DURACELL: TRANSFORMATION EN SMART FACTORY POUR DURER ENCORE PLUS
La transformation en usine de piles intelligente bouclée d'ici 2020
Ces cinq dernières années, Duracell à Aarschot a dû procéder à plusieurs restructurations. En octobre, la direction locale a toutefois annoncé que Berkshire Hathaway (le nouveau propriétaire, avec à la barre le multimilliardaire Warren Buffet) allait investir ces trois prochaines années 50 millions dans le site. La direction d'Aarschot a établi un plan avec un objectif clair: égaler les coûts de production de l'usine sœur chinoise via une production plus rapide et plus intelligente. Pour mener cette tâche à bien, Duracell s'est tourné vers Ometa et Devoteam.
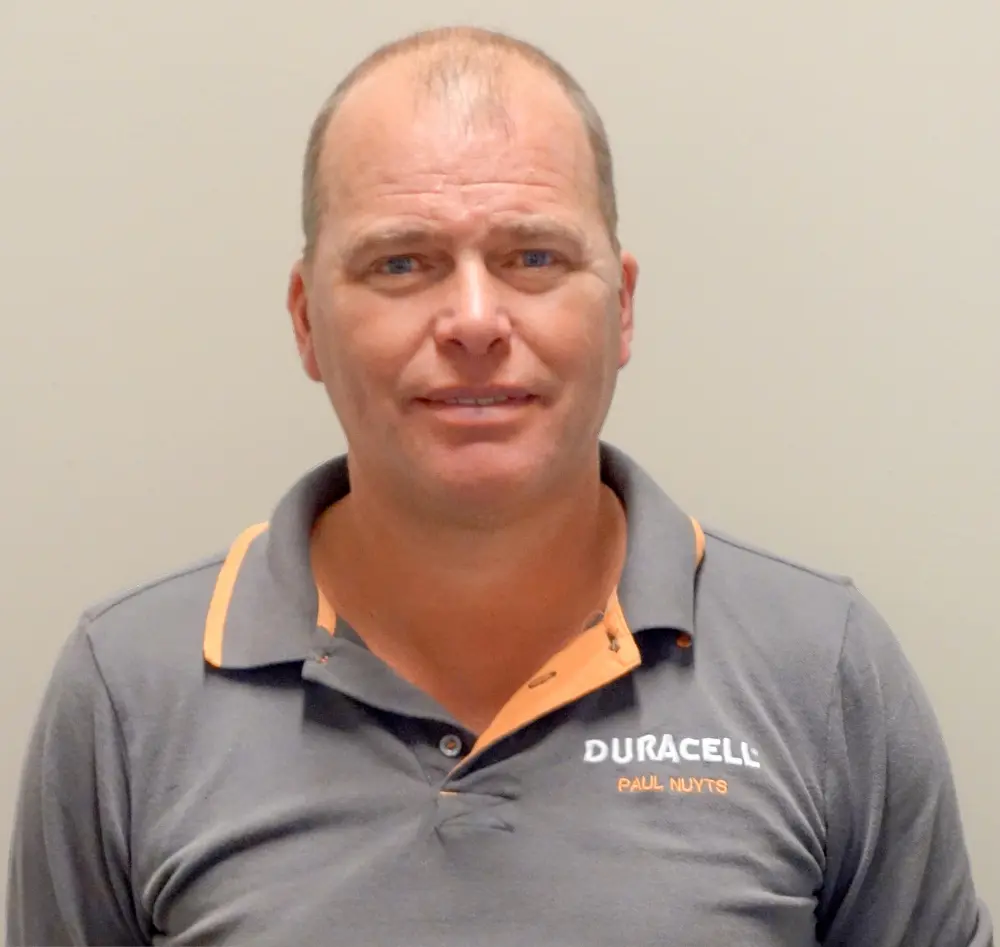
Paul Nuyts, Industry 4.0 project leader chez Duracell Aarschot: « Avec le projet de numerisation paperless, nous economisons quelque 20.000 heures de travail ou 1 million d'euros »
CONCURRENCE EN ORIENT
A ses débuts en 1967, Duracell Aarschot produisait 50.000 piles par an. Aujourd'hui, un demi-siècle plus tard, l'usine produit chaque jour cinq millions de piles AA et AAA pour des appareils ménagers et autres, partant pour d'autres pays européens, le Moyen-Orient et l'Afrique. Sur le plan de la capacité, tout va donc bien. Il y a cinq ans, l'avenir du site d'Aarschot s'est toutefois retrouvé compromis. Une des principales causes était le caractère compact des piles. Elles sont, en effet, ainsi faciles à transporter, ce qui arrange évidemment aussi les concullègues. Sur les cinq sites au total de Duracell (un en Europe, trois aux USA et un en Chine), l'usine sœur en Chine dispose, par ailleurs, aujourd'hui des lignes de production les plus performantes et sur d'autres plans aussi, les résultats y sont au moins aussi bons, voire meilleurs. Tout comme les entreprises occidentales, la Chine travaille avec des fournisseurs locaux et des matériaux moins chers, et privilégie l'automatisation, l'outsourcing des activités non principales et le lean manufacturing. L'époque où les entreprises occidentales pouvaient présenter leurs produits comme supérieurs sur le marché, est révolue.
Comment la firme Duracell pouvait-elle rester compétitive? Devait-elle tout de même continuer de miser sur une meilleure qualité en espérant que l'inflation touche l'Extrême-Orient? Il y a quelques années, la direction de l'entreprise a défini un objectif clairement mesurable: le coût par pile produite à Aarschot (les coûts de transport vers les marchés de vente compris) devait égaler celui de l'usine sœur chinoise. Pour atteindre cet objectif, le système de production de Duracell devait devenir successivement plus rapide et plus intelligent.
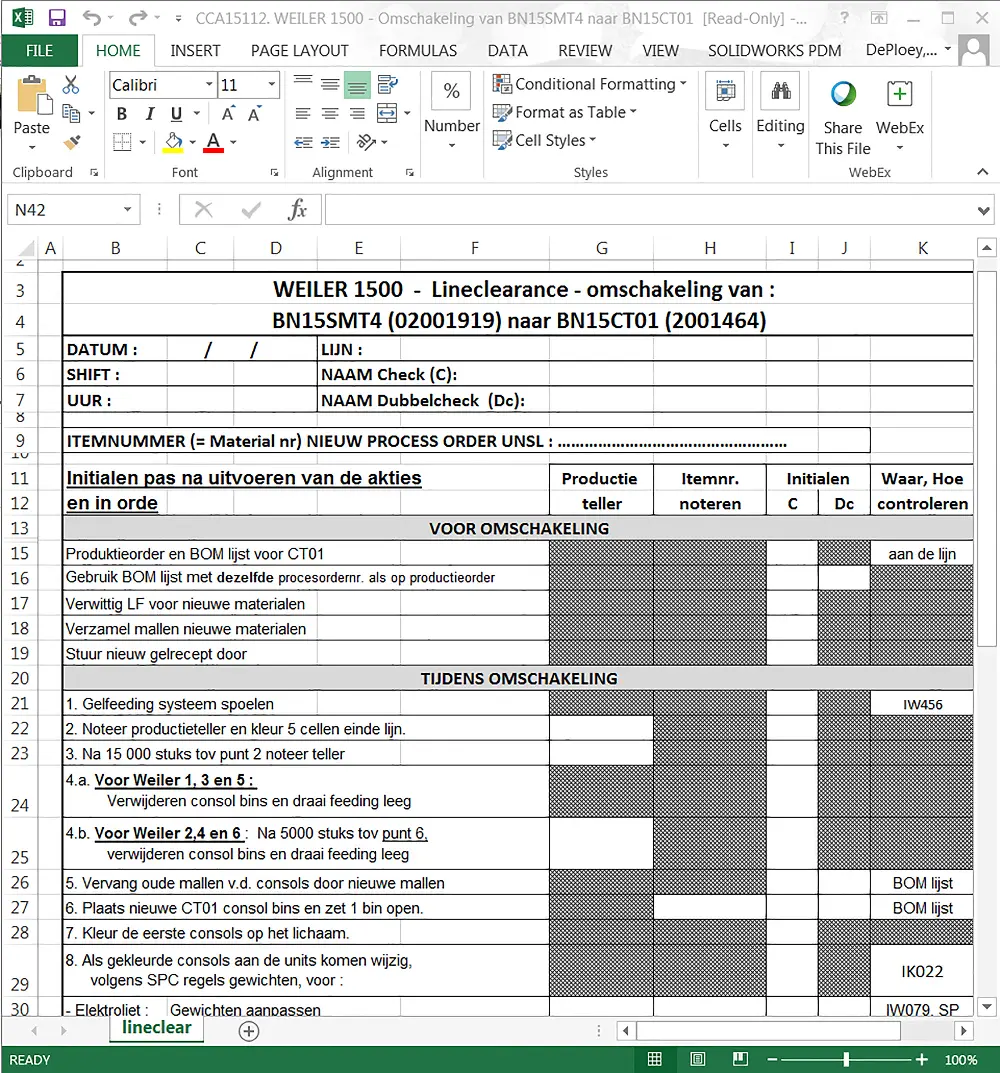
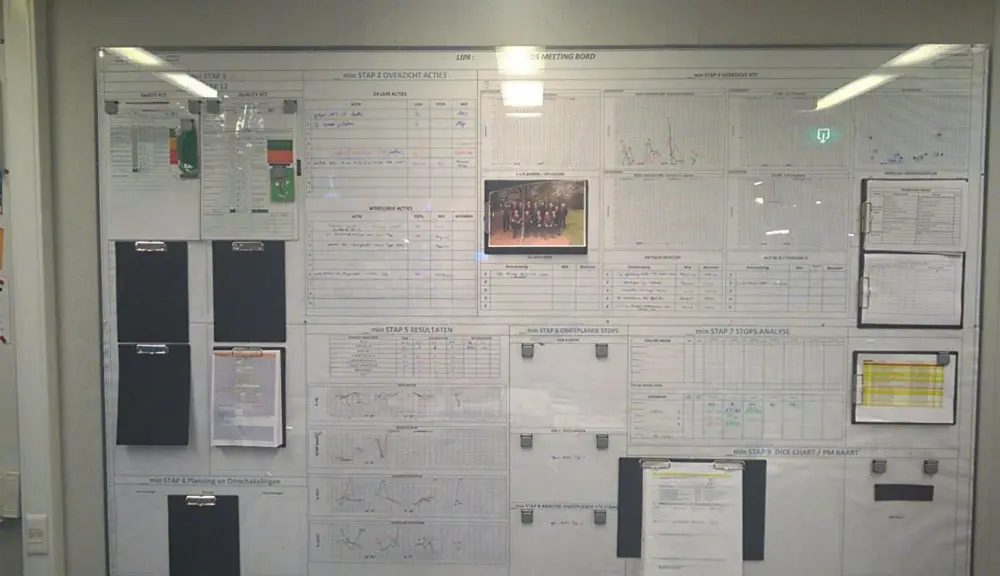
Le 'tableau d'affichage' a été remplacé par une interface portail sur laquelle les opérateurs tiennent une vue d'ensemble en temps réel des tâches exécutées et à exécuter
SYNDROME EXCEL
Début 2016, Duracell Aarschot a examiné ses processus de travail à la loupe pour repérer toutes les opérations administratives sans plus-value. Des problèmes ont ainsi été découverts, qui étaient propres à la complexité des processus de travail, au travail avec des systèmes commandés par l'homme et aux systèmes d'exploitation séparés (ERP, WMS, MES, …). Un constat important: dans certains cas, jusqu'à 20.000 heures étaient consacrées au traitement des documents. Une part importante de l'administration reposait jusqu'il y a peu sur Excel et toutes sortes de formulaires. Par département (sales, procurement, warehousing, …), des key users étaient désignés pour introduire les données et les reporter entre différents progiciels. « C'était la seule manière de pousser des informationsà travers notre chaîne de valeur », commente Paul
Nuyts, Industry 4.0 project leader sur le site d'Aarschot. Certaines données devaient être retapées ou imprimées plusieurs fois, adaptées, scannées et envoyées manuellement. Elles devaient bien sûr aussi arriver à temps et chez la/les bonne(s) personne(s). De plus, les gens commettent parfois des erreurs coûteuses (imaginez une virgule mal placée dans un document de paiement, ...). Si des données doivent être reprises souvent manuellement, le risque de telles erreurs augmente. En outre, on peut consacrer beaucoup de temps à des échanges de mails et de coups de téléphone avec des questions pour des éclaircissements ou des rectifications. Avant, chaque département pouvait, en fait, être considéré comme une île. Les informations sur le planning de production, le warehousing, etc., stockées dans des fichiers Excel ou autres, devaient à chaque fois être demandées via une des différentes interfaces non couplées.
PORTAILS D'EQUIPE
Le défi consistait à passer d'un système de pull information à push information. Au lieu de faire chercher des informations via une multitude d'interfaces, Duracell voulait présenter les informations sous la bonne forme et au moment nécessaire à celui ou ceux devant en disposer. Ometa propose une plate-forme d'intégration couplant les applications d'entreprise comme les systèmes d'ERP et de production à des systèmes portails ou à un CMS - dans ce cas Microsoft SharePoint. Toutes les informations sur le planning de production, les quantités de production, les pourcentages de déchets, l'entretien, le contrôle de sécurité et de qualité, qui étaient traitées avant manuellement à différents endroits, peuvent ainsi circuler directement et automatiquement vers SharePoint. Via leur poste de travail numérique, les différentes équipes sont en contact et peuvent tirer des sous-systèmes avec lesquels l'interface est en liaison, les informations de processus nécessaires en temps réel.
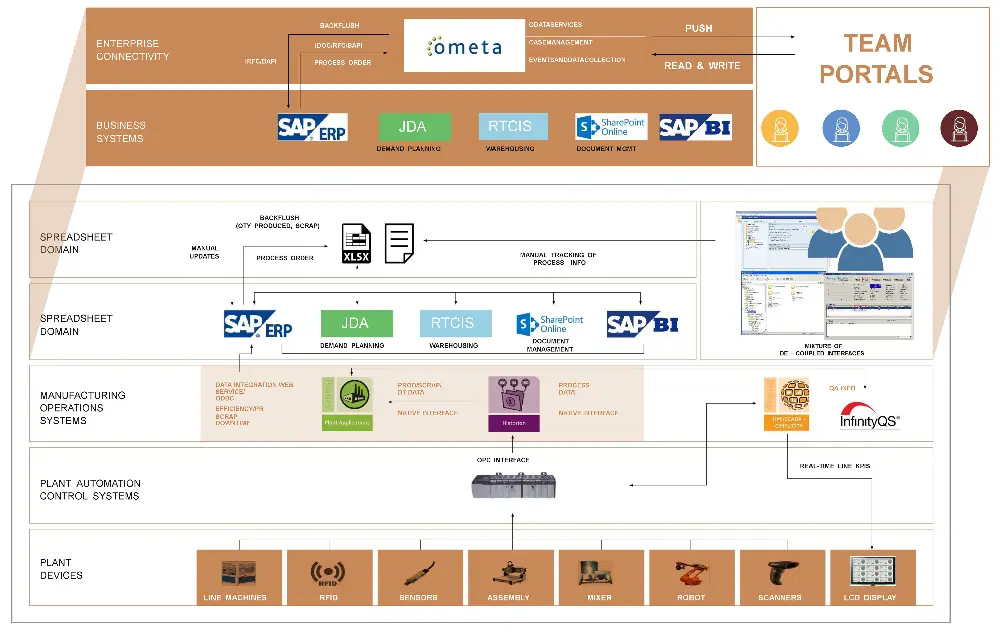
Avant, les informations devaient être cherchées via une des différentes interfaces non couplées (en dessous). A présent, les informations nécessaires sont présentées au bon moment en temps réel via des portails
DIGITAL TWIN
Chez Duracell, chaque pile subit pendant le processus de production neuf transformations différentes cruciales pour la qualité du résultat final. Chacune est donc surveillée étroitement. Caméras, capteurs, RFID, robots, mélangeurs et autres sur les lignes de production collectent une masse de mégadonnées sur une dizaine de paramètres critiques. Vu qu'encore trop des données stockées restent inexploitées ('silos de données'), Duracell veut doter chaque pile d'un 'digital twin' avec toutes sortes de données collectées couplées sur les WMS, MES, ERP, série de produits, données de machine, données de composant, ... S'il est possible de déterminer pour chaque pile sur la base de ce jumeau virtuel si elle répond à tous les critères de qualité, il n'y aura plus besoin par la suite d'échantillons par lot pour analyse en laboratoire, ce qui permettra de gagner du temps. Les opérateurs pourront aussi intervenir à temps dans le processus et contribuer ainsi à réduire la quantité de déchets de production.
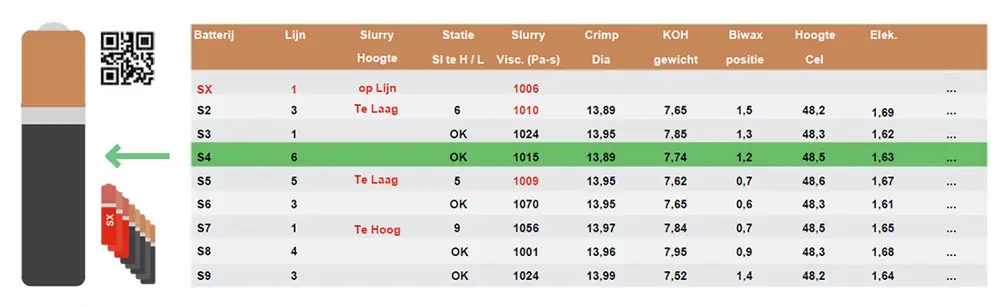
Le 'digital twin' d'une pile physique rend les contrôles d'échantillons visuels superflus (processus de contrôle plus court) et réduit les déchets
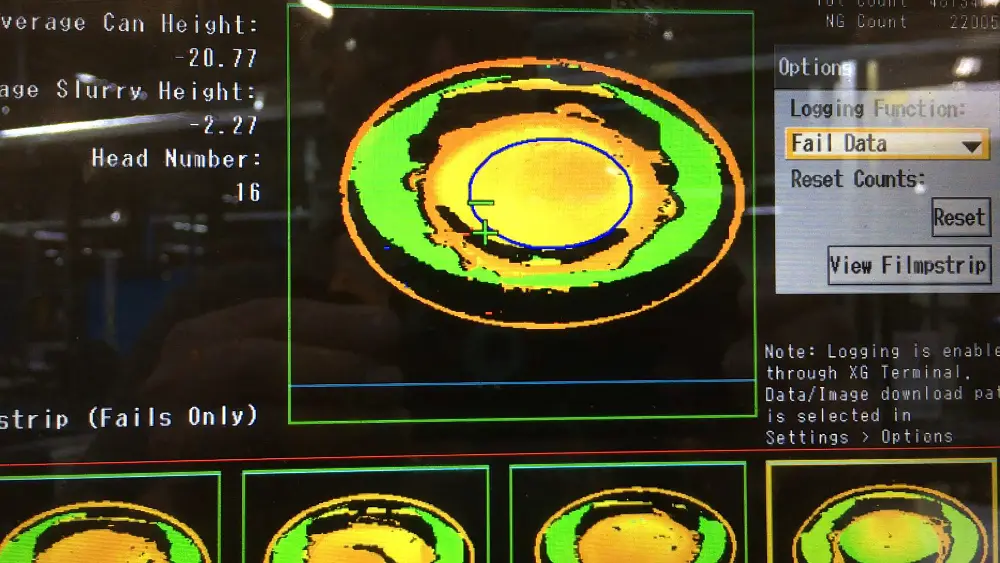
MACHINE LEARNING POUR LA PREDICTION
En guise de projet pilote, Duracell décidait d'appliquer le machine learning sur les lignes de production pour le composant d'anode des piles. On envisageait, au T1 de 2018, de numériser chaque cellule individuelle par transformation via des caméras et des scanners à laser intelligents sur les lignes. Parallèlement, l'entreprise passait d'un nettoyage manuel à l'eau à un nettoyage au laser et alors qu'avant, les dommages éventuels n'étaient contrôlés visuellement que sur quelques échantillons, il y avait à la place un contrôle basé sur laser en ligne de toutes les piles. Aussi dans cette période, on s'attellerait aussi au digital twin en temps réel. Là, la surveillance des paramètres critiques donnerait lieu à plus de 180 millions de points de données sur la base desquels des prévisions seront faites pour réduire les arrêts et déchets inutiles. Au T2 de 2018, on travaillerait à structurer les données en temps réel. Avec l'introduction de la norme OPC UA, même les programmes autres que Windows pourraient communiquer avec le hardware industriel.
Au printemps 2019, l'attention se concentrerait sur l'assistant numérique. Maintenant, les opérateurs reçoivent déjà leurs tâches via les écrans de PC et tablettes. Ici, la priorité est indiquée au moyen de couleurs (rouge pour les tâches urgentes, ...). Ils cochent les tâches finies, ce qui est traité automatiquement sur SharePoint et affiché via les tableaux de bord.
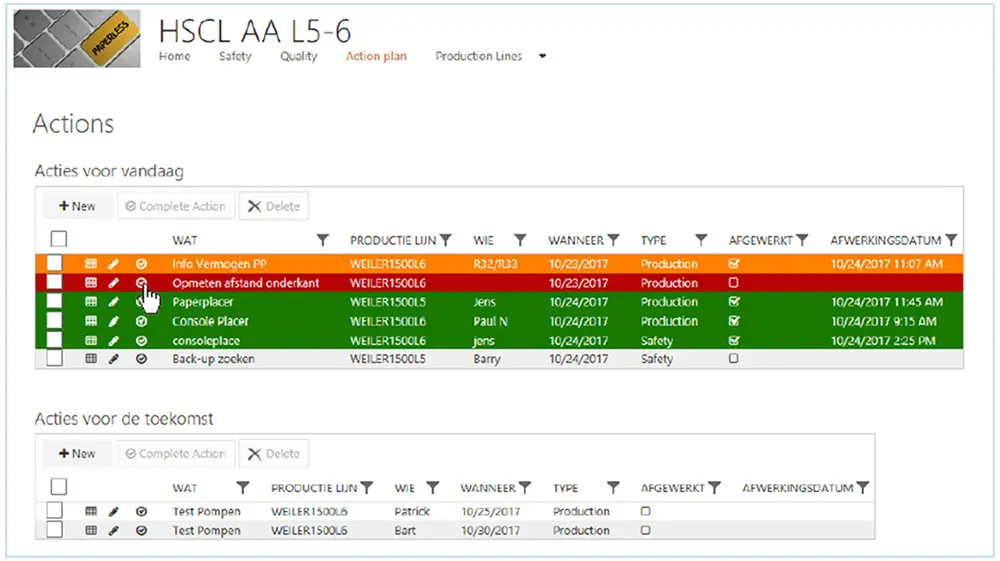