DURACELL GAAT NOG VEEL LANGER MEE VIA TRANSFORMATIE TOT SMART FACTORY
Transformatie slimme batterijenfabriek afgerond tegen 2020
In de afgelopen vijf jaren moest Duracell in Aarschot meermaals herstructureren. In oktober 2017 mocht de lokale directie echter bekendmaken dat Berkshire Hathaway (de nieuwe eigenaar, met aan het roer multimiljardair Warren Buffett), de komende drie jaar 50 miljoen investeert in de vestiging. De bedrijfsleiding van Aarschot stelde een plan op met een duidelijk doel: de productiekosten van de Chinese zustervestiging evenaren via een snellere en slimmere productie. Om die opdracht tot een goed einde te brengen, nam Duracell Ometa en Devoteam in de arm.
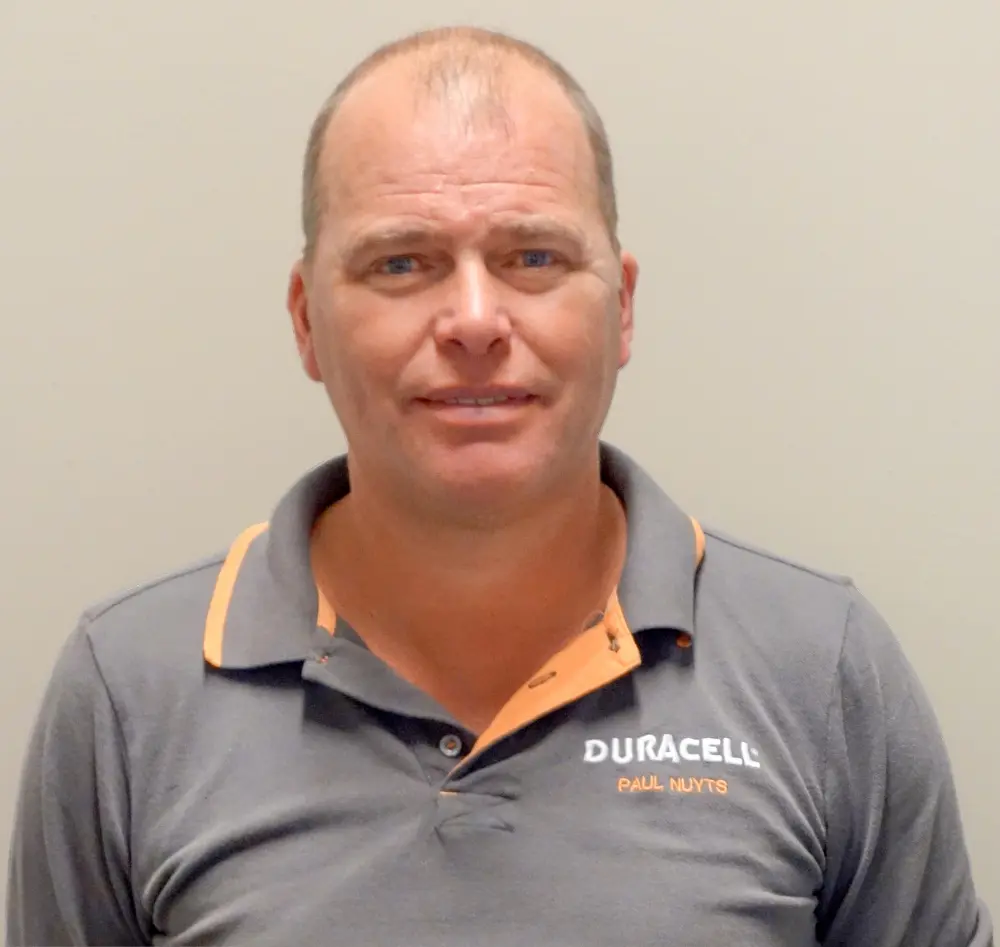
CONCURRENTIE IN HET OOSTEN
Bij de start in 1967 produceerde Duracell Aarschot 50.000 batterijen op jaarbasis. Vandaag produceert de vestiging elke dag vijf miljoen AA- en AAA- batterijen voor huishoud- en andere toestellen, die vertrekken richting andere Europese landen, het Midden-Oosten en Afrika. Op capaciteitsvlak zit het dus alvast goed. Zo'n vijf jaar geleden kwam het voortbestaan van de Aarschotse vestiging echter even in het gedrang. Een van de voornaamste oorzaken was het compacte karakter van de batterijen. Dat maakt ze immers makkelijk te transporteren, een gegeven dat natuurlijk ook de conculega's in de kaart speelt. Van de in totaal vijf vestigingen van Duracell (één in Europa, drie in de VS en één in China) beschikt de zustervestiging in China vandaag overigens over de best presterende productielijnen en ook op andere vlakken wordt daar minstens even goed of beter gescoord. Net als westerse bedrijven werkt ook China met lokale leveranciers en goedkopere materialen, en wordt daar ook volop aan automatisering, outsourcing van non-coreactiviteiten en lean manufacturing gedaan. De tijd dat westerse bedrijven hun producten als superieur op de markt kwijt konden, is voorbij. Wat kon Duracell nog in de concurrentiestrijd gooien? Moest het toch op een betere kwaliteit blijven inzetten en erop rekenen dat de inflatie wel zou toeslaan in het Verre Oosten? Enkele jaren terug stelde de bedrijfsleiding een duidelijk meetbaar doel voorop: de kost per in Aarschot geproduceerde batterij (inclusief de transportkosten richting haar afzetmarkten) moest de zuster in China evenaren. Daarvoor moest het productiesysteem van Duracell achtereenvolgens sneller en slimmer worden.
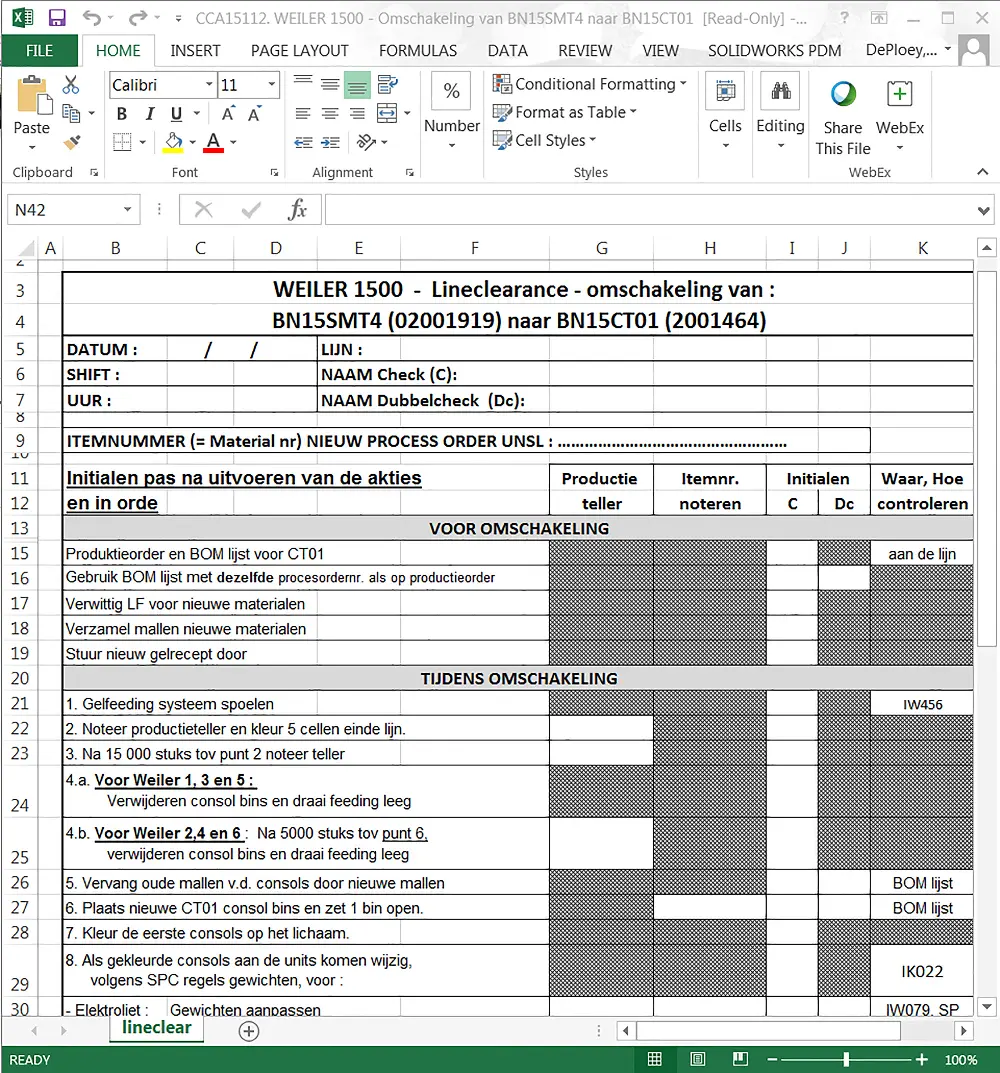
op niet-geconnecteerde data in Excel bestanden
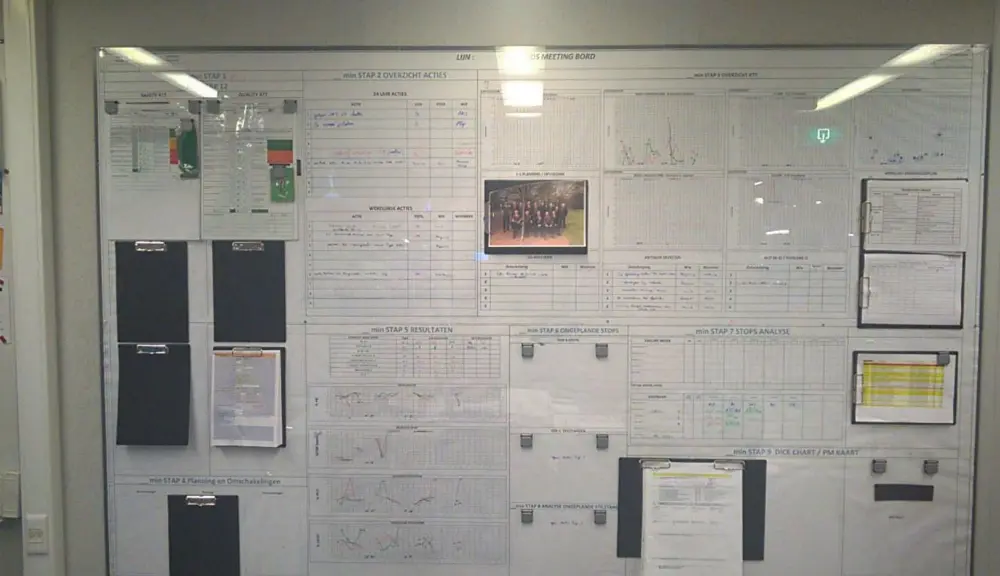
EXCELSYNDROOM
Begin 2016 legde Duracell Aarschot zijn werkprocessen onder de loep om alle administratieve handelingen zonder meerwaarde bloot te leggen. Daarbij kwamen problemen aan het licht die eigen waren aan de complexiteit van de werkprocessen, het werken met mensgestuurde systemen en gescheiden bedrijfssystemen (ERP, WMS, MES …). Belangrijk was de vaststelling dat er in bepaalde gevallen tot 20.000 uur werd besteed aan documentbehandeling. Een belangrijk deel van de administratie berustte er tot voor kort op Excel en allerhande formulieren. Per departement (sales, procurement, warehousing …) waren er key users aangesteld om data in te voeren en over te zetten tussen verschillende softwarepakketten. “Dat was de enige manier om informatie door onze waardeketen te pushen", licht Paul Nuyts toe, als Industry 4.0 project leader in de Aarschotse vestiging. Bepaalde data moesten meermaals worden overgetypt of uitgeprint, manueel aangepast, gescand en verstuurd, waarbij die natuurlijk ook tijdig en bij de juiste perso(o)n(en) moesten terechtkomen. Daarnaast speelt ook het feit dat mensen wel eens dure fouten maken (denk maar aan een ongelukkig geplaatst decimaal teken in een betalingsdocument ...). Als data vaak manueel moeten worden overgenomen, neemt de kans op dergelijke fouten toe. Bijkomend kan er heel wat tijd kruipen in mail- en telefoonverkeer met vragen om verduidelijking of rechtzettingen. Voorheen kon elk departement in feite worden gezien als een eiland. Informatie over productieplanning, warehousing etc., opgeslagen in Excelbestanden of andere formaten, moest telkens worden opgevraagd via een van verschillende niet-gekoppelde interfaces.
TEAMPORTALEN
De uitdaging bestond erin om over te schakelen van een systeem van pull naar push information. In plaats van info te laten opzoeken via een veelheid aan interfaces, wou Duracell info in de juiste vorm presenteren aan wie erover moet beschikken. Ometa biedt een integratieplatform dat bedrijfsapplicaties zoals ERP- en productiesystemen koppelt aan portaalsystemen of een CMS - in dit geval Microsoft SharePoint. Zo kan alle info rond productieplanning, productiehoeveelheden, afvalpercentages, onderhoud, veiligheids- en kwaliteitscontrole, die voorheen op verschillende plaatsen manueel werd verwerkt, meteen automatisch doorstromen naar SharePoint. Via hun digitale werkplek staan de verschillende teams met elkaar in contact en kunnen ze uit de onderliggende systemen waarmee de interface in verbinding staat, realtime de nodige procesinfo inwinnen.
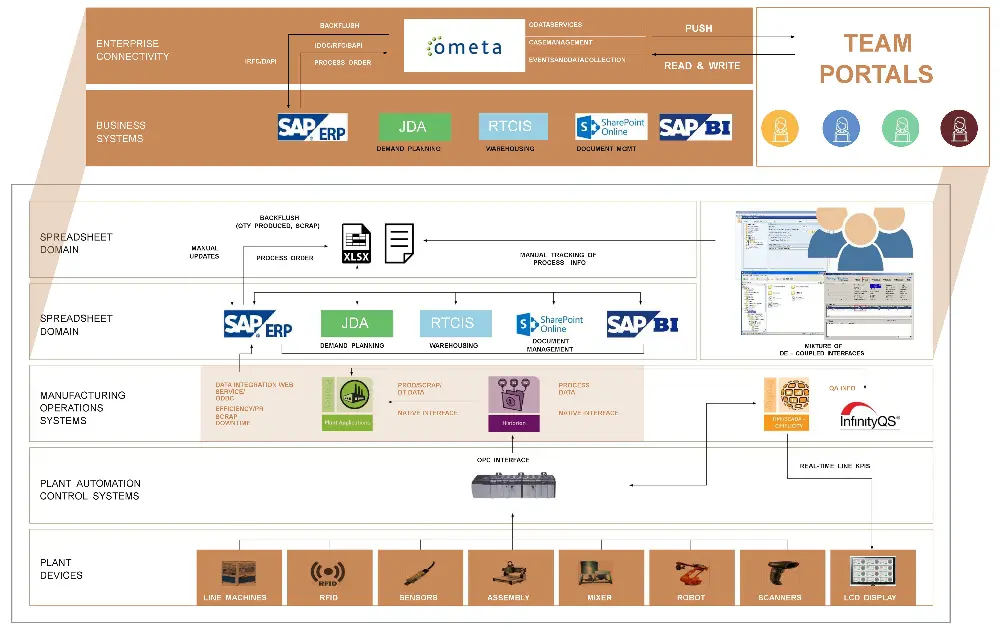
in de nieuwe wordt de nodige info op het juiste moment realtime gepresenteerd via portalen
DIGITAL TWIN
Bij Duracell ondergaat elke batterij tijdens het productieproces negen verschillende transformaties die cruciaal zijn voor de kwaliteit van het eindresultaat. Elk daarvan wordt dan ook nauwkeurig gemonitord. Camera's, sensoren, RFID, robots, mengers en andere apparaten op de productielijnen verzamelen een massa big data rond een tiental kritische parameters. Omdat nog te veel van de opgeslagen data onbenut blijven ('datasilo's'), wil Duracell elke batterij voorzien van een digital twin met daaraan gekoppeld allerlei verzamelde data over WMS, MES, ERP, productreeks, machinedata, componentendata ... Als op basis van die virtuele twin voor elke batterij bepaald kan worden of ze aan alle kwaliteitscriteria voldoet, dan zijn er achteraf geen steekproeven meer nodig per batch voor een labanalyse, wat tijd helpt te besparen. Operators zullen ook tijdig kunnen ingrijpen in het proces en zo de hoeveelheid scrap helpen reduceren.
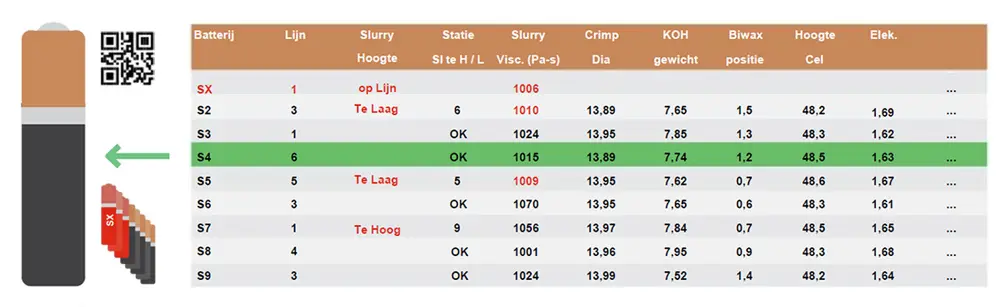
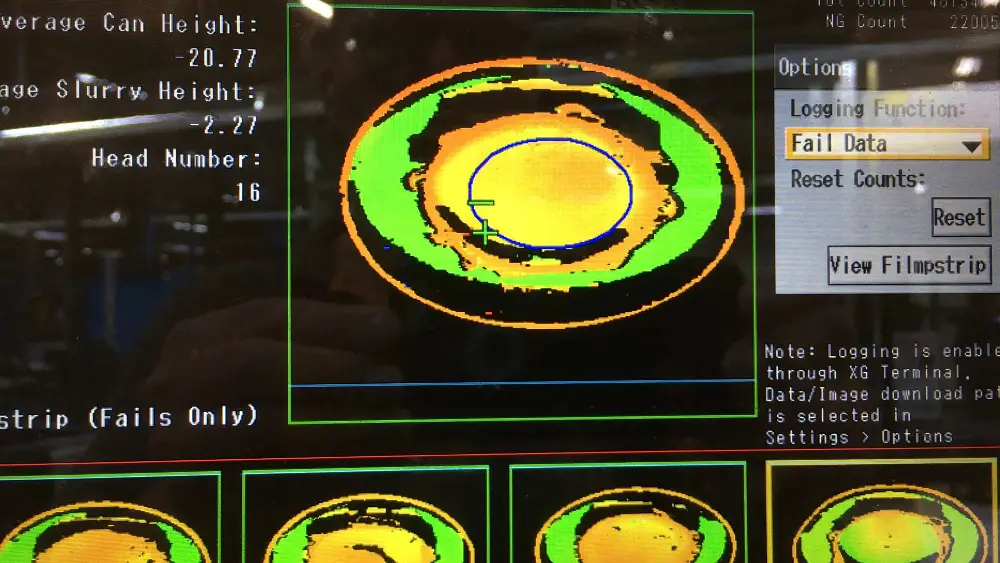
MACHINE LEARNING VOOR PREDICTIE
Bij wijze van pilootproject besloot Duracell machine learning toe te passen op de productielijnen voor de anodecomponent van de batterijen. Er werd gepland om in Q1 van 2018 elke individuele cel per transformatie te digitaliseren via slimme camera's en laserscanners op de lijnen. Gelijktijdig schakelde het bedrijf over van een manuele reiniging met water naar een laserreiniging, en waar voorheen slechts enkele samples visueel gecontroleerd werden op eventuele schade, komt er in de plaats een inline lasergebaseerde controle van alle batterijen. Een ander werk in die periode bestond in het verder uitwerken van de realtime digital twin, waarbij monitoring van de kritische parameters zou leiden tot meer dan 180 miljoen datapunten op basis waarvan voorspellingen worden gedaan om onnodige stops en scrap te reduceren. Voorts op de agenda voor het tweede kwartaal van 2018: structureren van de realtime data. De invoering van de OPC UA standaard zorgt ervoor dat ook niet-Windowsprogramma's kunnen communiceren met industriële hardware.
In het voorjaar van 2019 zou de digitale assistent de volle aandacht krijgen. De operators kregen eind 2017 al via de schermen van pc's en tablets hun taken toegewezen, waarbij door middel van kleuren de prioriteit werd meegegeven (rood voor dringende taken ...). Afgewerkte taken vinken zij af, wat automatisch wordt verwerkt op SharePoint en weergegeven via dashboards.
