JAN DE NUL GROUP CONSTRUIT UN QUAI DE 800 M DE LONG AU PANAMA
“L'interaction entre civil et dragage a permis de travailler plus vite et pour moins cher"
A la fin de l'année, l'entreprise de dragage et de construction Jan De Nul Group livrera un quai de 800 m de long au Panama pour la Port of Singapore Authority (PSA). Grâce au nouveau complexe d'écluses, des navires transportant jusqu'à 12.000 conteneurs peuvent naviguer sur le canal. Les quais existants devaient dès lors être adaptés à la nouvelle situation. La construction du mur de quai a été mise sur le marché en cinq volets. Pour trois d'entre eux, ils ont fait appel à Jan De Nul Group. InfraStructure s'est entretenu avec Emmanuel Lemaire, responsable du suivi du projet.
NOUVEAU COMPLEXE D'ECLUSES
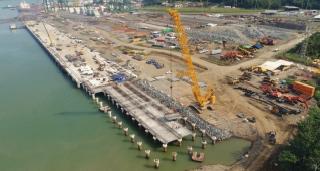
CINQ VOLETS
L'extension du quai existant a été divisée en cinq parties. “Il y avait tout d'abord l'amélioration du sol sur le futur terrain à conteneurs", explique Emmanuel Lemaire. “La deuxième partie englobait les travaux de dragage. Ensuite, la construction du quai proprement dit était programmée, suivie de l'achat et de l'installation des grues à conteneurs. Et enfin, le terrain à conteneurs devait aussi être aménagé avec un revêtement en béton, un système de drainage et des bâtiments de service. La première phase n'était absolument pas superflue. La composition du sol est, en effet, très hétérogène, allant de sol très meuble à du basalte dur. Aux endroits faibles, nous avons placé tous les 1,2 m des tuyaux de drainage verticaux. Nous avons comprimé le sol et via le drainage, nous avons pompé l'excédent d'eau. Nous avons ainsi comprimé 23 m de sol mou avec plus de 1 mètre. L'ensemble était ainsi suffisamment stable pour pouvoir supporter les charges d'un terrain à conteneurs sans tassements."
GAIN DE TEMPS GRACE A LA COMBINAISON DE CIVIL ET DRAGAGE
Le deuxième et le troisième volets du marché confiés à Jan De Nul étaient les travaux de dragage d'une part et la construction du quai d'autre part. “Le client avait prévu un mode de construction conventionnel, consistant à construire des pieux dans l'eau depuis un ponton ou une plate-forme de levage pour placer dessus un tablier en béton. Mais justement en raison de la diversité de la composition du sol à l'endroit concerné, nous avons proposé au client une autre méthode de travail. Notre proposition consistait à construire une digue de manière à pouvoir creuser l'espace intérieur au sec. Dans le cadre de l'aménagement des écluses sur le canal de Panama, nous avons déplacé 20 millions de mètres cubes de terre. Presque tout le propre matériel était déjà présent au Panama. Nous avons investi dans une foreuse LB36 et dans un blondin avec une capacité de 600 tonnes."
SITUATION GAGNANT-GAGNANT
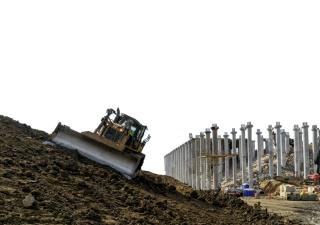
COMPLEXE D'ÉCLUSES AU PANAMA
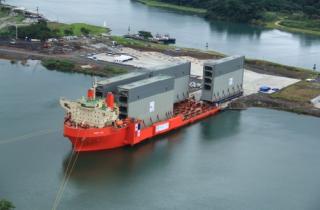
614 PIEUX
La construction du quai semble assez simple à décrire. Il est constitué de cinq rangées de pieux (561 au total) sur 800 m, sur lesquels est placée une plate-forme de 35 m de large composée de grands éléments préfabriqués en béton
1.000 au total pesant jusqu'à 55 tonnes par pièce. Au-dessus des éléments préfabriqués viendra une couche de finition en béton armé coulé sur place. La majorité des pieux ont été réalisés et placés par Soetaert, spécialiste des fondations faisant partie depuis 2015 de Jan De Nul Group. “Le mur de pieux est constitué d'une exécution simple de 375 pieux et d'une exécution complexe de 186 pieux et 53 pieux sécants", explique Emmanuel Lemaire. “Les pieux font 27 à 35 m de long et arrivent jusqu'à env. 6 m au-dessus du niveau de la mer. La différence de longueur est liée aux sols divers où il fallait forer. Chaque pieu que nous forions, était différent, ce qui rendait l'entreprise très complexe. Un poteau était enfoncé jusqu'à 7 m de profondeur dans un sol en basalte, tandis qu'un autre un peu plus loin devait être ancré à bien 20 m de profondeur à cause du mauvais sol. Pour installer les pieux complexes, nous placions d'abord un tube de forage temporaire à env. 12 à 17 m dans le sol. Dans ce tube, nous forions jusqu'à la roche. Une fois celle-ci atteinte, nous changions le diamètre et forions jusqu'au fond du pieu. Puis, nous placions le tube permanent qui allait rester dans le pieu, et nous retirions le tube temporaire. Après avoir nettoyé le fond et le pieu, nous placions les cages d'armature et coulions le béton dans le pieu."
TIMING SERRE
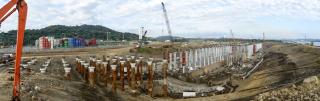
PROPRE CENTRALE BETON SUR CHANTIER
Les éléments préfabriqués sont coulés sur le chantier même. Le béton provient d'une propre centrale à béton installée sur le chantier. “Une centrale à béton exclusive sur le chantier était nécessaire. Sinon, nous aurions dû faire venir tout le béton de Panama City, avec tous les soucis de circulation s'ensuivant. De ce fait, nous n'aurions pu travailler que la nuit, ce qui ne serait pas bon pour le timing. Nous avons aussi composé le mélange de béton. Nos spécialistes ont sélectionné le type et la quantité de ciment nécessaire pour construire les pieux comme le quai. Pour les pieux, il fallait ainsi du béton gras. Il ne pouvait pas être utilisé pour les éléments préfabriqués, car ils penchaient en oblique. Nous avons utilisé ici un mélange de béton différent. Outre les exigences de mise en œuvre, nous avons aussi tenu compte de la résistance à la compression. La durabilité a joué un rôle crucial. Les chlorures dans l'eau de mer ne peuvent pas migrer à travers le béton jusqu'à l'armature. C'est pourquoi nous avons élaboré une composition de béton rendant une telle pourriture du béton impossible. Nous pouvons ainsi proposer une garantie de cinquante ans."
PONTON REGLABLE EN HAUTEUR
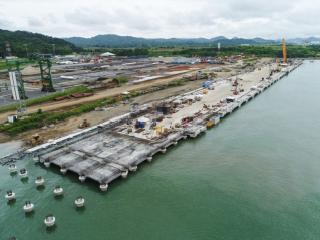
GRAND GROUPE DE COLLABORATEURS PANAMEENS
Pour mener à bien un travail d'infrastructure aussi gigantesque, il faut de la main-d'œuvre. Beaucoup de main-d'œuvre. “Env. 400 ouvriers ont travaillé sur le projet PSA, plus une soixantaine de cadres", précise Emmanuel Lemaire. “Beaucoup d'entre eux étaient des Panaméens, car les règles de travail au Panama sont strictes et protectionnistes. 90% de la charge salariale doit être panaméenne. Nous avons surtout employé des Panaméens. Comme nous sommes actifs en continu dans le pays depuis 2009, nous avons pu constituer un bon groupe de collaborateurs et de cadres. Nous connaissons beaucoup de gens et notre liste a vite été établie. La plupart d'entre eux sont ravis de pouvoir travailler pour Jan De Nul Group. Nous avons la réputation d'être un bon payeur régulier et respectons toutes les obligations légales."
213 MILLIONS DE DOLLARS
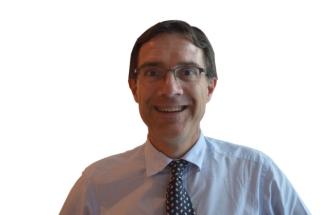