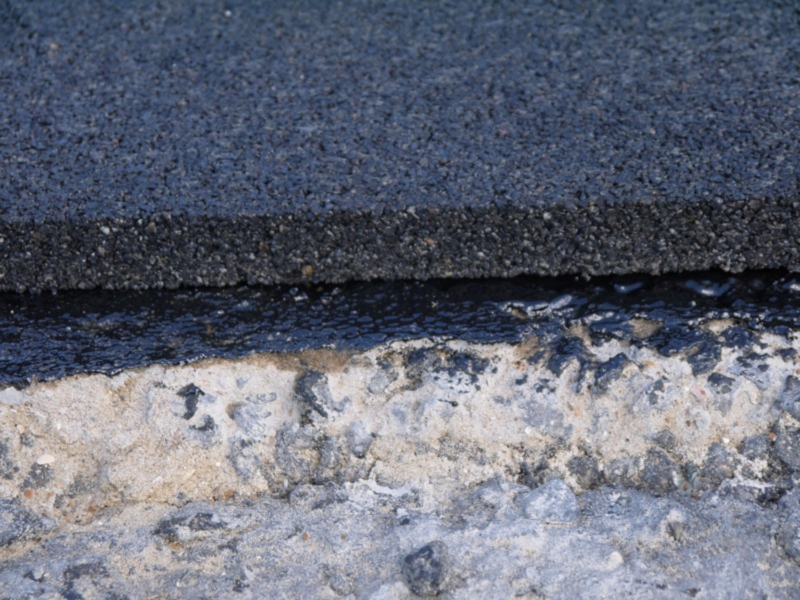
Une piste intéressante est PERS, ou 'poro-elastic road surface'. Ce type de revêtement est constitué d'une couche de finition avec d'une part une grande teneur en cavités (jusqu'à 35%) et d'autre part une élasticité du même ordre que celle des pneus qui circulent par-dessus. Le PERS doit être collé sur une sous-couche spéciale, qui repose à son tour sur les sous-couches d'asphalte classiques. Ce type de revêtement permet d'atteindre des réductions sonores considérables par rapport à l'asphalte dense, de 10 à 12 dB(A). Le PERS surclasse de loin les autres revêtements silencieux en termes de réduction sonore. A titre de comparaison: un écran acoustique de 4 mètres de haut crée un effet de réduction sonore de 8 dB(A). Dans la pratique, ces propriétés peuvent être réalisées par un mélange de particules de caoutchouc de forme cubique ou oblongue qui sont liées par une résine synthétique élastique. Par ailleurs, il comprend des pierres pour garantir une bonne rigidité. La particularité est que les particules de caoutchouc pour le PERS proviennent de pneus de voiture et de camion recyclés. Ces granulats de caoutchouc constituent environ 30% de la masse du mélange. En d'autres termes, le PERS a une évidente valeur écologique car il offre une solution durable au recyclage des pneus automobiles en caoutchouc dont 85.00 tonnes doivent être traitées chaque année rien qu'en Belgique.Le liant élastique utilisé est le plus souvent le polyuréthane, qui constitue environ 20 pour cent de la masse du mélange. Environ 50% de la masse sont constitués de pierres, pour la rigidité comme relevé. Eventuellement, de petites fractions d'additifs sont ajoutées dans un but spécifique, par exemple accroître la résistance aux UV ou comme produit anti-ruissellement.
TESTS INSTRUCTIFS DU PASSE
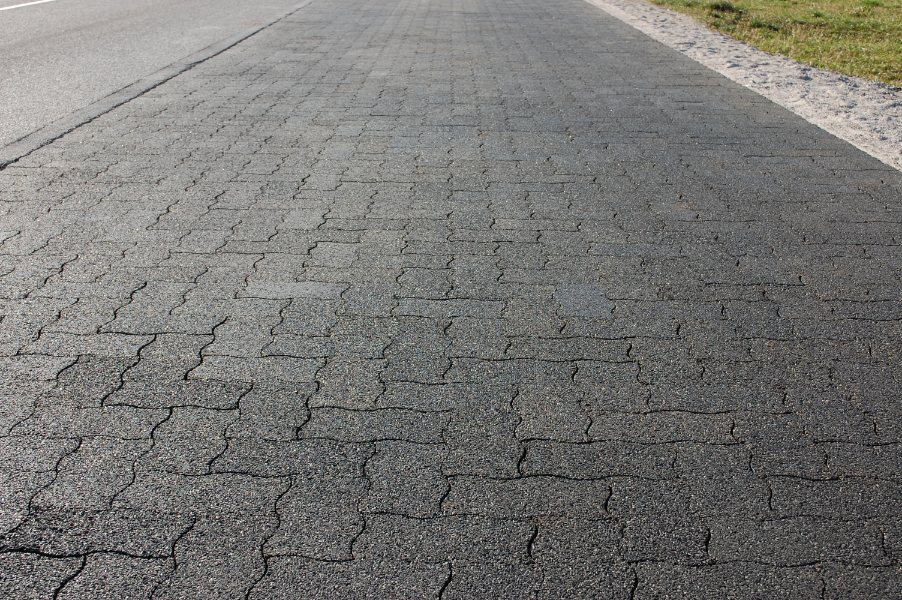
Entre-temps, certains projets pilotes intéressants autour du PERS ont donné des résultats promoteurs mais ont aussi clairement montré quelques points d'action.
Le PERS a été inventé en Suède et c'est aussi là que sont apparues les premières zones d'essai, il est vrai en dehors de la circulation régulière. Les premiers résultats étaient prometteurs, avec des réductions sonores jusqu'à 10 dB.
Une seconde expérience a eu lieu fin des années 80 en Norvège. Là, la zone d'essai de 130 mètres se situait dans un environnement à faible circulation. Les réductions sonores mesurées variaient de 7 à 9 dB. Toutefois le projet a été arrêté subitement lorsqu'un chasse-neige est passé sur le revêtement et l'a sérieusement endommagé.
De retour en Suède, un nouveau projet pilote a été lancé en 2004, cette fois avec trois types de PERS. Un type avec des panneaux (1 m x 1 m) de fabrication japonaise ('Tokai') collés avec de l'époxy sur un revêtement en asphalte en partie fraisé, des panneaux britanniques similaires ('Rosehill') et enfin un revêtement PERS 'continu' fabriqué in situ. L'expérience suédoise ne fut pas non plus un succès. Après quelques mois, la sous-couche d'asphalte s'est cassée et l'expérience a dû être stoppée. L'important est que la cause de l'échec ne devait pas être cherchée dans le revêtement PERS. Il était encore en excellent état lors de l'arrêt de l'expérience et adhérait encore parfaitement à la sous-couche.
Une expérience suivante a eu lieu aux Pays-Bas. Ici, il s'agissait d'une disposition d'essai sur une route mise hors service avec des panneaux de fabrication japonaise. Les résultats acoustiques de l'essai hollandais ont quelque peu déçu: seule une réduction de 7 dB(A) a été mesurée, ce qui semblait dû à une moins bonne finition des joints entre les panneaux. Ici aussi l'échec n'était pas d'emblée imputable au PERS. Un vaste programme s'est tenu au Japon à partir du milieu des années 1990. Là, plusieurs projets pilotes ont été menés ces dernières décennies. Les résultats acoustiques étaient très bons et on a atteint une longévité d'env. 4 ans.
A partir de 2009, les programmes d'essai en Europe ont été étoffés également. Sous le giron du projet européen PERSUADE, des tests ont été menés en Suède, au Danemark, en Slovénie, en Pologne et chez nous en Belgique à Herzele et à Sterrebeek. La longueur des zones d'essai ont varié de 20 à 75 m, avec des compositions PERS et des méthodes d'application variables. Les résultats d'essai étaient prometteurs en termes de réduction sonore: dans un cas spécifique on a même atteint 11 dB. Ces tests ont toutefois mis en lumière quelques points d'attention importants, comme la durabilité.
NOUVEAU PROJET A GAND
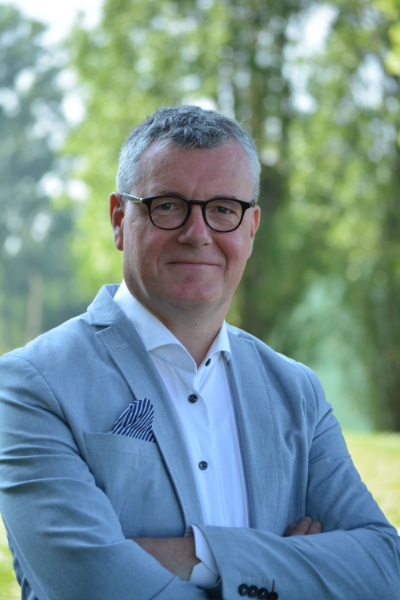
Luc Goubert, chercheur senior auprès du CRR, nous raconte ce qu'il espère apprendre du nouveau projet pilote: “A Herzele, nous avons utilisé un mélange fabriqué dans une centrale à béton et répandu in situ avec une finisseuse d'asphalte classique. C'était joli visuellement mais avec le temps, environ neuf mois, le PERS s'est détaché de la sous-couche. Dans un projet pilote au Danemark, nous avons vu une usure similaire. Après environ 14 mois, le PERS a dû être remplacé; il n'était donc absolument pas assez durable."
Afin de traiter ces points d'attention, une nouvelle zone d'essai de 44 mm de long dans la Noorderlaan à Gand teste la réduction du bruit: “Le mélange de caoutchouc consiste ici en petites fractions de grains de pneu automobile broyé, dans lesquelles sont mélangées des pierres. Celles-ci procurent la rigidité nécessaire."
“Par rapport à Herzele, nous avons travaillé ici pour la pose avec des plaques préfabriquées collées sur une sous-couche combideck très rigide. Une couche combideck consiste en un EBD dont les cavités sont remplies d'une boue de ciment, ce qui procure une sous-couche très rigide. C'est un peu comparable au procédé utilisé sur des trajets d'autobus très sollicités pour éviter l'orniérage. Le principe est développé au Japon, mais des tests précédents en Suède nous ont appris que ce type de PERS, combiné avec une sous-couche très rigide, est assez durable: là, le revêtement a fort bien presté pendant 2,5 ans dans des conditions pénibles, comme par exemple une lourde circulation et des températures hivernales. Lorsqu'il a été retiré, ce fut dans le cadre du réaménagement de la route et non pas parce que le PERS était cassé. J'ai donc bon espoir que la durabilité de cette zone d'essai sera satisfaisante dans nos conditions climatiques tempérées."
Utilisable sur des endroits sensibles
La zone d'essai gantoise sera suivie de façon intensive par le CRR, d'une part pour surveiller les effets de réduction sonore, d'autre part pour étudier l'usure, la rigidité et le bruit de roulement du revêtement.
Luc Goubert: “Le but est que ce revêtement ultra silencieux devient dans les prochaines années une alternative à part entière dans le marché de niche des revêtements silencieux. Il peut être utilisé sur des endroits où une très grande réduction sonore est nécessaire et où des écrans sonores ne peuvent pas être placés. Les premiers résultats sont du reste très prometteurs. Lors du passage d'une voiture à 50 km/h, nous avons mesuré une réduction de 9 dB(A). A 80 km/, ce fut même 10 dB(A). L'équivalent d'un écran lumineux de 6 m de haut. Aucun autre type de revêtement atteint ce résultat."
"A Gand, nous avons colle des plaques prefabriquees sur une sous-couche combideck tres rigide"
Points d'attention
“En ce qui concerne le prix, le propos est nuancé. En comparaison de l'asphalte ordinaire, il est bien entendu un peu plus cher. Il y a le liant plus cher et le placement n'est pas (encore) automatisé comme pour un revêtement traditionnel. Les tapis sont placés et collés manuellement, ce qui limite provisoirement la vitesse de pose à 8 à 10 m par heure. Mais dès que cette technique sera plus largement répandue, le degré d'automatisation et la vitesse augmenteront. Si l'on compare avec d'autres mesures antibruit telles que des écrans acoustiques, cela peut devenir une technique compétitive."
“Ce type de revêtement n'a aucune influence négative sur l'usure du pneu, mais la résistance au roulement est un plus peu élevée. Cela résulte dans une consommation accrue de 2% pour les voitures et même encore un peu plus pour les camions. Mais comme seule une fraction minime du réseau routier sera équipé de ce type de revêtement, c'est négligeable. Une étude sur le comportement hivernal est aussi effectuée, les résultats sont variables. En raison des cavités plus grandes, les frimas se manifesteront plus vite que sur l'asphalte ordinaire, mais le comportement en cas de pluie verglaçante est meilleur."
“La durabilité est le point d'attention le plus important. Dans des tests précédents, ce n'était pas suffisant. J'ai confiance que ce revêtement d'essai sera bel et bien assez solide. Les résultats du projet suédois me confortent dans cette conviction."
COMPOSITION BRUIT DE PNEU
Le bruit causé par les pneus est une interaction complexe entre plusieurs mécanismes, si bien que nous pouvons parler d'un bruit réellement composé.
- Le pompage de l'air est un phénomène qui comprime l'air à l'avant du pneu en roulant sur une surface plane. L'échappement de cet air comprimé entraîne du bruit, ceci est dénommé pompage de l'air. A l'arrière du pneu, ceci induit aussi une production sonore quand l'air est aspiré.
- Des vibrations à partir des pneus sont surtout provoquées par des irrégularités dans le revêtement de dimensions horizontales entre1 cm et environ 20 cm. En roulant sur de telles surfaces rugueuses, ces irrégularités 'martèlent' la bande de roulement et la font vibrer; comme la surface latérale du pneu y est reliée, elle vibre aussi et émet le bruit.
- Les deux sources de bruit sont encore aggravées par la réflexion du bruit dans le 'triangle' entre le pneu et le revêtement, ce qui est toutefois réprimé par un revêtement qui absorbe le bruit, comme l'EBD et encore davantage avec le PERS.