UNE PRODUCTION FLUIDE ET FIABLE CHEZ VOLVO CARS GRACE A DES ACTIONNEURS
De robustes actionneurs Assurent une production fluide et fiable chez Volvo Cars
Volvo Cars à Gand produit une voiture par minute. Un arrêt des machines entraîne donc très rapidement un ralentissement et des pertes de production. Le genre de souci dont on préfère se passer dans un secteur aussi compétitif! La fiabilité des installations revêt donc une importance primordiale. Linak a récemment été impliqué dans un projet destiné à moderniser l'installation où sont assemblés les skids.
ASSEMBLAGE DE SKIDS POUR LE TRANSPORT DE VEHICULES
Ceux qui ont déjà visité les halls de production d'un fabricant automobile, le confirmeront: rares sont les secteurs où l'automatisation est aussi poussée! On a l'impression de voir une seule machine très longue … mais dont la performance est égale à celle du maillon le plus faible de la chaîne.
Il en va de même chez Volvo Cars à Gand, où plus de 5.000 personnes travaillent chaque jour sur des modèles comme la nouvelle XC40, la V40, la S60 et la V60. A Gand, Volvo fabrique près de 250.000 voitures par an. Un chiffre qui donne le tournis!
Les véhicules dans cette longue chaîne de production sont montés sur un châssis spécial. Ces 'skids de laquage' sont des plates-formes qui transportent les voitures à travers la division peinture. Ils sont composés de manière assez simple: deux rails métalliques et différentes traverses plus petites. Ils sont démontés au début du montage final et assemblés au début de la chaîne de laquage. Lors du développement d'un nouveau type de skid pour les modèles CMA actuels, on a décidé de moderniser en profondeur l'installation d'assemblage des skids. Via le general contractor, Stotz Fredenhagen Industries (SFI), c'est Linak qui a été impliqué dans ce projet.
SYSTEME AUTOMATISE
Nous avons discuté avec Marc Vervaeck, ingénieur chez Volvo Cars, du comment et du pourquoi de cette adaptation: “Le premier type de skid que nous composons ici, est pour la plate-forme CMA, c'est-à-dire pour les modèles de véhicule plutôt compacts (e.a. la nouvelle XC40). Le deuxième type de skid s'appelle SPA et sert pour les plus gros modèles que nous produisons de manière plus sporadique. Les deux systèmes utilisent les même poutrelles, mais les traverses sont différentes. L'ancienne installation pour composer ces skids fonctionnait encore, mais lors du démarrage de la nouvelle plate-forme CMA, nous voulions revoir le tout. Ce qui nous embêtait surtout, c'était le principe de fonctionnement plutôt complexe. Il utilisait quatre broches, entraînées par un moteur central. Non seulement chacune de ces broches était reliée séparément au moteur, mais en plus, elles étaient toutes reliées entre elles avec des engrenages, etc. afin de garantir la synchronicité de leur fonctionnement. De plus, les broches avaient déjà cassé à plusieurs reprises et la réparation était difficile et prenait du temps à cause de l'accessibilité réduite. Indépendamment de ça, nous avons aussi rencontré quelques problèmes avec le préhenseur. A cause de la salissure des poutrelles, due à des résidus de peinture, par exemple, celui-ci ne fermait plus bien, ce qui réduisait sa prise.“
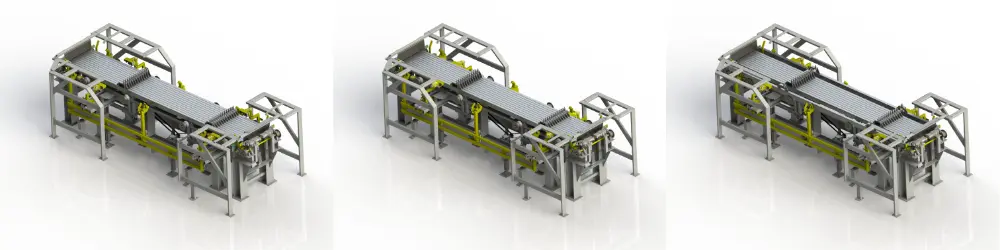
qui sont prises, si bien que la distance jusqu'aux poutrelles suivantes varie
Positionnement précis
Philippe Thuysbaert est responsable Benelux chez SFI, qui a construit la nouvelle ligne d'assemblage de skids pour Volvo Car de Gand. “A l'origine, Volvo a proposé d'adapter légèrement les vieux principes de l'entraînement central et des serrages pneumatiques, mais au final, on a décidé de passer à un nouveau concept. En bref, celui-ci fonctionne comme suit: le treuil extrait automatiquement un lot de douze poutrelles de l'étagère de stockage et les monte sur la nouvelle station de contrôle. La préhension des poutrelles ne s'effectue plus avec un préhenseur pneumatique, mais avec un système à électroaimant. Celui-ci est moins sensible aux salissures sur les poutrelles, ce qui améliore la fiabilité. Dans le processus, ce sont chaque fois les poutrelles situées le plus à l'extérieur qui sont prises, si bien que la distance jusqu'aux poutrelles suivantes varie constamment. L'ensemble se déroule de manière entièrement synchronisée grâce à quatre actionneurs Linak, deux de chaque côté. Ils doivent constamment lisser les différences au niveau de la distance de préhension. Les quatre actionneurs Linak fonctionnent indépendamment, mais ils sont électroniquement reliés, si bien qu'ils peuvent travailler de manière parfaitement synchronisée. Une fois que les poutrelles sont bien positionnées, elles partent vers le poste de travail d'assemblage CMA et SPA, où a lieu le montage des traverses. Pendant ce temps, les poutrelles sont automatiquement contrôlées (il faut qu'elles soient propres et rectilignes), car elles doivent être parfaitement droites pour éviter les problèmes par la suite lors de l'assemblage. Normalement, les skids doivent faire 60 mm de large, mais il arrive parfois qu'il reste de la peinture sur les poutrelles, si bien que la mesure varie de quelques millimètres. Si c'est le cas, elles sont automatiquement illuminées et envoyées vers la station de réalisation pour être nettoyées.
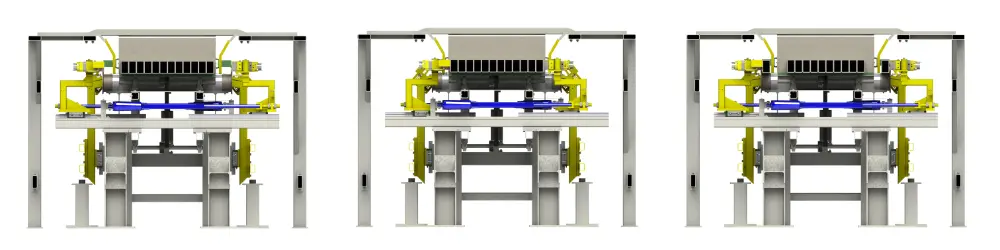
Autrefois, ce contrôle n'était pas effectué, si bien que le nettoyage était soit excessif, soit insuffisant. Aujourd'hui, cette fréquence est optimisée. Le processus de contrôle s'effectue à la demande du client sans perdre un temps de cycle - donc pendant le déplacement des poutrelles. Au niveau du poste de travail, les traverses sont positionnées sur les poutrelles par l'opérateur au moyen d'un manipulateur. Il y a encore un contrôle optique automatique qui vérifie le positionnement correct des traverses.“
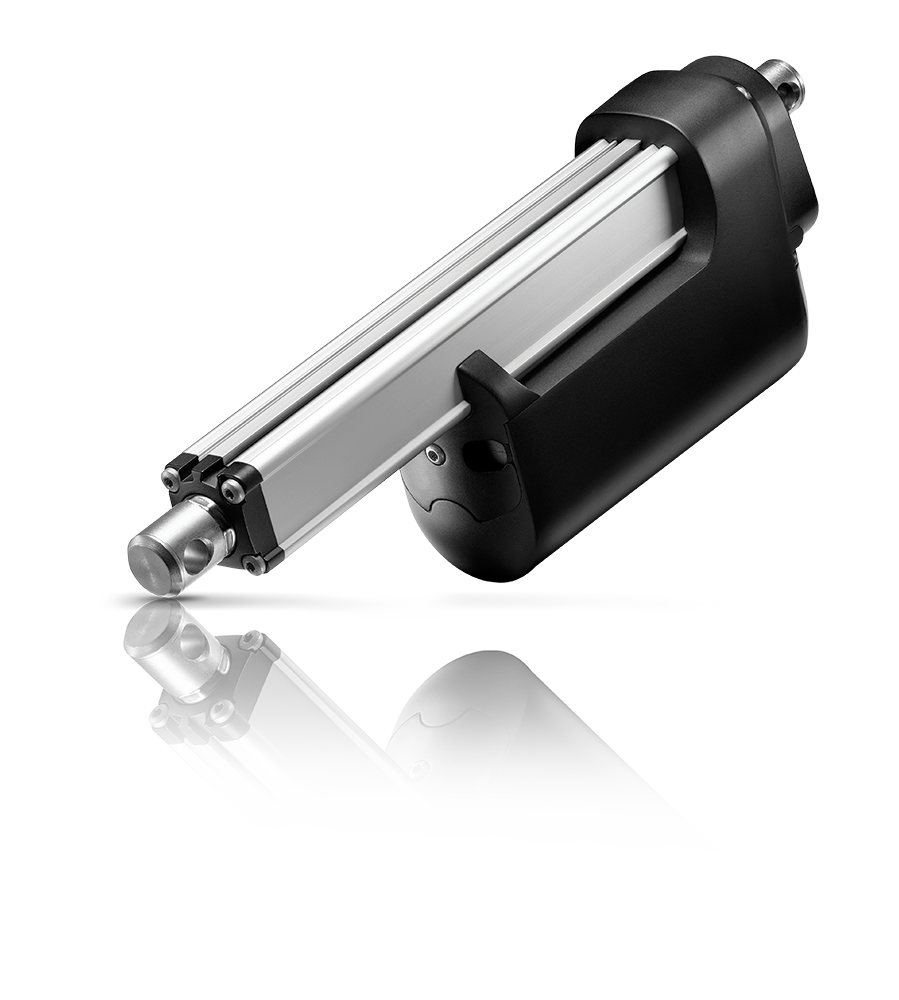
une force de 10.000 N
UN ROLE CRUCIAL POUR LES ACTIONNEURS
Le bon fonctionnement de l'installation dépend du positionnement correct et de la synchronisation des actionneurs. Pour cela, on a fait appel au LA36 de Linak. Nico Planckaert, account manager chez ce fournisseur de composants: "Ce type d'actionneur peut délivrer une puissance de 10.000 newtons. La technique qui se cache derrière, est relativement simple: la base est une broche et un écrou. En fait, c'est le même principe que la technique utilisée pour régler la hauteur des lits d'hôpitaux et des bureaux, sauf que dans ce cas-ci, la réalisation doit être beaucoup plus robuste afin de résister aux vibrations et aux chocs propres à l'industrie. Bien sûr, il y a aussi beaucoup plus de composants pour le retour d'informations concernant les positions. Mais le principe derrière la synchronisation est une technique directement empruntée au réglage de hauteur des bureaux. La robustesse est garantie par le degré IP élevé. Ces composants sont conçus pour un fonctionnement sans entretien. En théorie, ils peuvent exécuter ces mouvements plusieurs millions de fois. Ils contribuent donc énormément au temps de disponibilité de cette installation.
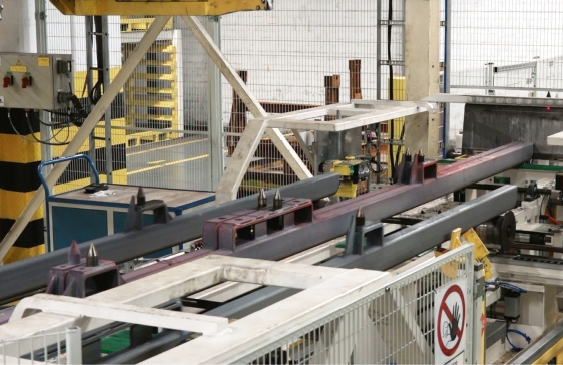
Maintenant, le réglage s'effectue de manière électronique et non plus mécanique. Si une pièce est défectueuse, l'adaptation se déroule plus facilement. De plus, on n'a délibérément pas opté pour la synchronisation sur nos appareils proprement dit, même si c'est parfaitement possible grâce à l'intégration d'électronique. On a choisi un drive séparé dans le coffret qui synchronise la commande. Pour les techniciens de maintenance, c'est plus clair lorsqu'il s'agit d'effectuer un dépannage.“
Philippe Thuysbaert embraie: “Ces dix dernières années, beaucoup de choses ont changé dans l'industrie. L'automobile est devenue beaucoup plus complexe. Les exigences sont nombreuses: le temps de réalisation doit être plus court, le nombre de fournisseurs autorisés est limité et il faut respecter des délais de livraison. Au niveau de la sécurité aussi, la situation s'est durcie. Cette installation en est un bel exemple. Avec l'ancienne commande pneumatique, les cylindres ne pouvaient pas être sous pression. Il fallait donc toujours commencer par transformer l'énergie résiduelle avant de pouvoir travailler dans l'installation. Aujourd'hui, ce n'est plus nécessaire avec cette solution Linak qui, en outre, répond avec un bon rapport qualité/prix à la mission confiée: déplacer les poutrelles transversalement de manière synchronisée."
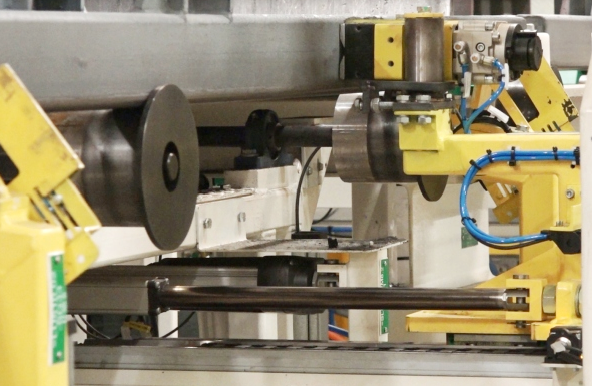
Nico Planckaert: "Quand on travaille pour l'industrie, il faut prévoir un solide boîtier autour du moteur et de la broche. On peut aussi l'utiliser pour y intégrer les commutateurs finaux, un retour de position ou une carte de contrôle complète (digitale ou via un système bus). Ainsi, on obtient un système plug-and-play qui est configuré par nos soins et qui possède un certain degré IP. Il faut juste le raccorder."
Moins de bruit
Outre le fonctionnement rationalisé, la nouvelle installation offre un avantage supplémentaire pour l'opérateur.
Marc Vervaeck: "Autrefois, les manipulateurs fonctionnaient sur la base de la technique sous vide. Il y avait donc une pompe bruyante qui tournait en permanence. Avec le passage à un système pneumatique de la société Tiltech, ce problème est maintenant résolu, si bien que le travail est plus confortable pour l'opérateur.“
PAS LA PREMIERE INSTALLATION POUR SFI
Pour SFI, la modernisation de l'assemblage de skid n'est pas le premier projet chez Volvo Cars à la division peinture. Philippe Thuysbaert nous emmène dans l'espace adjacent, où SFI a réalisé un autre projet et s'est lui-même chargé de l'aspect mécanique et électrique pour le hardware et le software.
“Nous sommes actifs chez Volvo en tant que SFI, mais dès la construction de l'usine, des installations ont été mises en place par le prédécesseur de notre entreprise - tant Stotz que Fredenhagen."
Rachat et activité mondiale
Plus tard, Fredenhagen a été rachetée par Stotz et le nom a été changé en SFI. SFI est actif au niveau mondial dans l'industrie automobile avec des installations clé-en-main, dont tous les modèles possibles de systèmes de transport internes; lignes de montage; entrepôts automatiques, et en dehors de l'automobile, les activités vers le turnkey recycling et les installations de récupération d'énergie sont élargies. “Selon moi, le Skid Loading et les installations de surcharge pour CMA et SPA sont l'une des installations les plus complexes que nous ayons réalisées ces dernières années. Dans ce processus, les skids du bodyshop sont échangés automatiquement par un skid navette, qui sert à transporter les véhicules à travers les bains de nettoyage et de dégraissage. Ces skids CMA ou SPA sont automatiquement vissés par le bas aux différents modèles de véhicules. Ici, nous nous sommes occupés de tout: mécanique, PLC, software, et les installations fonctionnent avec une fiabilité de 99,5%.“
TRAVAILLER POUR L'INDUSTRIE AUTOMOBILE
Le projet chez Volvo Cars est le premier avec des actionneurs Linak. Nico Planckaert: “Les entreprises comme Volvo Cars travaillent avec une liste de fournisseurs agréés afin de garantir une certaine uniformité. Ici, on ne trouvera pas cinq fournisseurs de robots ou de PLC différents, car cela deviendrait difficile pour les services de maintenance.
Pour les actionneurs aussi, il y avait une liste de fournisseurs. Nous n'y figurions pas. Il faut posséder les bons papiers pour en faire partie, car il faut convaincre plusieurs départements de la qualité du produit qu'on propose."